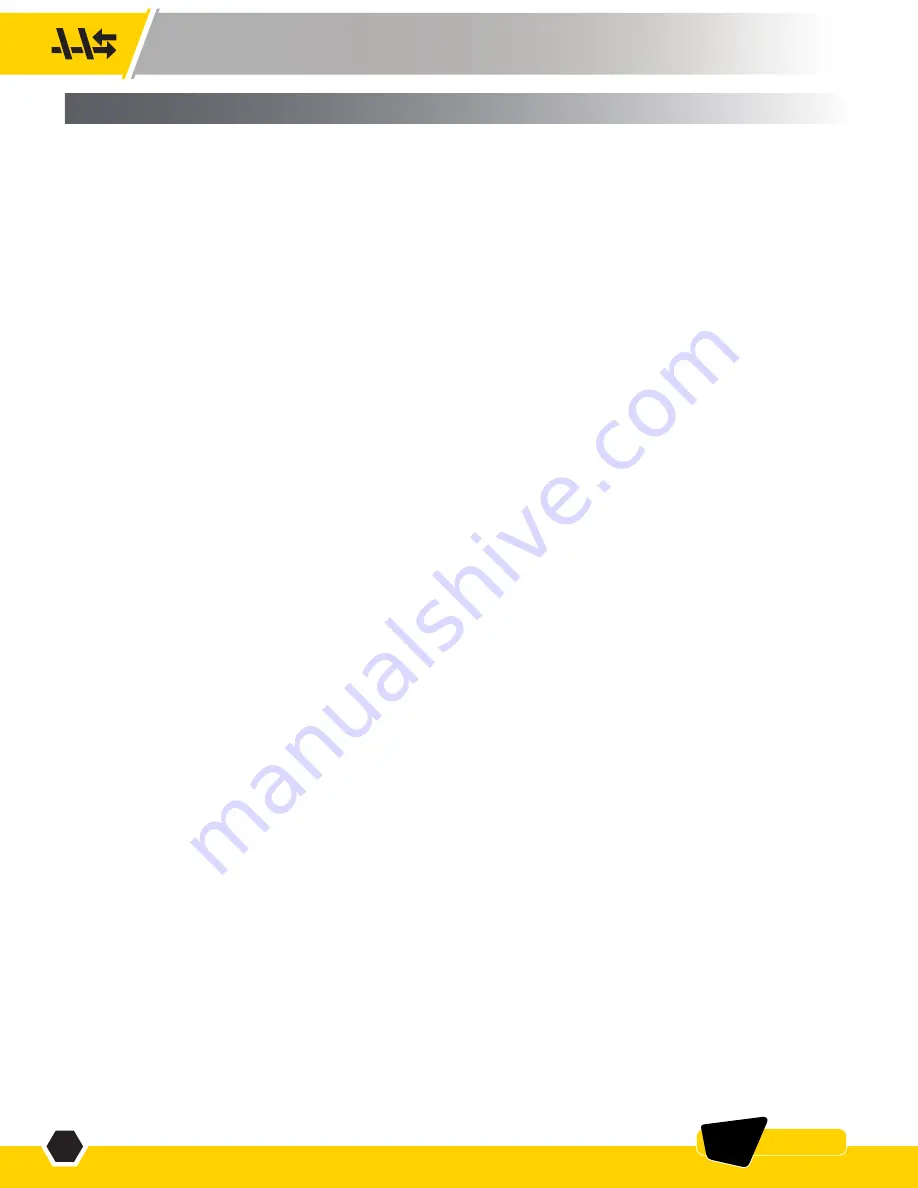
8
Customer Service
(704) 841-6000
www
.apolloflowcontrols.com
“Apollo”
Flow Controls
INSTALLATION, OPERATION & MAINTENANCE
MANUAL
NOTE: It is important that the DCV device be tested periodically in compliance with local codes, but at least once a year or more, as
service conditions warrant.
METHOD 1 (DUPLEX GAUGE)
NOTE: Test set-up is illustrated in Figure 6 for 1/2” through 2” and Figure 7 for 2-1/2 through 10”.
EQUIPMENT REQUIRED:
Double check backflow preventer test kit.
NOTE: All connections must be free from leaks in order to achieve accurate readings during testing.
TEST NO. 1:
PURPOSE:
TO TEST CHECK VALVE #1 FOR TIGHTNESS AGAINST REVERSE FLOW.
REQUIREMENT:
The valve shall permit no through leakage in a direction reverse normal flow under all conditions of a pressure differential.
PROCEDURE:
1. Bleed water through all four test cocks to flush any foreign material.
2. Connect the “high” side hose to test cock #2. Connect the “low” side hose to test cock #3.
3. Open test cocks #2 and #3. Bleed both hoses, making sure to bleed the low side last.
4. Close #2 shut-off valve, then close #1 shut-off valve.
5. Slowly open by-pass valve #1 and lower the pressure at test cock #2 approximately 2 psi below the pressure at test cock #3. Note: Due to check
valve disc compression, both “high” and “low” side gauges may drop at the same rate approximately 10-15 psi or more. After the check valve
disc compresses fully the required “high” side pressure of 2 psi below the “low” side should be obtainable. If this pressure differential can be
maintained then check valve #1 is reported as “tight” or “okay”. Proceed to test no. 2. However, if this pressure differential cannot be maintained
proceed to step no. 6.
6. Open #1 shut-off valve to repressurize the device.
7. Loosely attach the vent hose to test cock #1. Bleed all air from the gauge and vent hose by opening bypass valve #2. Close by-pass valve #2,
tighten vent hose. Open test cock #1.
8. Close #1 shut-off valve.
9. Loosen the “low” side hose at test cock #3 and lower the pressure in the assembly approximately 10 psi. Retighten hose.
10. Simultaneously open by-pass valves #1 and #2 very slowly. If the check valve is holding tight the “high” side gauge will begin to drop while the
“low” side gauge will rise. Close both bypass valves. If a small (no more than 5 psi) pressure differential is created and held, then the check valve
is reported as “tight” or “okay.” If a pressure differential cannot be maintained the check valve is reported as leaking.
TEST NO. 2:
PURPOSE: TO TEST CHECK VALVE #2 FOR TIGHTNESS AGAINST REVERSE FLOW.
REQUIREMENT:
The valve shall permit no through leakage in a direction reverse to normal flow under all conditions of a pressure differential.
PROCEDURE:
1. Same as test #1 except the “high” side hose is connected to test cock #3 and the “low” side connected to test cock #4.
RESTORE OPERATION:
1. Close all test cocks. Remove testing equipment. Open shut-off valves #1 and #2.
VIII. TESTING PROCEDURES