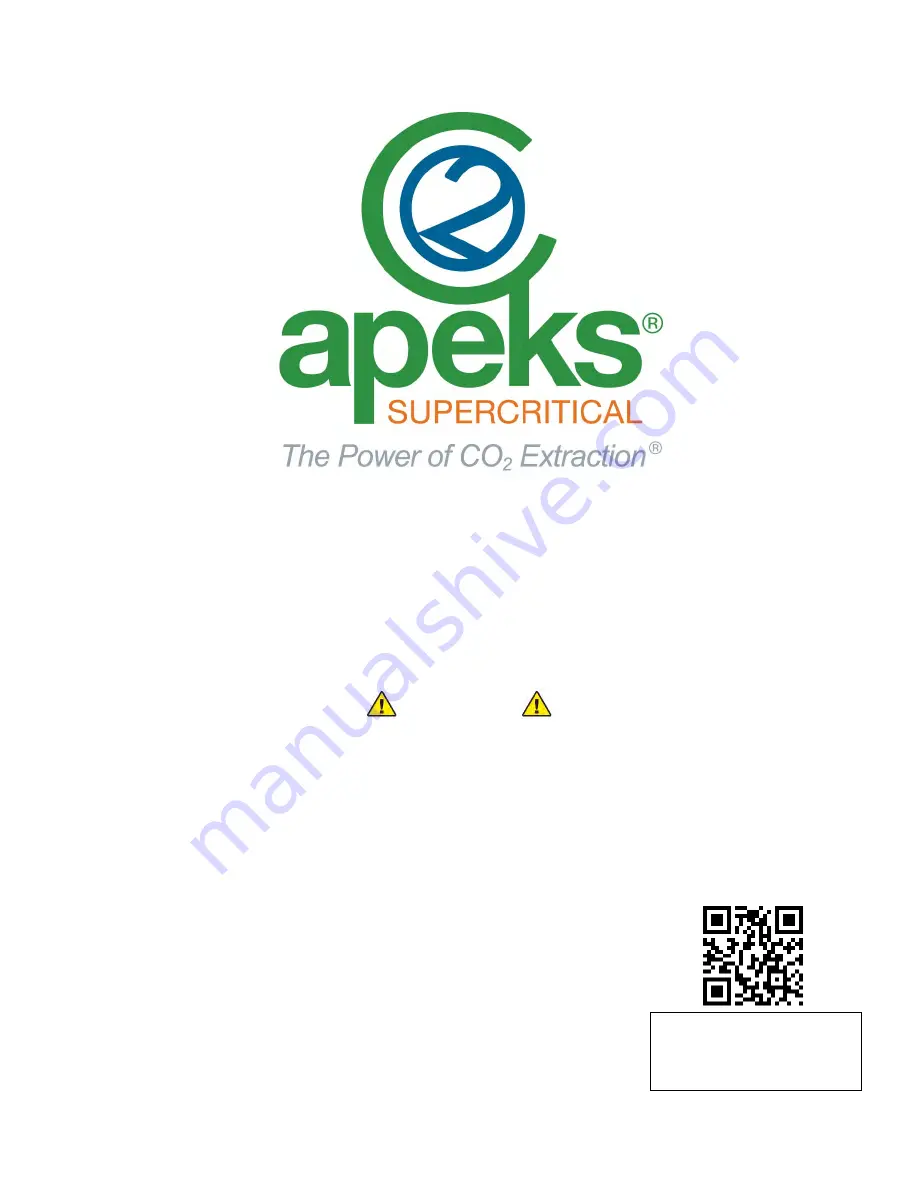
Updated 04/23/2019
©Apeks, LLC 2019
THE
FORCE™
2-STAGE
5000PSI
B
OTANICAL
O
IL
E
XTRACTION
S
YSTEM
O
PERATION
M
ANUAL
WARNING
FAILURE TO FOLLOW THE SET UP AND OPERATION PROCEDURE
PROVIDED IN WITHIN THIS MANUAL MAY VOID THE EXTRACTION
SYSTEM’S WARRANTY
Apeks Supercritical
150 Commerce Blvd.
Johnstown OH 43031
740-809-1160
www.apekssupercritical.com
Scan this QR code to get the
most recent version of the
operating instructions.
Содержание THE FORCE 2-STAGE
Страница 21: ...The Force 2 Stage Operation Manual 21 Revision Date 4 23 2019 2 2 9 3 PLC Analog Inputs...
Страница 22: ...The Force 2 Stage Operation Manual 22 Revision Date 4 23 2019 2 2 9 4 PLC Analog Outputs...
Страница 43: ...The Force 2 Stage Operation Manual 43 Revision Date 4 23 2019 Suction Check Valve Springs Poppet...
Страница 45: ...The Force 2 Stage Operation Manual 45 Revision Date 4 23 2019 7 4 Appendix D Piping and Instrumentation Diagram...
Страница 46: ...The Force 2 Stage Operation Manual 46 Revision Date 4 23 2019...
Страница 47: ...The Force 2 Stage Operation Manual 47 Revision Date 4 23 2019...
Страница 48: ...The Force 2 Stage Operation Manual 48 Revision Date 4 23 2019 7 5 Appendix E CO2 Phase Diagram...
Страница 53: ...The Force 2 Stage Operation Manual 53 Revision Date 4 23 2019...
Страница 54: ...The Force 2 Stage Operation Manual 54 Revision Date 4 23 2019...
Страница 55: ...The Force 2 Stage Operation Manual 55 Revision Date 4 23 2019...
Страница 56: ...The Force 2 Stage Operation Manual 56 Revision Date 4 23 2019...
Страница 57: ...The Force 2 Stage Operation Manual 57 Revision Date 4 23 2019 Z...
Страница 58: ...The Force 2 Stage Operation Manual 58 Revision Date 4 23 2019...
Страница 59: ...The Force 2 Stage Operation Manual 59 Revision Date 4 23 2019...
Страница 60: ...The Force 2 Stage Operation Manual 60 Revision Date 4 23 2019...
Страница 61: ...The Force 2 Stage Operation Manual 61 Revision Date 4 23 2019...
Страница 62: ...The Force 2 Stage Operation Manual 62 Revision Date 4 23 2019...
Страница 63: ...The Force 2 Stage Operation Manual 63 Revision Date 4 23 2019...
Страница 64: ...The Force 2 Stage Operation Manual 64 Revision Date 4 23 2019...
Страница 65: ...The Force 2 Stage Operation Manual 65 Revision Date 4 23 2019...
Страница 66: ...The Force 2 Stage Operation Manual 66 Revision Date 4 23 2019...
Страница 67: ...The Force 2 Stage Operation Manual 67 Revision Date 4 23 2019...