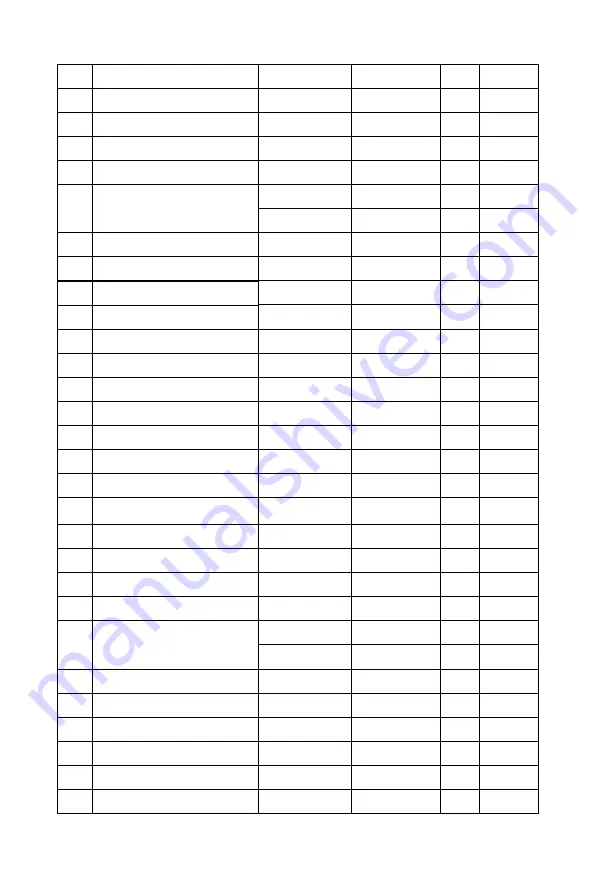
30
746001-00101
746001-00019
1
415V
27
electromagnetic valve
752001-00014
752001-00014
1
28
Back panel
262011-00738
262011-00738
1
29
Fuse holder
740007-00004
740007-00004
1
30
Circuit breaker cover
766003-02217
766003-02217
1
31
Cable
769001-00288
769001-00289
1
380/415V
769001-00026
769001-00027
1
400V
32
Control socket
740001-00184
740001-00184
1
33
Control socket
740003-00012
740003-00012
1
34
Fan cover
766003-02403
766003-02403
1
35
Right side panel
262023-00585
262023-00585
1
36
Bottom plate
262065-00067
262065-00067
1
37
Filter capacitor
722001-00070
722001-00070
2
38
Input capacitor bracket
766002-00104
766002-00104
1
39
Rack Capacitor Board
220293-00009
220293-00009
1
40
High frequency box assembly 220263-00001
220263-00001
1
41
High leakage transformer
763003-00018
763003-00018
1
42
Arc ignition plate assembly
220575-00003
220575-00003
1
43
Step-up transformer
components
220431-00060
220431-00008
1
44
Output reactor
763004-00041
763004-00041
1
45
current sensor
753001-00064
753001-00020
1
46
Polypropylene capacitor
722001-00067
722001-00067
1
47
IGBT protection board
220005-00164
220005-00135
1
48
Varistor
720021-00017
720021-00017
1
380/400V
720021-00021
720021-00021
1
415V
49
Three-phase rectifier module
735005-00002
735005-00003
1
50
IGBT module
735007-00048
735007-00038
2
51
Temperature relay
745008-00006
745008-00006
1
52
IGBT radiator
264005-00028
264005-00033
1
53
Radiator bracket
766002-00091
766002-00090
1
54
Output diode Radiator
264011-00121
264011-00116
1
Содержание ATIG315P
Страница 1: ......
Страница 29: ...28 4 10 Disassembly and reassembly Fig 4 10 1 Disassembly and reassembly ...