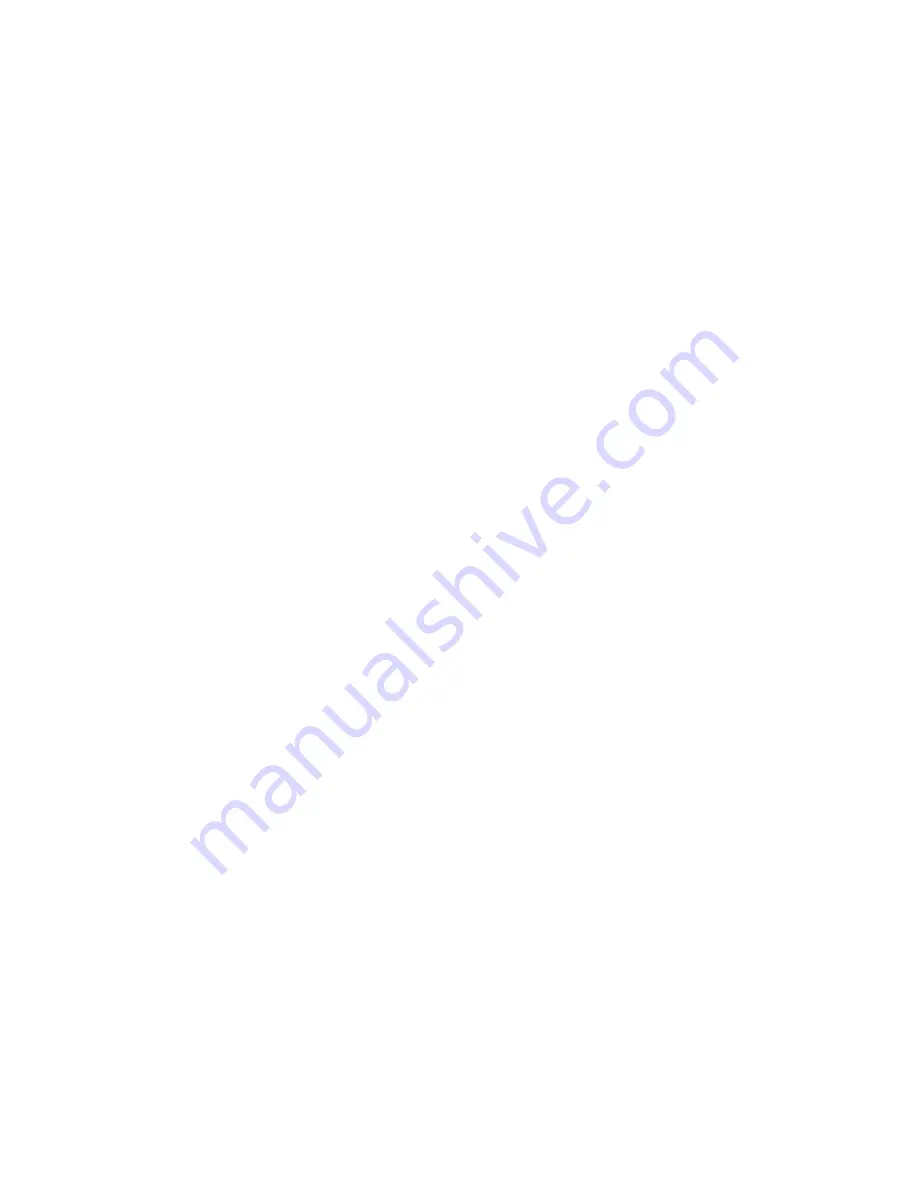
12
ANGI OPERATION AND SERVICE MANUAL
Rev
2006/06
6. MAINTENANCE
6.1 RECOMMENDED PREVENTATIVE
MAINTENANCE SCHEDULE
ANGI has developed a preventative maintenance
schedule for this equipment based on number of
hours of operation. Adhering to this schedule will
minimize unscheduled downtime and assure long
machine life.
This maintenance schedule is summarized in the
Preventative Maintenance Table
included in the
Appendix in this section. The maintenance
intervals in this table are based on the hours of
operation displayed on the control panel hour
meter. When using this table, refer to the Service
Specifications in this manual for detailed servicing
procedures and considerations.
This table has been set-up based on nominal
operating conditions and will need to be
altered for harsh operating environments
.
When performing any maintenance, lock out
the controls to prevent inadvertent starting.
6.2 SERVICE SPECIFICATIONS
6.2.1 COMPRESSOR CRANKCASE LUBE
SYSTEM
6.2.1.1. Compressor Lubrication Spec.
See Compressor Operation & Maintenance
Manual for the correct lubrication specifications.
The compressor is shipped with Polyglycol
lubricant in the crankcase on all North
American orders. DO NOT MIX with Petroleum
based oils.
International shipments have diester synthetic
oil in the crankcase. Diester synthetic will mix
with petroleum oils.
6.2.1.2. Compressor Crankcase Lube Level
A sight glass is provided on the auxiliary end of the
crankcase that identifies the lubrication level. The
oil should always be replenished by removing the
breather cap and adding oil through the top cover.
DO NOT ADD OIL WHILE THE COMPRESSOR
IS RUNNING
The oil level should be filled 2/3-3/4 of the sight
glass. DO NOT OVERFILL THE CRANKCASE
SUMP. After running the compressor, it may be
necessary to add oil to the crankcase sump to
one-half level on the sight gauge, but never must
exceed two-thirds height when the compressor is
primed and running.
Assure that the system has been fully primed
prior to checking oil levels.
6.2.1.3. Compressor Crankcase Oil Pressure
A spring loaded oil pressure regulator is
provided on the compressor. The oil pressure
may be adjusted by removing the cover on the
regulator and turning the adjusting bolt. The oil
pressure has been set by ANGI to the proper
operating pressure of 55-60 psig as measured
on the downstream side of the oil filter.
6.2.1.4. Compressor Crankcase Oil Filtration
A strainer basket and oil filter is provided to
provide filtration. Always replace the oil filter
element and clean the strainer basket when
replacing the crankcase oil.
The strainer basket is located on the auxiliary
end of the compressor frame below the oil level.
Only the replace filter element with a same
grade element. Element replacement interval
should be completed per the Periodic
Maintenance Schedule or any time a 10 psig
pressure drop is detected across the filter.
6.2.2. COMPRESSOR FORCED FEED
LUBRICATION SYSTEM
6.2.2.1. Lubrication Reservoir Level
A separate lubrication reservoir and sight glass
is provided to lubricate the worm gear and cam
on the lubricator.
6.2.2.2. Lubrication Rate
The lubrication feed rate may be adjusted by
turning an adjuster knob on top of the lubricator.
Proper lubrication rate may be confirmed by
observing the indication on the digital no-flow
switch. This switch is mounted to the lubrication
distribution block. Verify that the lubrication rate
by observing the indication and comparing the
rate to that specified on data plate attached to
the lubricator.
6.2.3. COOLING SYSTEM
6.2.3.1 Cooling Fan
The fan blade should be inspected for cracked
or broken blades. Additionally, the blade pitch
should be uniform between blades. Verify that
the fan is not rubbing on the bell or on any fan
guarding.
Never operate the station with missing or
damaged fan blades or without the fan blades
properly installed.