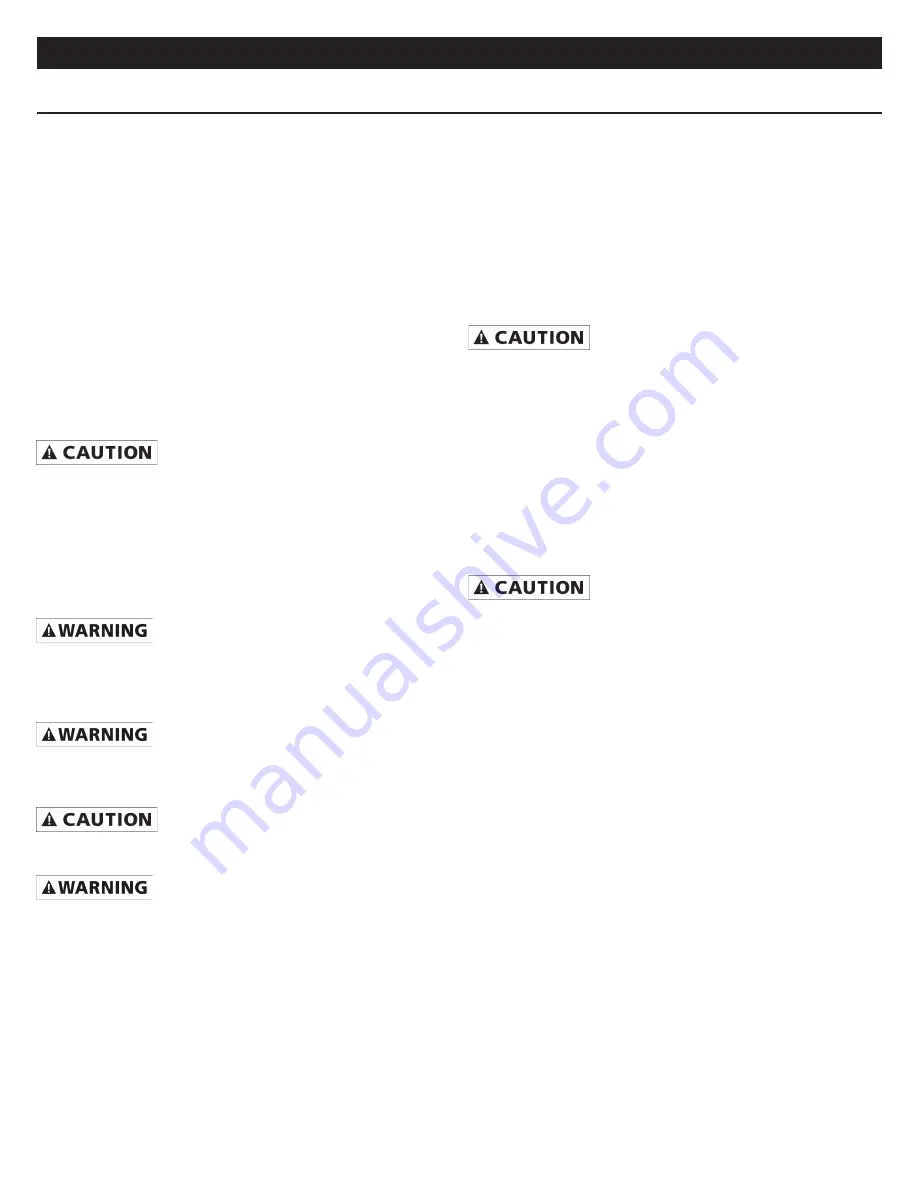
Specifications Information and Repair Parts Manual
569, 570, 571, 572 Series
5690-250-00
2
11/2012
INSTALLING FLANGES
1.
Included with pump: (2) 3” NPT flanges, 2 gaskets, and 4 bolts, nuts, and
washers.
2.
Install flanges on piping using sealing tape or pipe sealant.
3.
Insert gasket into machined groove on pump flange.
4.
Position pump by lining up bolt holes on pump flange with bolt holes on
pipe flange.
5.
Install 4 hex head bolts, nuts, and washers. Torque both flange bolts in
even increments to a value of 8-11 ft-lbs (1.1-1.5 Kg-m). Torque the bolts
in both the suction and discharge flanges in this manner.
OPERATION
1.
Prior to pump start up ensure system is clean and filled with clean liquid
that is compatible with pump components.
2.
Pressurize the pump body slowly. Check for leaks at the flange joint, the
pump casing, and motor shaft.
Pressurize pump casing slowly. Failure to check for leaks at all joints
sealed with a gasket may result in personal injury or property damage.
3. Do not run pump dry! Mechanical shaft seal damage will occur if pump
is run dry. Pump body must be filled with liquid before starting motor. Air
must be vented from the system by means of an air vent located at a high
point in the system.
MAINTENANCE
Make certain that the unit is disconnected and locked out from the power
source before attempting to service or remove any components.
1. System must be drained or pump isolated by turning off suction and
discharge valves before attempting to remove pump.
Water temperature in system can not exceed 100°F (38°C) before
removing or servicing pump. If draining system leave drain valve open
during servicing.
Pump surface temperature can not exceed 90°F (32°C) before removing
or servicing pump.
Loosen flange bolts slightly and shift pump side to side to vent internal
pump casing pressure before removing or servicing pump.
2.
Remove pump from the system by removing four flange mounting bolts,
nuts, and washers.
SHAFT SEAL REPLACEMENT
Refer to figures No. 2
REMOVAL OF OLD SEAL
IMPORTANT
: Always replace both seal seat (Ref. No. 4) and seal head (Ref.
No. 5) to ensure proper mating of components! Also, impeller seal (ref. No. 7)
should be replaced anytime impeller fastener (Ref. No. 8) has been removed.
1. Remove fasteners (Ref. No. 11) connecting casing (Ref. No. 9) to adapter
(Ref. No. 2).
2.
Remove casing. If casing is hard to slide off, use a large flat screwdriver to
pry between cast boss next to casing bolt boss and adapter flange. Take
care not to mar adapter flange machined surface.
Care should be taken not to pinch or “shave” casing seal (Ref. No. 3)
between adapter and casing.
3. Use a box and/or socket wrench to remove impeller fastener. Remove
impeller seal and impeller (Ref. No. 6).
NOTE:
Motor shaft must be held in place to remove impeller. Back of the
motor either has slot in shaft (use large screwdriver to hold or has 2 flats on
motor shaft (use 7/16 open end wrench to hold). Impeller and impeller fastener
unscrew CCW when looking at the bottom of casing.
4. The seal head can now be pulled from shaft.
5. Pry seal seat from adapter.
INSTALLATION OF NEW SEAL
The precision lapped faces on mechanical seal are easily damaged.
Handle your repair seal carefully. Do not touch polished seal faces.
IMPORTANT:
Be sure that shaft should does not damage polished face (See
figure 2).
1. Thoroughly clean all surfaces of seal cavity in adapter.
2. Using a clean cloth, wipe shaft and make certain that it is perfectly clean
3. Wet rubber portion of new seal seat with a light coating of soapy water.
While wearing clean gloves or using a clean light rag, press seal seat
squarely into adapter recess. Use cardboard washer (usually supplied
with new seal), place over polished surface and use a piece of pipe or
dowel rod to press in firmly but gently. Avoid scratching polished face
4. Dispose of cardboard washer. Check again to see that polished face is
free of dirt and all other foreign particles and that it has not been scratched
or damaged.
5. Wet the inside rubber portion of new seal head with a light coating of
soapy water. Slide head onto motor shaft with sealing surface facing seal
seat (see figure 2).
NOTE:
A short “run-in” period may be necessary to provide completely leak-
free operation.
6. Screw impeller onto shaft. Use screwdriver slot at rear of motor shaft
(opposite the threaded end) to tighten impeller.
NOTE
: It may be necessary to remove plug in motor end cap to expose slot.
If removed, be sure to reinstall plug AFTER pump is completely assembled.
7. Check if shaft turns freely by spinning impeller.
8. Slide impeller seal onto exposed shaft screw acorn nut onto shaft and
tighten.
9. Place casing seal in groove on adapter. Wet seal with a light coating of
Patterson/AMT Inline Circulator Pump
Содержание 569 Series
Страница 6: ...Specifications Information and Repair Parts Manual NOTES ...
Страница 7: ......
Страница 8: ...www amtpump com ...