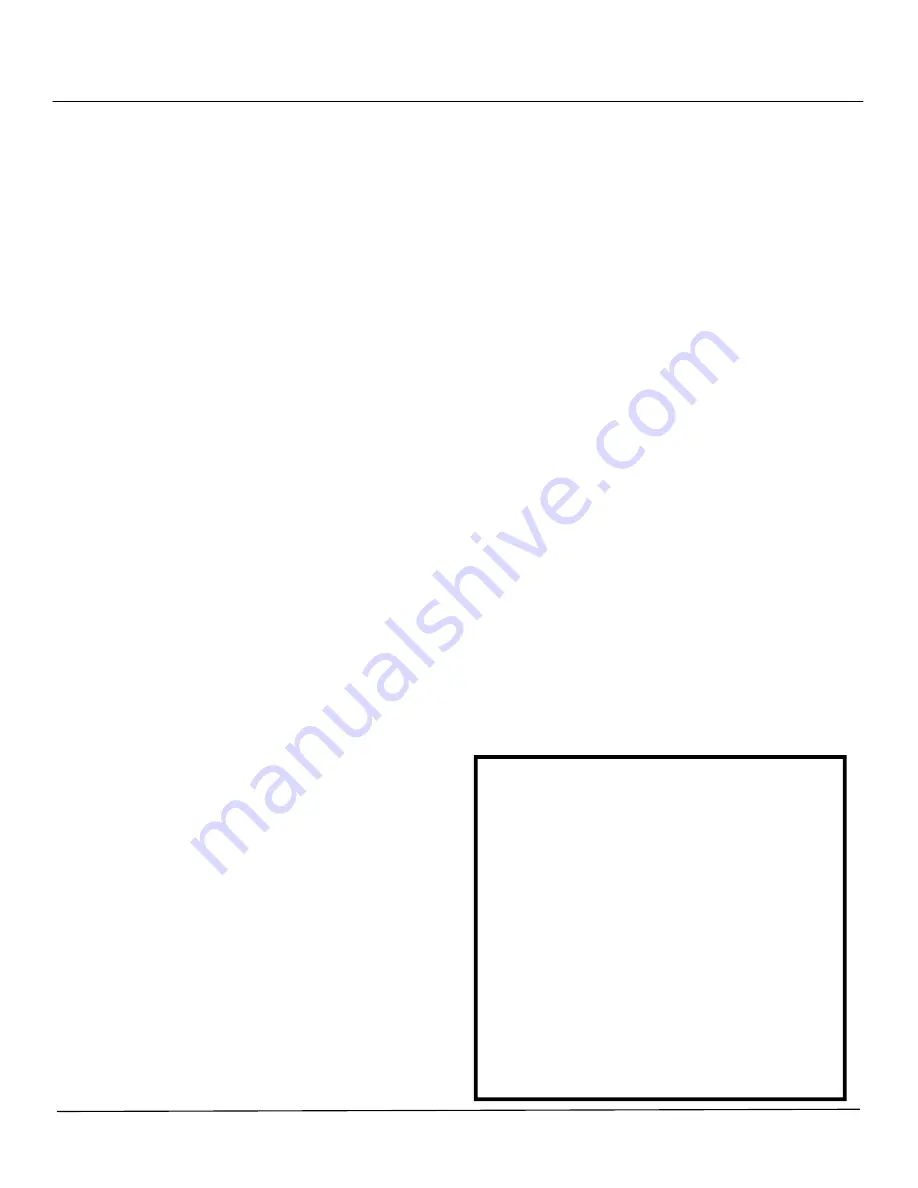
Maintenance
Manual
6
Ampco
Pumps
Company
Operating personnel should know that any changes in the system or the liquid being pumped might have an effect on the pump’s
performance. It is advisable to also record the fluid temperature, specific gravity, viscosity, liquid concentration, percent of solid con-
centration, other additives and properties. A proper maintenance procedure should begin with a file for each pump. All known data
relative to the pump, fluid handled and system should be included. Complete records of maintenance and repair costs along with a
log of the units operating hours should be kept.
In addition, complete pump identification- size, type, operating speed, manufacturer, serial number, model number, and material of
construction should be noted.
Maintenance Procedures
Daily Check – possibly the most important inspection will be the daily observation.
1. Seal leakage rate
2. Pressure reading and flow indication
3. Change in operating sound
4. Change in bearing temperature
5. Check to make sure flow is going through the double seal flush lines (for Double Seal pumps)
Semi-Annual Inspection – typically made at 6-month intervals with results noted in the pumps maintenance file.
1. Check of mechanical seal assembly
2. Check of bearing lubrication
Annual Inspection – includes Semi-Annual inspection plus:
1. Removal of seal for inspection
2. Bearing
check
3. Check of axis/running clearance of impeller
Contingency Plan
For inspection findings and breakdowns, a contingency plan should be developed. To begin, an adequate supply of probable replace-
ment parts should be kept on hand.
The minimum recommended spare parts are as follows:
1. Mechanical seal kit (complete with O-ring set)
2. Casing
O-ring
3. Impeller
key
In addition Ampco recommends
1. Impeller
2. Impeller nut / bolt and washer (SP 240 only)
Where service cannot be interrupted, a complete stand-by pump
unit fully assembled (and in a by-pass line) is recommended.
Ampco
Pumps
Company
SP
Series
Manual
M
‐
015
RevC
6.19
REQUIRED
TOOLS
1.
Rubber
mallet
2.
15/16”
socket—for
impeller
nut
3.
3/8”
diameter
steel
rod—to
hold
stub
sha
4.
One–
3/4”
wrench
(frame
sizes
280
&
larger)
‐
adapter
bolts
5.
Food
grade
lubricant
(for
gaskets
and
O
‐
rings)
6.
Allen
wrench
for
sha
collar
bolts
:
3/16”
180
frame,
1/4”
210
‐
250
frame,
5/16”
280
‐
320
frame,
3/8”
360
frame
7.
Impeller
puller
/
pinch
bars
(may
be
necessary)
8.
Shim
(see
impeller
gap
chart
for
sizes)
9.
Food
grade
an
‐
seize
lubricant
DISMANTLE AND REPLACE PARTS AS FOLLOWS:
Before attempting any service on the pump or motor, discon-
nect or lock out electrical power to the pump motor. If the pump
and motor are to be removed as a unit, note the wiring configu-
ration. Use colored or numbered tape to mark the wire connec-
tions of the motor and power source, for reconnection.
These instructions are limited to fluid ends only; see other
drawings and literature applicable to motors, pedestals, frames,
shafts, etc. if additional repairs are required.