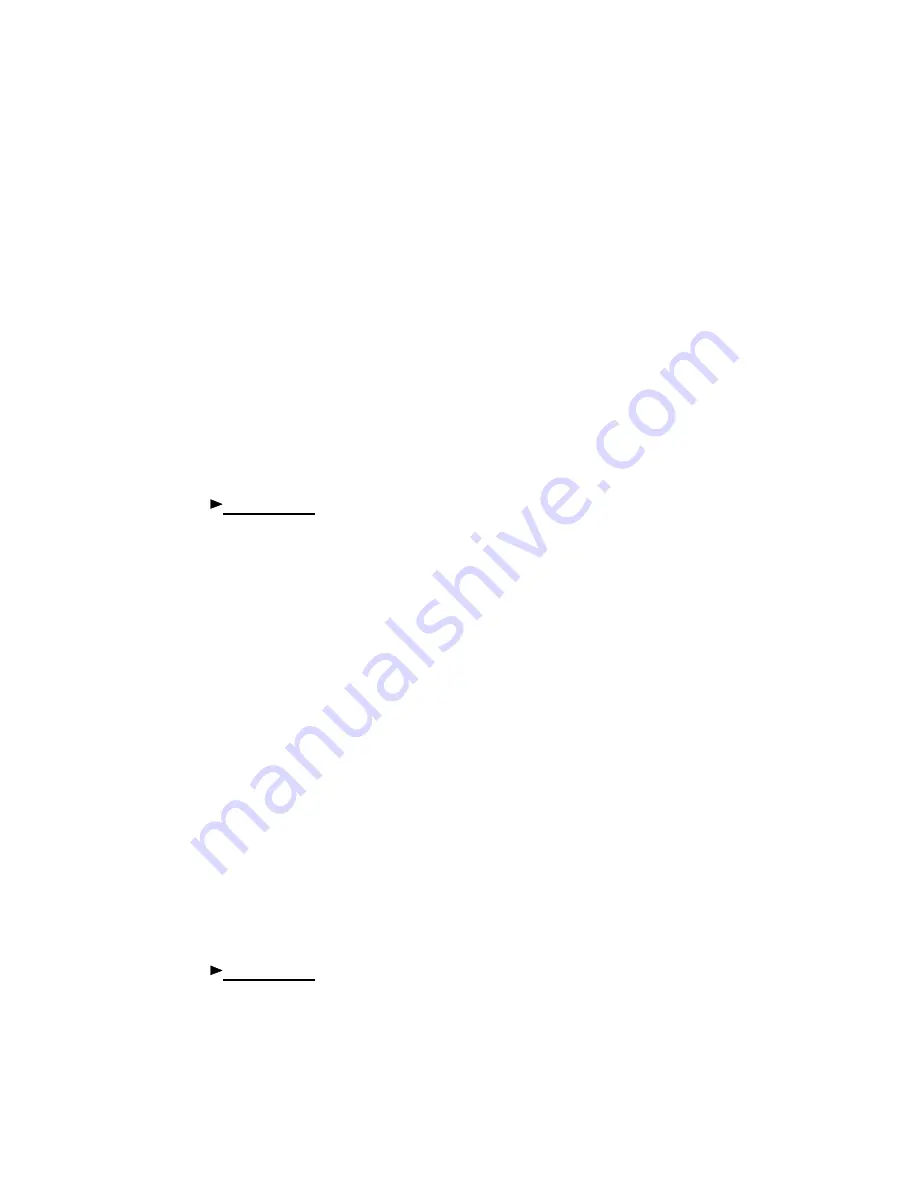
A magnet quench protection circuit is incorporated to rapidly reduce the power
supply output voltage to zero in the event a magnet quench is detected. The
function is defeatable from the front panel.
II. SPECIFICATIONS
Input power . . . . . . . . . . . . . . . . . . . . . . . . . . . . . 115 or 230 Vac, 50-60 Hz
Ramp output . . . . . . . . . . . . . . . . . . . . . . . . . . . . . 0 to 5 VDC
Charging rate . . . . . . . . . . . . . . . . . . . . . . . . . . . . 0 to 10 Amps/sec
Charging rate ranges . . . . . . . . . . . . . . . . . . . . . 0.1, 1 and 10 Amps/sec
Charging rate adjustment . . . . . . . . . . . . . . . . 10 turn potentiometer
Current limit . . . . . . . . . . . . . . . . . . . . . . . . . . . . . 10 turn potentiometer
Current control . . . . . . . . . . . . . . . . . . . . . . . . . . . Up/Pause/Down switch
Voltage limit . . . . . . . . . . . . . . . . . . . . . . . . . . . . . 10 turn potentiometer
III. INSTALLATION
WARNING:
Before energizing the instrument, the earth
ground of the power receptacle must be verified to be at earth
potential and able to carry the rated current of the power circuit.
Using extension cords should be avoided. If one must be used,
however, ensure the ground conductor is intact and capable of
carrying the rated current.
In the event that the ground path of the instrument becomes less
than sufficient to carry the rated current of the power circuit, the
instrument should be disconnected from power, labeled as unsafe,
and removed from place of operation.
This document contains operating instructions as well as
calibration instructions. The calibration procedure is to be
performed only by trained service personnel familiar with electrical
safety precautions and proper energized electrical safety
procedures. Do not perform any operations on any AMI equipment
with the cover removed unless qualified to do so and another
person qualified in first aid and CPR is present.
Do not operate this instrument in the presence of flammable
gases. Doing so could result in a life-threatening explosion.
WARNING:
Do not modify this instrument in any way. If
component replacement is required, return the instrument to AMI
facilities as described in section IX of the manual.
Page 2