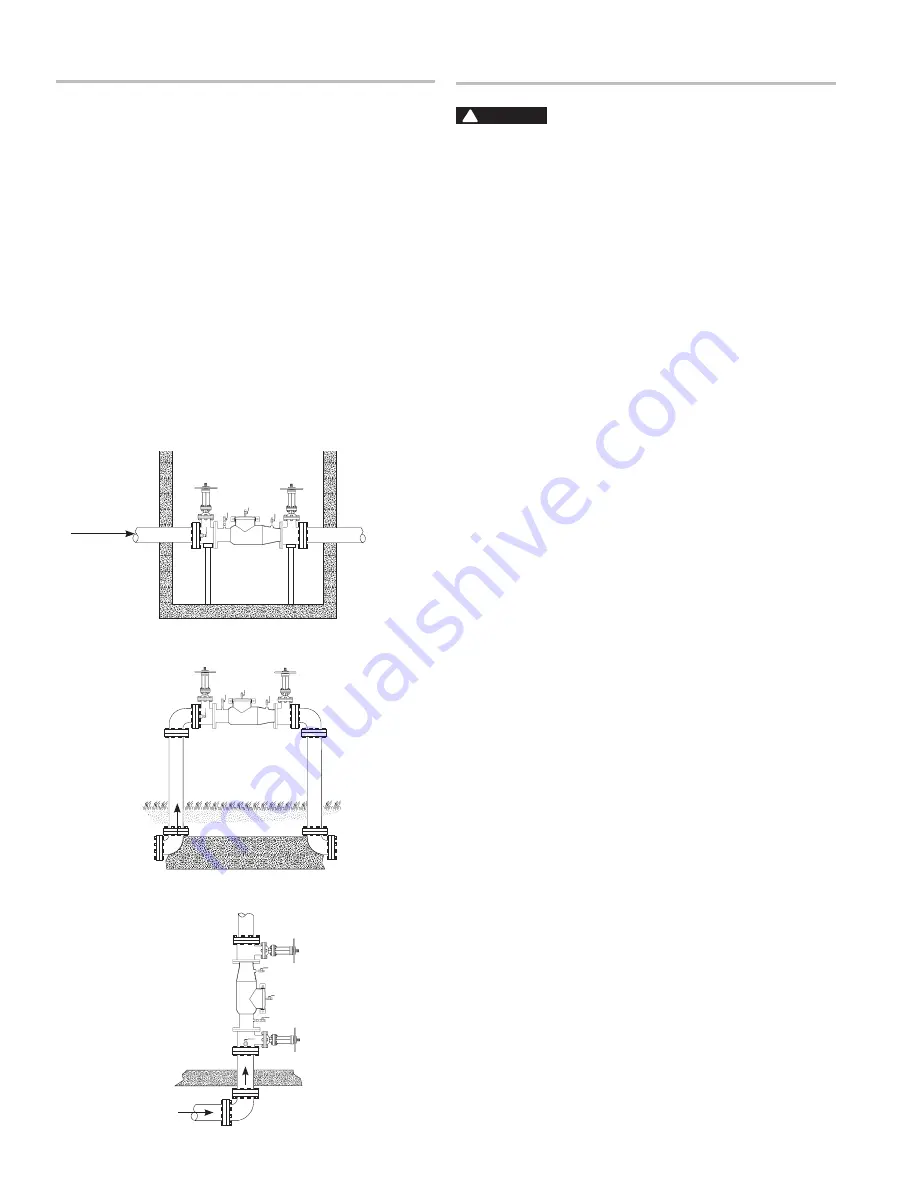
2
Outdoor Installation
1. Before installing any Ames assembly, Flush the Line thoroughly
to remove all debris, chips and other foreign objects. Failure to
do so may make the assembly inoperable.
2. The Ames 2000SS and 3000SS Backflow Preventers are ap-
proved by ASSE (American Society of Sanitation Engineers) to
be installed in horizontal or vertical positions as long as the flow
indicator arrow in the assembly is pointed in the direction of
water flow. Local water authorities must approve all installation
configurations.
3. Allow sufficient clearance around the installed assembly to
conduct testing, servicing, and inspection. Allow a minimum of 12”
from the flood level to the bottom of the assembly.
4. If double check or double check detector assembly is installed in a
vault or pit, be sure proper drainage is available. If sufficient drain-
age is not available a cross-connection may occur.
5. If installing on fire protection system, be sure to purge air from
fire system. Fill system slowly with all inspectors test valves
open.
Installation Guidelines
Indoor Installation
Vertical Installation ASSE
WARNING
!
Depressurize valve before servicing.
Removing Cam-Checks
1. Shut down water system and lock out system if possible. Slowly
open all ball valves to relieve air and water pressure. Loosen
bolts on groove coupler and remove groove coupler and cover
plate from valve body.
2.
#1 CHECK (Fig. 2)
Using a
9
/
16
” socket wrench or nut driver, remove the four nuts
from the #1 check studs (See Fig.1). Using two hands, placing
them at 12 o’clock and 6 o’clock, wiggle the check assembly
free. Remove through access port with back of clapper first with
spring end down. Pull check assembly out of main body.
#2 CHECK (Fig. 3)
After loosening bolts with a
9
/
16
” socket, remove bolts complete-
ly. Using the centerline access bar, spin the cam assembly from
the 9 o’clock position to the 12 o’clock position, then (without
letting go of the access bar) push the cam assembly slightly
downstream so that the clapper is now parallel to the valve
body. Now bring the cam assembly through the check retaining
wall. Leave the cam assembly clapper parallel to the valve body.
Pull the cam assembly through the access port.
3. Using a
3
/
8
” nut driver or a piece of small diameter pipe, place
on the cam arm torsion spring and move away from and
around the torsion spring retaining bracket so as to relieve the
torsion spring tension. (See Figure 4.) This will allow the cam
arm to move freely, enabling you to inspect the clapper face
and cam seat. Thoroughly clean the seat area and clapper
sealing surfaces, cam arms, and O-rings for damage, nicks,
and debris. If damaged, install a new check assembly O-ring,
or washer, shutoff disk.
4. Reassembly reverse of disassembly, carefully tightening torsion
spring, installing Checks and tightening Studs.
5. Before reinstallation of check assembly, thoroughly clean O-ring
groove and lubricate O-ring with F.D.A. approved lubricant.
Maintenance Instructions