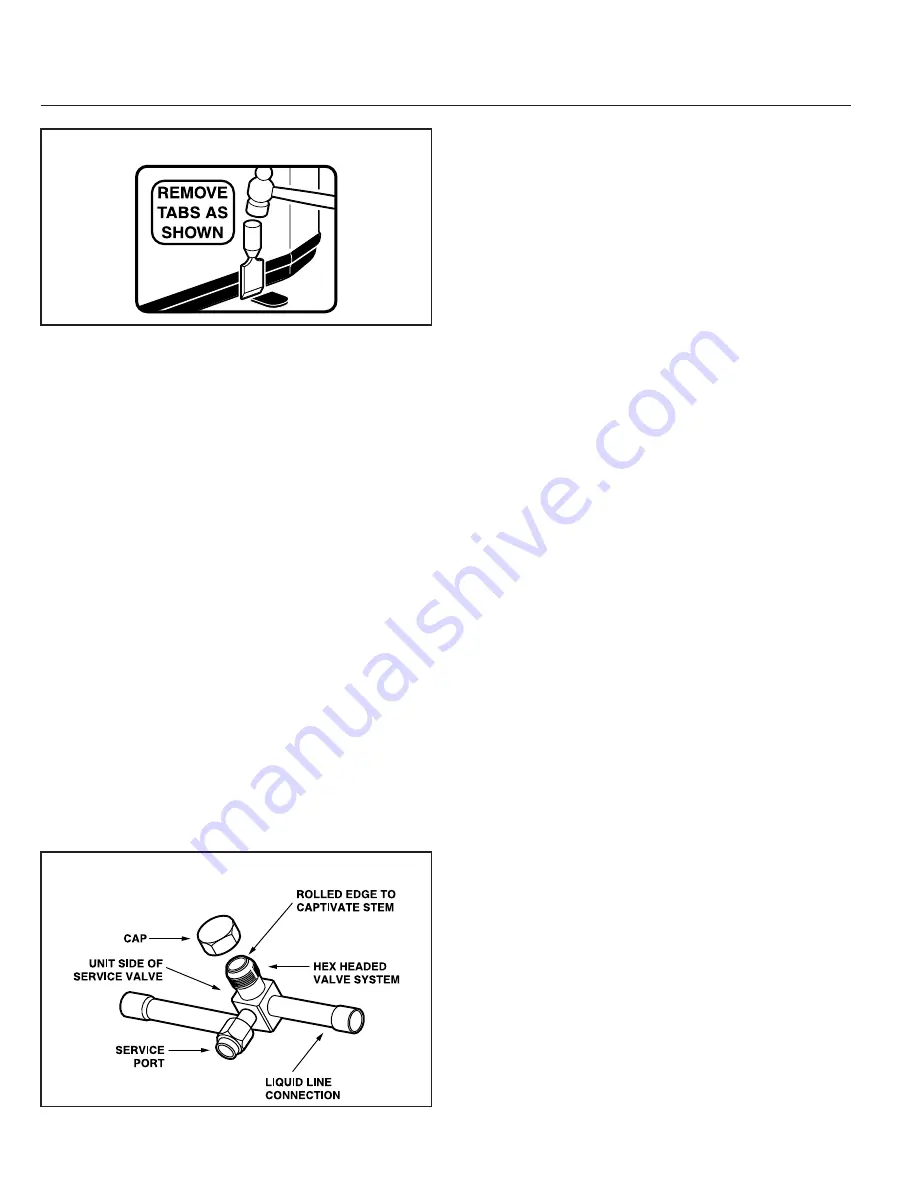
PAGE 2
Pub. No. 11-AC17D1-1
INSTALLER'S GUIDE
7. If outdoor unit is mounted above the air handler, maximum
lift should not exceed sixty (60) feet (suction line). If air handler
is mounted above condensing unit, maximum lift should not
exceed sixty (60) feet (liquid line).
8. Locate and install indoor coil or air handler in accordance
with instruction included with that unit.
NOTE: Refer to "Refrigerant Piping Software" Pub.
No. 32-3312-0*, and "Refrigerant Piping Manual"
Pub. No. 32-3009-0* (the position of the * denotes latest
revision number).
C. INSTALLING REFRIGERANT LINES
▲
CAUTION:
If using existing refrigerant lines
make certain that all joints are brazed, not soldered.
Condensing units have provisions for braze connections.
Pressure taps are provided on the service valves of outdoor unit
for compressor suction and liquid pressures.
The indoor end of the recommended refrigerant line sets may be
straight or with a 90 degree bend, depending upon situation
requirements. This should be thoroughly checked out before
ordering refrigerant line sets.
The gas line must always be insulated.
▲
CAUTION:
In scroll compressor applica-
tions, dome temperatures may be hot. Do not touch top of
compressor, may cause minor to severe burning.
The units are factory charged with the system charge required
when using fifteen (15) feet of rated connecting line. Unit
nameplate charge is the same.
Final refrigerant charge adjustment is necessary. Use
the Charging Information on page 6 or in the outdoor unit
Service Facts.
1. Determine the most practical way to run the lines.
2. Consider types of bends to be made and space limitations.
NOTE: Large diameter tubing will be very difficult to rebend
once it has been shaped.
3. Determine the best starting point for routing the refrigerant
tubing — INSIDE OR OUTSIDE THE STRUCTURE.
4. Provide a pull-thru hole of sufficient size to allow both liquid
and gas lines.
5. Be sure the tubing is of sufficient length.
6. Uncoil the tubing — do not kink or dent.
7. Route the tubing making all required bends and properly
secure the tubing before making connections.
8. To prevent a noise within the building structure due to
vibration transmission from the refrigerant lines, the following
precautions should be taken:
a. When the refrigerant lines have to be fastened to floor
joists or other framing in a structure, use isolation type hangers.
b. Isolation hangers should also be used when refrigerant
lines are run in stud spaces or enclosed ceilings.
c. Where the refrigerant lines run through a wall or sill,
they should be insulated and isolated.
d. Isolate the lines from all ductwork.
D. SERVICE VALVE OPERATION
BRASS LIQUID AND GAS LINE SERVICE VALVES
The Brass Liquid and Gas Line Service Valves are factory
shipped in the seated position to hold factory charge. The
pressure tap service port (when depressed) opens only to the
field brazing side of the valve when the valve is in the seated
position. The liquid line valve is not a back seating valve (see
WARNING below).
▲
WARNING:
Extreme caution should be ex-
ercised when opening the Liquid and Gas Line Service
Valves. Turn valve stem counterclockwise only until the
stem contacts the rolled edge. (See Figures 3 and 5) No
torque is required.
BRASS GAS LINE BALL SERVICE VALVE
The Brass Gas Line Ball Service Valve is shipped in the closed
position to hold the factory refrigerant charge. The pressure tap
service port (when depressed) opens only to the field brazing
side when the valve is in the closed position.
The Gas Line Service Valve is full open with a 1/4 turn. See
Figure 4.
BRAZING REFRIGERANT LINES
1. Remove lower access cover to access service valves.
2. Before brazing, remove plugs from external copper stub
tubes. Clean internal and external surfaces of stub tubes prior
to brazing.
BASEPAN TAB REMOVAL
2
3
LIQUID LINE SERVICE VALVE