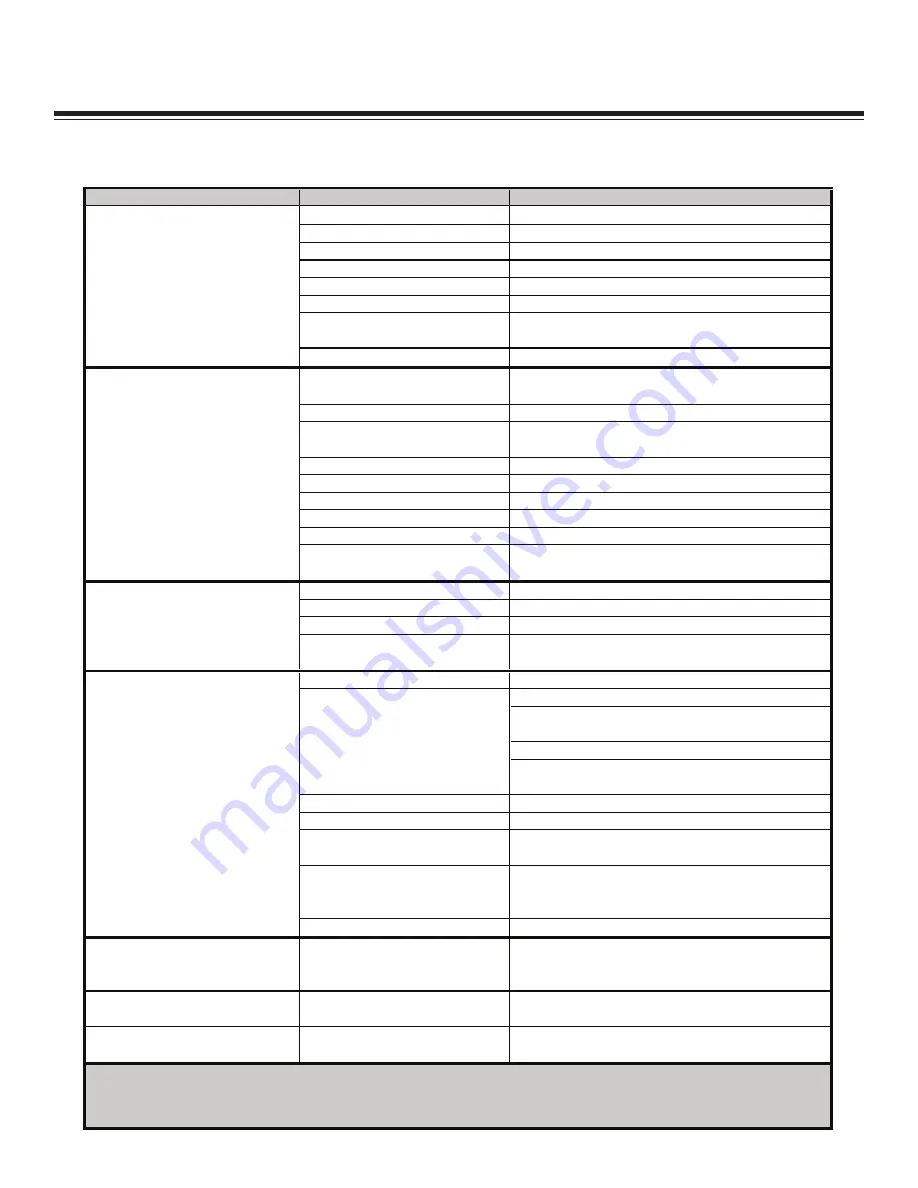
29
Troubleshooting
29
Chapter 8 - Troubleshooting
If symptoms of poor performance develop, the following chart can be used as a guide to investigate and correct the
problem. When diagnosing faults in operations of the air compressor, always check that the hydraulic power source is
supplying the correct hydraulic flow and pressure that is listed in the compressor specification section of this manual.
Problem
Possible Cause
Solution
Compressor temperature.
Low
oil level.
Add compressor oil to level.
Fan not operating.
Check ground wire and fan switch/relay.
Plugged oil filter.
Replace filter.
Dirty cooler core.
Clean cooler fins.
Contaminated cooler core.
Remove and clean.
Hydraulic pressure and flow
incorrect
Adjust and reset according to specifications.
Worn hydraulic motor.
Replace.
Air demand too great.
Tighten air hose clamps. Repair air leaks.
Air filter plugged.
Clean or replace.
Pressure switch out of
adjustment.
Readjust to specifications.
Faulty pressure switch.
Replace.
Compressor speed too slow.
Check hydraulic flow and pressure.
Drive belt slipping.
Readjust and tighten.
Service valve wide open.
Close valve.
Solenoid valve on.
Hydraulic Manifold valve stuck
(closed).
Clean or replace.
Defective pressure switch.
Replace.
Air control line leaking.
Check and correct.
Inlet valve stuck.
Clean and replace.
Restriction in control line
(dirt/ice).
Clean and free up.
Belt Slipping
Readjust and tighten.
Check the following:
1. Setting on supply pressure sytem relief valve.
2. Ensure adequate pressure and flow.
3. Check and see if other hydraulic systems
activated off the same hydraulic supply.
Presssure relief set too low.
Readjust.
Pressure relief seals leaking.
Replace.
Air pressure set too high for
hydraulic system.
Adjust pressure switch to reduce air pressure.
Solenoid valve cartridge seals
leaking on hydraulic manifold
assembly.
Replace with new cartridge.
Hydraulic reservoir low on oil.
Add to oil level.
Compressor noisy or loud when
starting compressor in cold
weather:
Ice buildup inside compressor
from condensation
Engage PTO and allow hydraulic fluid to
circulate and warm system up before engaging
compressor.
Compressor synthetic oil has a
milky appearance:
Coalescering/Separator
cartridge clogged or plugged.
Replace cartridge and change compressor oil.
Ecessive oil level in compressor: Internal crack inside oil cooler.
Replace cooler, change filters and compressor
oil.
Insufficient hydraulic system
pressure or flow.*
*This can occur if another hydraulically activated component is used off the same pump system. Activating the secondary
component may drop hydraulic supply system pressure/flow and leave insufficient for compressor. Not: Even a momentary drop
in hydraulic supply pressure or flow may initiate compressor blowdown to commence.
Compressor Shuts Down with air
demand:
Compressor will not build up
pressure:
Compressor over pressures:
Compressor Stalls:
Содержание 53887
Страница 2: ...SRS 65 Manual Revisions...
Страница 8: ...4 SRS 65 Owner s Manual...
Страница 18: ...14 SRS 65 Owner s Manual Electrical Installation BLACK WIRE RED WIRE NOT USED RED WIRE NOT USED...
Страница 24: ...20 SRS 65 Owner s Manual...
Страница 30: ...26 SRS 65 Owner s Manual...
Страница 32: ...28 SRS 65 Owner s Manual...