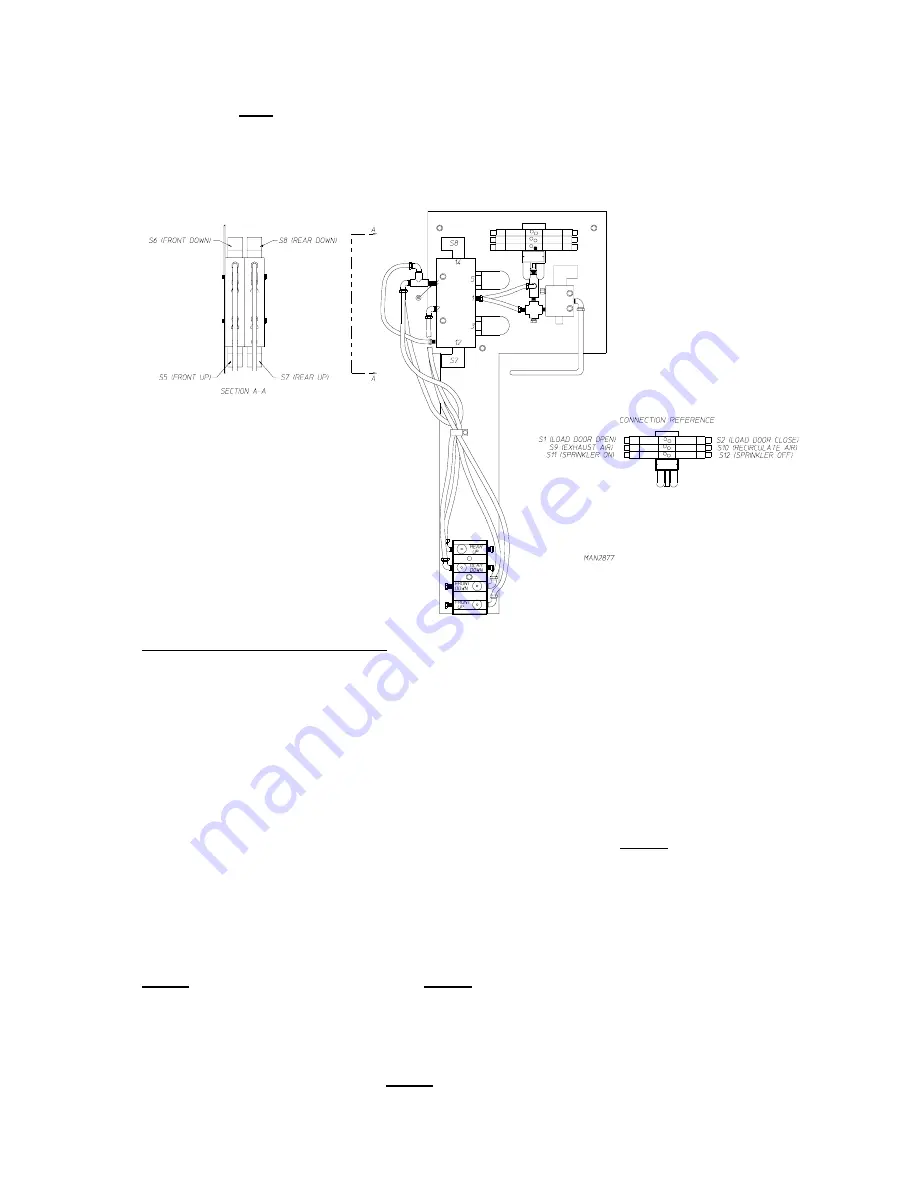
37
The tilting piston valves are 3-position valves. This means that, if no voltage is applied to both positions
S5 and S8
ALL
five (5) valve ports are blocked. If the dryer is tilting or leveling and power to the dryer
is shut off, the pistons will lock in position, holding the dryer in a partially tilted position.
The dryer can be made to tilt faster or slower by adjusting the pistons 3/8 flow control valves which are
located on the pneumatic control panel.
4. Internal and External Pilot Air Supply
On two-way tilt dryers, a pneumatic safety circuit is incorporated to prevent both front and rear tilting
pistons from extending their rods at the same time. When 120 volts is supplied to the S5 side of the front
tilting piston solenoid valve coil, the round internal spool in the core of the solenoid will move, allowing 80 PSI
(552 kPa) air to flow into the bottom ports of the front tilting pistons, while the top ports of these pistons are
bled to the atmosphere. In addition to this 120 volt electrical signal, the spool also requires a 30 PSI (207
kPa) supply of compressed air to change its position. This pilot air can either be supplied internally, tapped
off the 80 PSI (552 kPa) air supply connected to port no. 1 through holes in the body of the solenoid valve
or it can be supplied externally through the 1/8-inch F.P.T. connection located on either end of the solenoid
valve. If no pilot air is supplied to the solenoid valve. Then the spool
cannot
move, even with voltage
supplied to the solenoid valve coil.
This can be used to prevent both sets of tilting pistons from extending their rods at the same time. When the
front tilting piston rods are extended, 80 PSI (552 kPa) air is connected to the bottom piston ports, while the
top piston ports are bled to the atmosphere. So, by tapping the external pilot air supply to the rear tilting rods
are extended, then there is no pilot pressure available to the rear tilting piston solenoid valve so that its spool
cannot
move and the rear tilting piston rods
cannot
extend if a 120 volt signal is sent to its 12 side solenoid
valve coil.
The external pilot air supply to the front tilting piston is tapped off the rear tilting piston top port air line so that
whenever the rear piston rods are extended, there is no pilot air supplied to the front tilting piston solenoid
valve and the front tilting piston rods
cannot
extend. On the solenoid valve supplied on the dryer, the 12
side valve is externally piloted, while 14 side valve is internally piloted.
Содержание ADS-464 II
Страница 80: ...ADC113074 1 01 24 00 10 ...