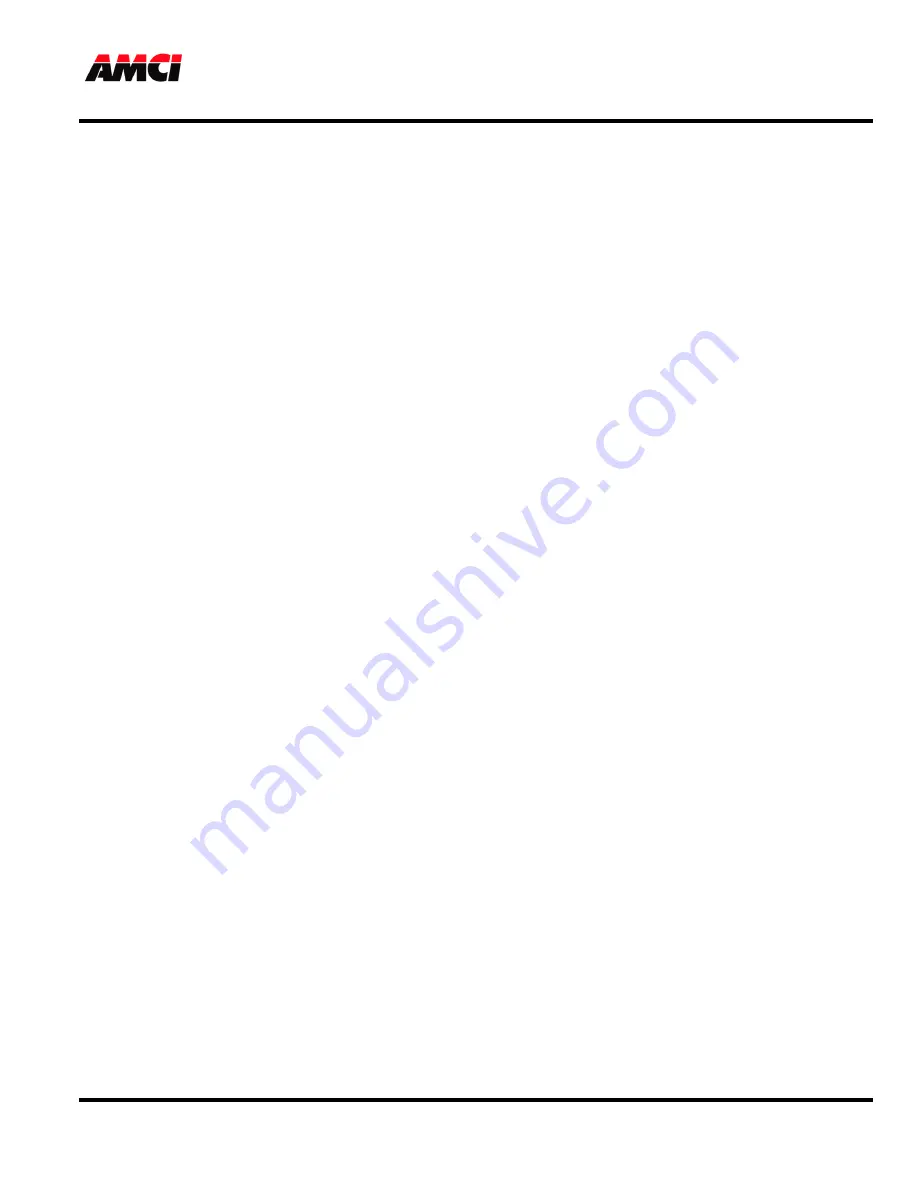
20 Gear Drive, Plymouth Industrial Park, Terryville, CT 06786 page: 13
Tel: (860) 585-1254 Fax: (860) 584-1973 Web: www.amci.com
ControlLogix 7252 LDT Interface Manual
Revision 1.5
Latched Input: The 7252 module has two Latch Inputs, one for each channel, that allow you to capture and display
the current Data Value whenever the input transitions. This parameter, which is composed of two bits, allows you to
capture the input on the 0 to 1 transition, the 1 to 0 transition, or on both transitions. The function of the Latched Input
will be disabled if neither bit is set.
To be read by the 7252 module, the latching inputs must be on for between 0.2ms and 1.2ms, depending on the
number of channels being used.
The 7252 module reports the status of the Latched input even if the function of the latched input has been
disabled.
The Latched Value is not saved through power down. Therefore, the Latched Value displayed in the 7252
module’s input registers at power up will be zero.
Limit Switch Position: These two-word parameters define ON and OFF setpoints. If the ON setpoint is less than the
OFF setpoint, a bit in the Input Registers, which can be easily interrogated by a relay instruction, will be set when the
Data Value is between these two setpoints, but not equal. If the ON setpoint is greater than then OFF setpoint, then the
bit will be set when the Data Value is outside of the these two setpoints, but not equal.
A separate Limit Switch bit based on the same ON/OFF setpoints also exists for the Interpolation Data Value.
Interpolated Data value: This additional and optional feature may be useful for customers using the ControlLogix
PLC’s virtual axis functionality. If used, the 7252 module will take the PLC’s Central System Clock-Time and the
sensor’s velocity data to calculate an Interpolated or “Look Ahead” Data value. This has two possible functions. One,
the Interpolated Data Value along with the time value can be sent to other ControlLogix modules, for example the
AMCI 8213-VA, allowing them to schedule their responses with a high degree of precision. Two, the Interpolated Data
Value allows the user to “Look Ahead” to what the Data Value will be at a defined time in the future. Here is the
procedure for generating the Interpolation Data Value.
1.
Make the PLC the System Time Master by opening the Controller Properties and clicking
on the Date/Time tab. Click on the box next to the “Make this controller the Coordinated
System Time Master” text so that a check mark appears in the box and accept the changes
by clicking on OK. The Interpolated position value will be valid only if this step is
performed.
2.
Create a GSV instruction in your ladder logic, with the Class Name set to CST and the
Attribute Name set to CurrentValue, to read the system time from the PLC. The
destination address must made up of two DINT registers.
3.
If desired, add a value to word 0 of the time value read above. This value is entered in
1
µ
s increments, every 1000 equals 1ms, and equals the amount of time that you want to
“look ahead.”
4.
Place the time value from step 3 into the output registers. The next time that the
Interpolation Transmit bit transitions from either 0 to 1 or 1 to 0, the Central System Time
will be sent to the 7252 module.
5.
The latest Interpolation Data Value will be located in the input data the next time the
module is updated at the normal RPI update.