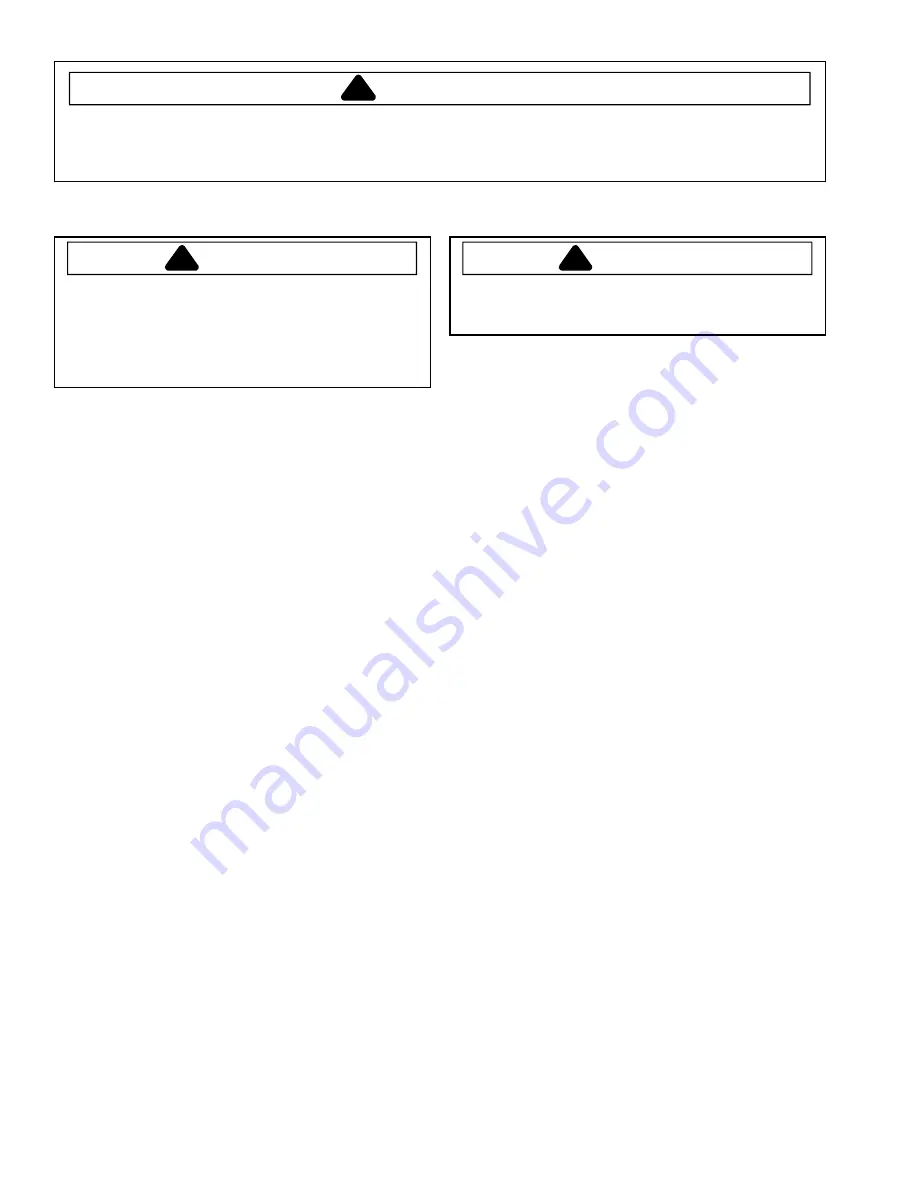
RS4100004 Rev. 0
26
Leak Testing
DANGER
!
To prevent serious injury or death from violent
explosions, NEVER use oxygen or acetylene for
pressure testing or cleanout of refrigeration systems.
Free oxygen will explode on contact with oil.
Acetylene will explode spontaneously when put
under pressure.
It is important to check sealed system for refrigerant
leaks. Undetected leaks can lead to repeated service
calls and eventually result in system contamination,
restrictions, and premature compressor failure.
Refrigerant leaks are best detected with halide or
electronic leak detectors.
NOTE: The flame on a halide detector glows green in
the presence of HCFC22 refrigerant.
Testing Systems Containing a Refrigerant Charge
1. Stop the operation (turn air conditioner off).
2. Holding leak detector exploring tube as close to
system tubing as possible, check all piping, joints,
and fittings.
NOTE: Use soap suds on areas leak detector cannot
reach or reliably test.
Testing Systems Containing No Refrigerant Charge
1. Connect cylinder of nitrogen, through gauge manifold,
to process tube of compressor and liquid line strainer.
2. Open valves on nitrogen cylinder and gage manifold.
Allow pressure to build within sealed system.
3. Check for leaks using soap suds.
If a leak is detected in a joint, do not to attempt to repair
by applying additional brazing material. Joint must be
disassembled, cleaned and rebrazed. Capture refrigerant
charge (if system is charged), unbraze joint, clean all
parts, then rebraze.
If leak is detected in tubing, replace tubing. If leak is
detected in either coil, replace faulty coil.
Brazing
CAUTION
!
To reduce risk of personal injury or property
damage, take necessary precautions against high
temperatures required for brazing.
Satisfactory results require cleanliness, experience, and
use of proper materials and equipment.
Connections to be brazed must be properly sized, free of
rough edges, and clean.
Generally accepted brazing materials are:
·
Copper to copper joints: SIL-FOS (alloy of 15
percent silver, 80 percent copper, and 5 percent
phosphorous). Use without flux. Recommended
brazing temperature is approximately 1400°F. DO NOT
USE FOR COPPER TO STEEL CONNECTION.
·
Copper to steel joints: SILVER SOLDER (alloy of 30
percent silver, 38 percent copper, 32 percent zinc).
Use with fluoride based flux. Recommended brazing
temperature is approximately 1200°F.
·
Steel to steel joints: SILVER SOLDER (see copper
to steel joints).
·
Brass to copper joints: SILVER SOLDER (see
copper to steel joints).
·
Brass to steel joints: SILVER SOLDER (see copper
to steel joints).
Testing Procedures
!
WARNING
To avoid risk of electrical shock, personal injury, or death, disconnect electrical power source to unit and
discharge capacitor through a 10,000 ohm resistor before attempting to service, unless test procedures require
power to be connected. Ensure all ground wires are connected before certifying unit as repaired and/or
operational.