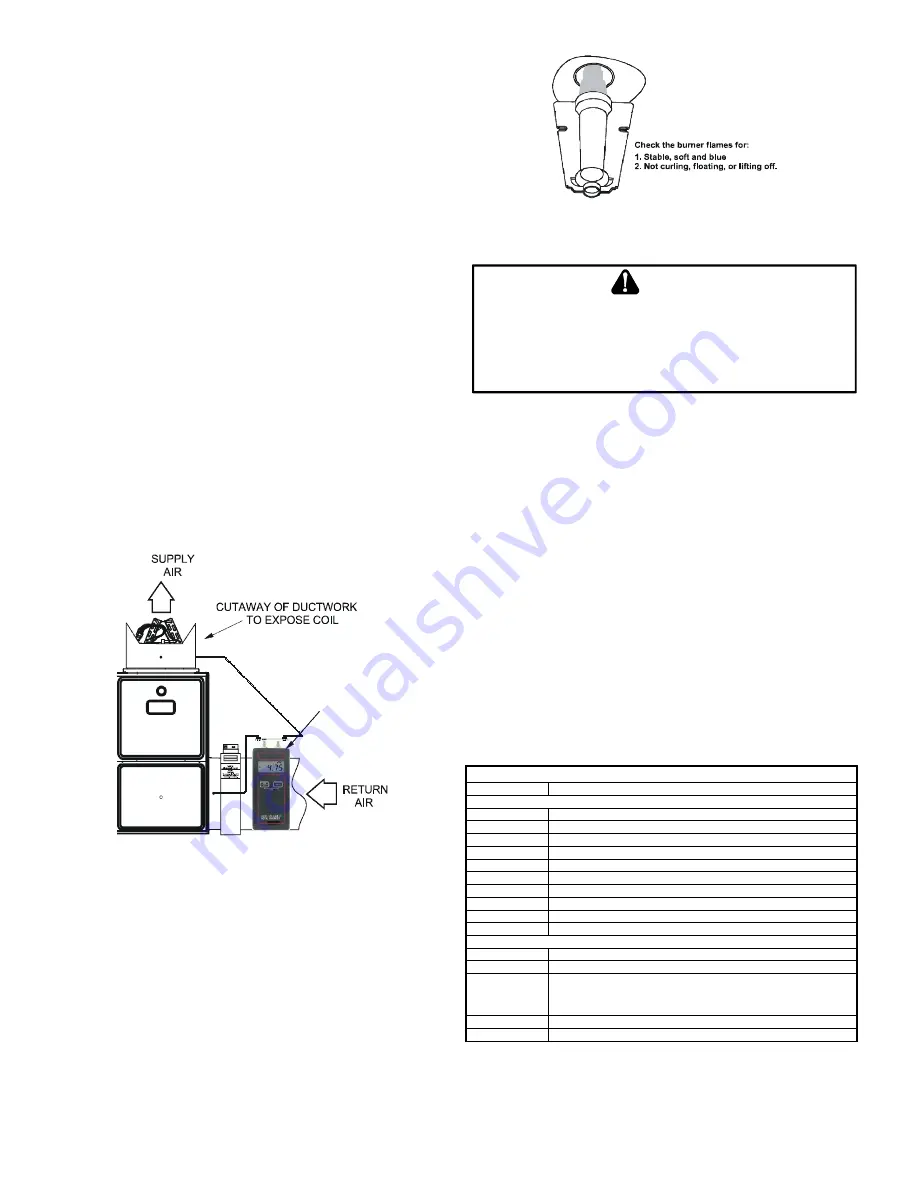
23
Burner Flame
T
O
AVOID
PERSONAL
INJURY
OR
DEATH
,
DO
NOT
REMOVE
ANY
INTERNAL
COMPARTMENT
COVERS
OR
ATTEMPT
ANY
ADJUSTMENT
.
E
LECTRICAL
COMPONENTS
ARE
CONTAINED
IN
BOTH
COMPARTMENTS
.
C
ONTACT
A
QUALIFIED
SERVICE
AGENT
AT
ONCE
IF
AN
ABNORMAL
FLAME
APPEARANCE
SHOULD
DEVELOP
.
WARNING
Safety Circuit Description
General
A number of safety circuits are employed to ensure safe and
proper furnace operation. These circuits serve to control any
potential safety hazards and serve as inputs in the monitoring
and diagnosis of abnormal function. These circuits are contin-
uously monitored during furnace operation by the integrated
control module.
Integrated Control Module
The integrated control module is an electronic device which
controls all furnace operations. Responding to the thermostat,
the module initiates and controls normal furnace operation,
and monitors and addresses all safety circuits. If a potential
safety concern is detected, the module will take the neces-
sary precautions and provide diagnostic information through
an LED
Red LED Flash
Error / Condition
1
System Lockout (Retries Exceeded)
2
Pressure Switch stuck Closed
3
Pressure Switch stuck Open
4
Open Main or Auxillary Temperature Limit Switch
5
Flame Sensed>4.25 Seconds with Gas Valve De-Energized
6
Open Rollout Temperature Limit Switch
8
Igniter Relay Fault
10
Open Fuse
11
Igniter Open
12
Inducer Relay Error
7
Low Flame Sense Signal
9
Twinning Fault
OFF
Control Failure / No Power / Internal Fault / IRQ Loss. Gas Heating Lockout
(Gas valve energized when it should be de-energized) Or Gas Valve De-
energized when it should be Energized
Rapid Flash
Reverse Polarity
Continuous On Normal Operation
ERROR CODE
Flash Codes stored in memory (auto-erased after 14 days)
Flash Codes NOT stored in memory
.
Excessive external static pressure will result in insufficient air
that can cause excessive temperature rise. This can cause
limit switch tripping and heat exchanger failure.
To determine total external duct static pressure, proceed as
follows;
1. With clean filters in the furnace, use a draft gauge
(inclined manometer) to measure the static pressure
of the return duct at the inlet of the furnace. (Negative
Pressure)
2. Measure the static pressure of the supply duct. (Positive
Pressure)
3. The difference between the two numbers is .4” w.c.
Example:
static reading from return duct = -.1” w.c.
static reading from supply duct = .3” w.c.
total external static pressure on this system = .4” w.c.
NOTE:
Both readings may be taken simultaneously and read
directly on the manometer if so desired. If an air conditioner
coil or Electronic Air Cleaner is used in conjunction with the
furnace, the readings must also include theses components,
as shown in the following drawing.
4. Consult proper tables for the quantity of air.
If the total external static pressure exceeds the maximum listed
on the furnace rating plate, check for closed dampers, regis-
ters, undersized and/or oversized poorly laid out duct work.
Digital
Manometer
Checking Static Pressure
Burner Flame
The burner flames should be inspected with the burner
compartment door installed. Flames should be stable, quiet,
soft, and blue (dust may cause orange tips but they must not
be yellow). Flames should extend directly outward from the
burners without curling, floating, or lifting off. Flames must
not impinge on the sides of the heat exchanger firing tubes.
Содержание CES80
Страница 39: ...39 THIS PAGE INTENTIONALLY LEFT BLANK...