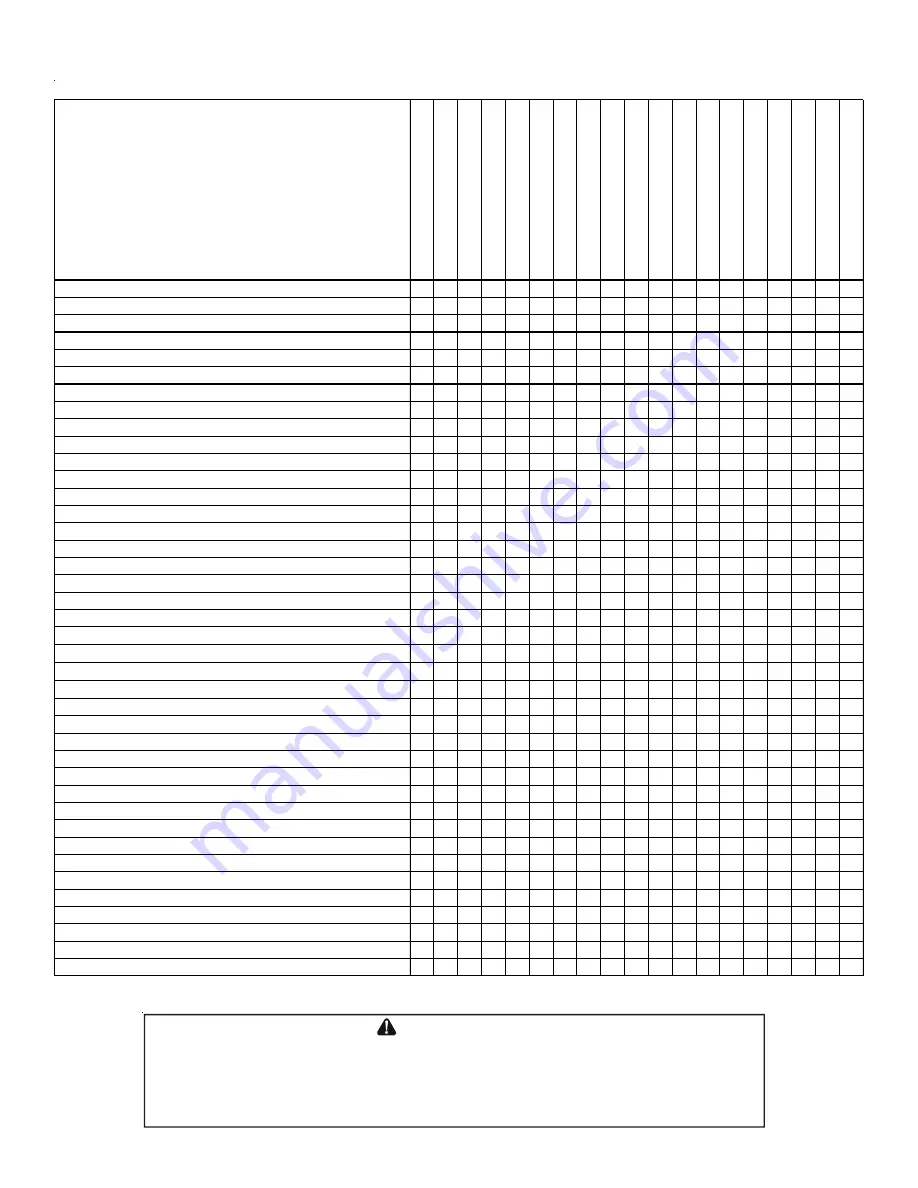
31
A
VOID
CONTACT
WITH
THE
CHARGED
AREA
.
•N
EVER
TOUCH
THE
CHARGED
AREA
BEFORE
CONFIRMING
THAT
THE
RESIDUAL
VOLTAGE
IS
50
VOLTS
OR
LESS
.
1. S
HUT
DOWN
THE
POWER
AND
LEAVE
THE
CONTROL
BOX
FOR
10
MINUTES
.
2. M
AKE
SURE
TO
TOUCH
THE
E
ARTH
GROUND
TERMINAL
TO
RELEASE
THE
STATIC
ELECTRICITY
FROM
YOUR
BODY
(
TO
PREVENT
FAILURE
OF
THE
PC
BOARD
).
3. M
EASURE
THE
RESIDUAL
VOLTAGE
IN
THE
SPECIFIED
MEASUREMENT
POSITION
USING
A
VOM
WHILE
PAYING
ATTENTION
NOT
TO
TOUCH
THE
CHARGED
AREA
.
4. I
MMEDIATELY
AFTER
MEASURING
THE
RESIDUAL
VOLTAGE
,
DISCONNECT
THE
CONNECTORS
OF
THE
OUTDOOR
UNIT
’
S
FAN
MOTOR
. (I
F
THE
FAN
BLADE
ROTATES
BY
STRONG
WIND
BLOWING
AGAINST
IT
,
THE
CAPACITOR
WILL BE CHARGED,
CAUSING
THE
DANGER
OF
ELECTRICAL
SHOCK
.)
WARNING
Outdoor Normal Temperature Operating Range: 17-62° / Indoor Normal Temperature Operating Range: 65 - 85°
POSSIBLE CAUSE
X IN ANALYSIS GUIDE INDICATE
"POSSIBLE CAUSE"
C
o
m
p
di
sc
har
g
e
te
m
p
>
200F
C
o
m
p
di
sc
har
g
e
te
m
p
<
105F
C
o
m
p
di
sc
har
g
e
S
H
>
70
F
C
o
m
p
di
sc
har
g
e
S
H
<
20
F
H
igh
pr
es
su
re
>
490ps
i
H
igh
pr
es
su
re
S
S
V
<
270
ps
i
H
igh
pr
es
su
re
LS
V
<
270
ps
i
LS
V
S
C
>
12F
L
S
V
SC
<
4
F
Low
pr
es
su
re
<
40ps
i
R
equ
es
ted %
d
e
m
and <
A
ct
ual
%
R
equ
es
ted %
d
e
m
and >
A
ct
ual
%
R
epe
at
ed s
top
/s
ta
rt
W
e
a
k heat
in
g
N
o
s
w
itc
h
heat
in
g
No
is
e
In
co
m
p
le
te
def
ro
st
oper
a
tio
n
S
top
oper
at
io
n
S
w
ea
ting l
iqui
d
li
n
e
Liquid stop valve does not fully open
X
X
X
X
X
X
X
X
X
X
Gas stop valve does not fully open
X
X
X
X
X
X
X
X
X
Line set restriction
X
X
X
X
X
X
X
X
X
X
Line set length is too long
X
X
X
Blocked filter-dryer
X
X
X
X
X
X
X
X
X
X
OD EEV coil failure
X
X
X
X
X
X
X
X
X
X
X
X
X
X
X
X
OD EEV failure
X
X
X
X
X
X
X
X
X
X
X
X
X
X
X
X
Check valve failure – Leakage
X
X
X
X
X
X
X
High Pressure switch failure
X
Pressure sensor failure
X
X
X
X
X
X
X
X
X
X
X
X
Discharge temp sensor failure
X
X
X
X
X
X
X
X
X
Coil temp sensor failure
X
X
X
X
X
X
Defrost sensor failure
X
X
X
X
X
X
Liquid temp sensor failure
X
X
X
X
Ambient temp sensor failure
X
X
X
X
X
X
X
OD recirculation
X
X
X
X
X
X
X
X
ID recirculation
X
X
X
X
X
X
Dirty OD Heat-exchanger
X
X
X
X
X
X
X
X
Dirty ID Heat-exchanger
X
X
X
X
X
X
Outdoor Ambient temp is too high
X
X
X
X
X
X
Outdoor Ambient temp is too low
X
X
X
X
X
X
X
X
X
X
ID suction temp is too high
X
X
X
X
X
ID suction temp is too low
X
X
X
Mixture of non-condensible gas
X
X
X
X
X
X
X
X
OD fan motor failure
X
X
X
X
X
X
X
RV failure
X
X
X
X
X
X
X
X
X
RV coil failure
X
X
X
X
X
X
X
X
X
Over charge
X
X
X
X
X
X
X
X
X
X
Under charge
X
X
X
X
X
X
X
X
X
X
Leak
X
X
X
X
X
X
X
X
X
X
TXV failure
X
X
X
X
X
X
X
X
TXV size is small
X
TXV size is big
ID failure
X
X
X
X
X
X
X
X
X
X
X
X
X
X
X
X
X
X
OD Control Board failure
X
Compressor failure
X
X
X
X
X
X
X
X
X
X
X
X
Cooling loop is not attached
X
X
X
Cooling loop grease is not enough
X
X
X
Compressor and Gas furnace are operating at the same time
X
X
Low ID CFM
X
X
X
X
X
X
X
HEATING ANALYSIS CHART