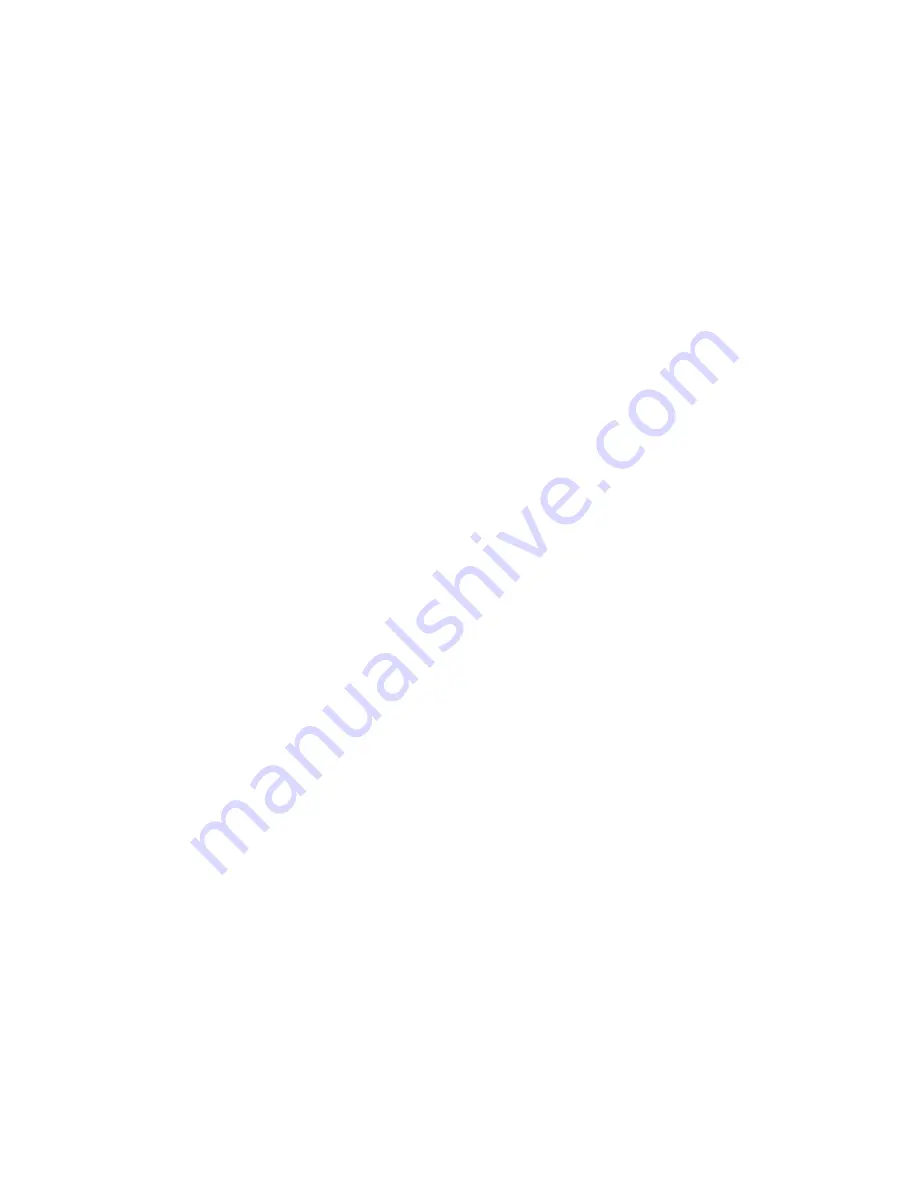
SERVICING
52
5. Compare the hi-pressure reading to the "Required Liquid Line
Temperature" chart. Find the hi-pressure value on the left col-
umn. Follow that line right to the column under the design
subcooling value. Where the two intersect is the required liq-
uid line temperature.
Alternately you can convert the liquid line pressure gauge
reading to temperature by finding the gauge reading in the R-
410A Pressure vs. Temperature Chart, find the temperature in
the °F. Column.
6. The difference between the thermometer reading and pressure
to temperature conversion is the amount of subcooling.
ADD CHARGE TO RAISE SUBCOOLING. RECOVER CHARGE
TO LOWER SUBCOOLING.
Subcooling Formula = Sat. Liquid Temp. - Liquid Line Temp.
NOTE:
To adjust subcooling, follow the sequence of S-108.
EXAMPLE:
a. Liquid Line Pressure = 417 PSIG
b. Corresponding Temp. = 120°F.
c. Thermometer on Liquid line = 109°F.
To obtain the amount of subcooling subtract 109°F from 120°F.
The difference is 11° subcooling. See the specification sheet or
technical information manual for the design subcooling range for
your unit.
There are other causes for high head pressure which may be found
in the "Cooling / Heating Analysis Chart."
If other causes check out normal, an overcharge or a system con-
taining non-condensables would be indicated.
If this system is observed:
1. Start the system.
2. Remove and capture small quantities of gas from the suction
line dill valve until the head pressure is reduced to normal.
3. Observe the system while running a cooling performance test.
If a shortage of refrigerant is indicated, then the system con-
tains non-condensables.
SUPERHEAT AND SUBCOOLING ADJUSTMENT ON TXV APPLICATIONS
NOTE:
Subcooling and superheat information is valid only while
the unit is operating at 100% capacity or 100% compressor speed
in CHARGE MODE.
Compressor speed is displayed under STATUS menu in the
thermostat.
1. Run system at least 10 minutes to allow pressure to
stabilize. During the adjustment of subcooling, ambient
temperature should be greater than 65°F and less than
105°F. If ambient temperature is out of range, don’t adjust
subcooling.
2. For best results, temporarily install a thermometer on the
liquid line at the liquid line service valve and 4-6" from the
compressor on the suction line. Ensure the thermometer
makes adequate contact and is insulated for best possible
readings. Use liquid line temperature to determine sub-
cooling and vapor temperature to determine superheat.
NOTE:
A
N
OPTIONAL
METHOD
IS
TO
LOCATE
THE
THERMOMETER
AT
THE
SUCTION
LINE
SERVICE
VALVE
. E
NSURE
THE
THERMOMETER
MAKES
ADEQUATE
CONTACT
AND
IS
INSULATED
FOR
BEST
POSSIBLE
READINGS
.
3. The system subcooling should be 7 to 9°F. If not in that range,
adjust subcooling and superheat according to the following
procedure.
a. If subcooling and superheat are low, adjust TXV to 7 to
9°F superheat, then check subcooling.
NOTE:
To adjust superheat, turn the valve stem clockwise
to increase and counter clockwise to decrease.
b. If subcooling is low and superheat is 7 to 9°F, add charge
to rise subcooling to 7 to 9°F, then check superheat.
c. If subcooling is low and superheat is high, add charge to
rise subcooling to 7 to 9°F, then check superheat.
d. If subcooling is 7 to 9°F and superheat is high, adjust the
TXV valve to 7 to 9°F superheat, then check subcooling.
e. If subcooling and superheat are high, adjust the TXV valve
to 7 to 9°F superheat, then check subcooling.
f. If subcooling is high and superheat is 7 to 9°F, remove
charge to lower the subcooling to 7 to 9°F, then check
superheat.
g. If subcooling is high and superheat is low, adjust the TXV
valve to 7 to 9°F superheat and remove charge to low the
subcooling to 7 to 9°F.
h. If subcooling is 7 to 9°F and superheat is low, adjust the
TXV valve to 7 to 9°F superheat and remove charge to
lower the subcooling 7 to 9°F, then check the superheat.
NOTE:
Not more than 0.5 lb. (8 Oz.) of refrigerant must be
added to the system in order to achieve the target
subcooling. It is recommended to add 4 oz. refrigerant
each time and try adjusting the TXV and let the system
stabilize.
4. Disconnect manifold set. Installation is complete.
S-110
CHECKING THERMOSTATIC EXPANSION VALVE
OPERATION
1. Remove the remote bulb of the thermostatic expansion valve
from the suction line.
2. Start the system and cool the bulb in a container of ice water,
closing the valve. As you cool the bulb, the suction pressure
should fall and the suction temperature will rise.
3. Next warm the bulb in your hand. As you warm the bulb, the
suction pressure should rise and the suction temperature will
fall.
4. If a temperature or pressure change is noticed, the expansion
valve is operating. If no change is noticed, the valve is re-