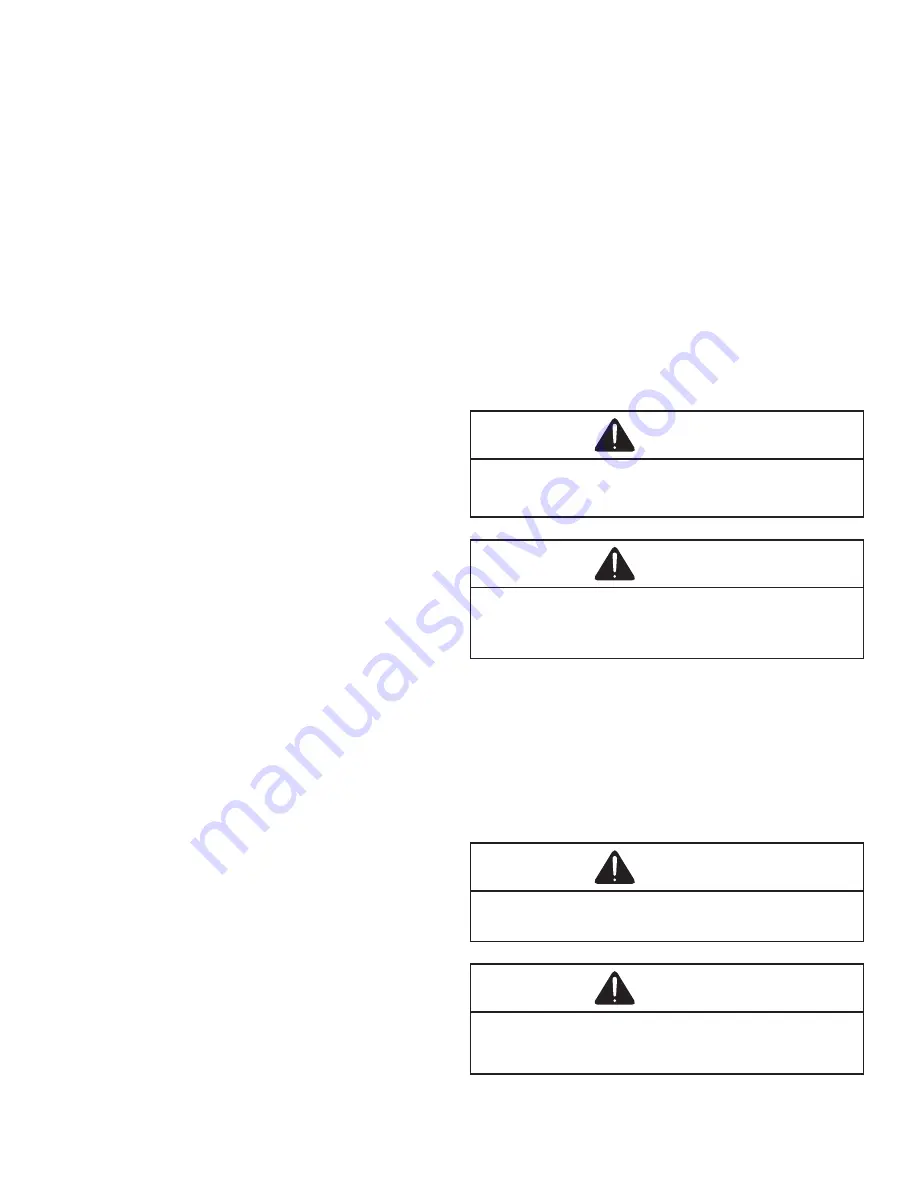
4
NOTE: If using existing indoor coil and changing
refrigerant types, ensure the indoor coil and
metering device are compatible with the type
of refrigerant being used. If new indoor coil is
required check spec sheet or AHRI for approved
coil. If system is being replaced due to compressor
electrical failure, assume acid is in system. Refer
to Service Procedure S-115 Compressor Burnout
in service manual for clean-up procedure.
Burying Refrigerant Lines
If burying refrigerant lines can not be avoided, use the
following checklist.
1. Insulate liquid and suction lines separately.
2.
Enclose all underground portions of the refrigerant
lines in waterproof material (conduit or pipe) sealing
the ends where tubing enters/exits the enclosure.
3. If the lines must pass under or through a concrete
slab, ensure lines are adequately protected and
sealed.
Refrigerant Line Connections
IMPORTANT: To avoid overheating the service
valve, TXV valve, or filter drier while brazing,
wrap the component with a wet rag, or use a
thermal heat trap compound. Be sure to follow
the manufacturer’s instruction when using the
heat trap compound. Note: Remove Schrader
valves from service valves before brazing tubes
to the valves. Use a brazing alloy of 2% minimum
silver content. Do not use flux.
Torch heat required to braze tubes of various sizes is
proportional to the size of the tube. Tubes of smaller size
require less heat to bring the tube to brazing temperature
before adding brazing alloy. Applying too much heat to any
tube can melt the tube. Service personnel must use the
appropriate heat level for the size of the tube being brazed.
NOTE:
The use of a heat shield when brazing is
recommended to avoid burning the serial plate or
the finish on the unit.
1. The ends of the refrigerant lines must be cut square,
deburred, cleaned, and be round and free from nicks
or dents. Any other condition increases the chance of
a refrigerant leak.
2. “Sweep” the refrigerant line with nitrogen or inert gas
during brazing to prevent the formation of copper-
oxide inside the refrigerant lines. The POE oils used
in R-410A applications will clean any copper-oxide
present from the inside of the refrigerant lines and
spread it throughout the system. This may cause a
blockage or failure of the metering device.
3. After brazing, quench the joints with water or a wet
cloth to prevent overheating of the service valve.
4.
Ensure the filter drier paint finish is intact after
brazing. If the paint of the steel filter drier has
been burned or chipped, repaint or treat with a rust
preventative. This is especially important on suction
line filter driers which are continually wet when the
unit is operating.
NOTE: Be careful not to kink or dent refrigerant
lines. Kinked or dented lines will cause poor
performance or compressor damage.
Do NOT make final refrigerant line connection until plugs
are removed from refrigerant tubing.
NOTE: Before brazing, verify indoor piston size by
checking the piston kit chart packaged with indoor
unit.
Standing Pressure Test (Recommended before
System Evacuation)
WARNING
To avoid the risk of fire or explosion, never use oxygen,
high pressure air or flammable gases for leak testing of a
refrigeration system.
WARNING
To avoid possible explosion, the line from the nitrogen
cylinder must include a pressure regulator and a pressure
relief valve. The pressure relief valve must be set to open at
no more than 450 psig.
Using dry nitrogen, pressurize the system to 450 PSIG.
Allow the pressure to stabilize and hold for 15 minutes
(minimum). If the pressure does not drop below 450 PSIG
the system is considered leak free. Proceed to system
evacuation using the Deep Vacuum Method. If after 15
minutes the pressure drops below 450 PSIG follow the
procedure outlined below to identify system leaks. Repeat
the Standing Pressure Test.
Leak Testing (Nitrogen or Nitrogen-Traced)
WARNING
To avoid the risk of fire or explosion, never use oxygen,
high pressure air or flammable gases for leak testing of a
refrigeration system.
WARNING
To avoid possible explosion, the line from the nitrogen
cylinder must include a pressure regulator and a pressure
relief valve. The pressure relief valve must be set to open at
no more than 450 psig.
Содержание ASXH3 Series
Страница 14: ...14 THIS PAGE IS LEFT INTENTIONALLY BLANK...
Страница 15: ...15 THIS PAGE IS LEFT INTENTIONALLY BLANK...