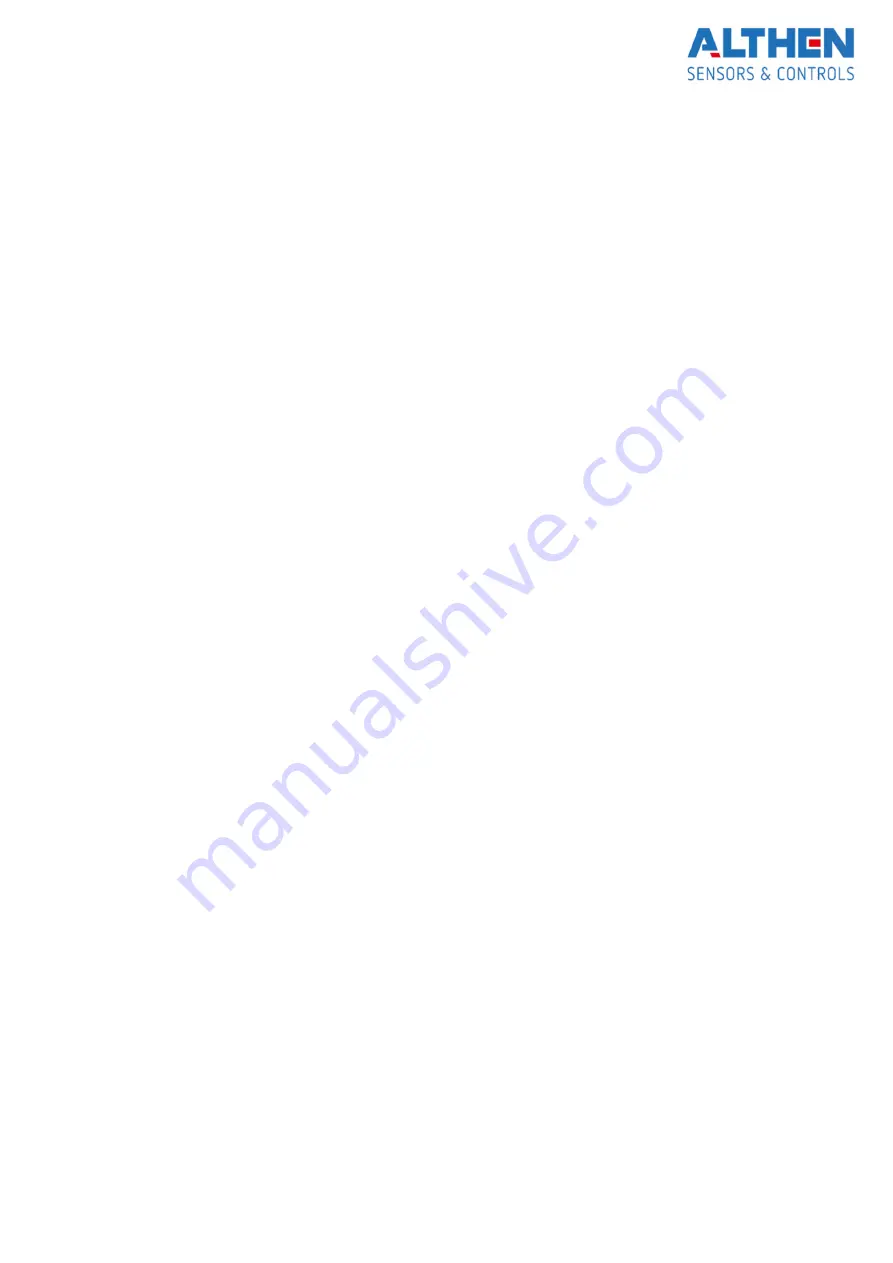
5 | 18
2.1 Instructions for using strain gauge sensors
Notice:
Strain gauge sensors with a small range are extremely sensitivity to improper handling. Force
transducers can be destroyed simply by touching. Same applies for the diaphragms of pressure and
torque sensors. So, bear in mind: handle with care!
Loading the transducer in excess of the nominal range may result in an increased and lasting zero
balance offset as well as damage to the sensor. The same applies to short-term force or pressure
impulses that exceed the nominal range.
To most force transducers the force must be applied centrically in order to avoid shear forces, which
may be harmful to the sensor, or cause measurement inaccuracy. Rounded surfaces, joint heads or
other suitable guides can ensure centric force transmission.
Tightening torqued while mounting any sensors may result in an increased zero balance offset. If the
sensor has been replaced, the calibration of the amplifier must be checked. A new adjustment might be
necessary.
3 Technical description
The described 2-channel measuring amplifier serves to supply one or two strain gauge sensors with a
full bridge resistance of 300 ohms or more and the amplification of the sensor signal. The sensors may
be connected in 4- or 6-wire technology Standard analogue outputs are available for further
evaluation. The coarse amplification is determined by an internal resistor and can be fine adjusted by a
potentiometer (V) on front of the amplifier. A second potentiometer (N) on front allows the correction
of the zero point. In addition, a dip-switch allows to change the width of the zero-adjustment range. If
even this expansion of the range should not be sufficient, an internal potentiometer can be adjusted to
add a tare.
The presence of supply / internal operation voltage is indicated by the 2 green LED’s on the front.