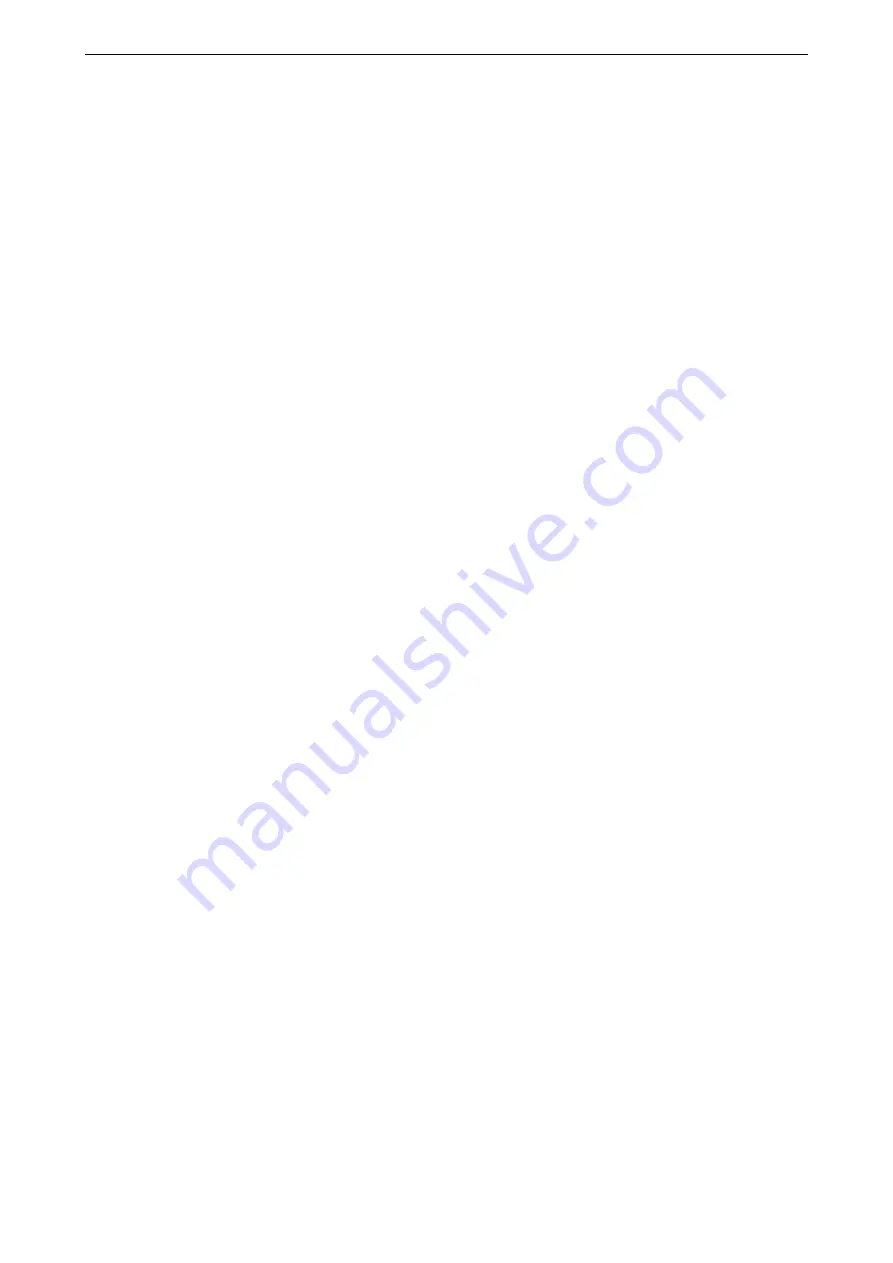
E32.0.A3.6C-01 Manual for connection and operation of the JDS-211 page 16 of 16
Tips for identification of the integral time „1.Int“
Please set the following values by the configuration of your device:
Set point value “1.SP“:
desired temperature
Proportional band “1.Pb“:
value identified in chapter A.2
Integral time “1.Int“:
3600
Derivative time “1.dEr“:
0 (off)
Cyclic time “1.CyC“:
2s (10s for inert control system)
Derivative time “1.dEr“ is switched off. The device works as PI-controller. Start the control and wait until the
temperature gets to the set point. If this takes too much time shorten the value of “1.Int“. To avoid overshoots
please watch how fast the temperature rises. Is the rise too small, shorten “1.Int“ again. Is the rise already
very big, raise “1.Int“. If “1.Int“ is not too small the temperature should be stable at the set point.
Now there has to be an external interference on the control system (i.e. fill in cold water, put a cold object
onto the controlled metal block, etc.). This interference should be a quite realistic to that under operating
conditions. If no external interference can be carried out, you can also change the set point value.
Watch how the device regulates the temperature to the set point. If there is a overshoot the “1.Int” value has
to be raised. If the temperature approach the set point only very slowly the “1.Int” value can be shorten.
Please consider to wait the settling time (up to several minutes for some control systems) after each change
of “1.Int”.
Your “1.Int” value is 1.2 times the value identified by that procedure.
4. Derivative time „1.dEr“
If cold water is filled in a heated water tank the temperate falls rapidly. A human operator, who regulates the
temperature of the tank manually, will intuitively turn immediately the full heating power on, then cut it down to
approach the set point by small changes of the heating power.
The D-action (derivative action) of the PID-controller is responsible for the intervention at that big by big tem-
perature changes. The D-action doesn’t react on the divergence between actual and set point temperature, but
on temperature changes. If the temperature falls very quickly there will be a big heating power due to the D-
action. If the actual temperature approaches the set point very fast the D-action reduces the heating power
calculated by the P- and I-action. If there is no temperature change the D-action is zero.
The strength of this effect is adjusted by the derivative time “1.dEr“. A small “1.dEr“ value means, that there is
only a small reaction on temperature changes. A big one means, that there is a big reaction on changes.
In a lot of application the use of the device as a PI-controller is entirely satisfactory. In this case set the deriva-
tive time “1.dEr“ to 0.
If the PID-control is needed, “1.dEr“ has to be identified. This requires exact information about the controlled
process and knowledge of control engineering. However, a derivative time “1.dEr“=Integral time “1.Int”/5 has
delivered an optimal performance in practice.
Your “1.dEr“ value is 0.2 times the “1.Int“ value.
5. Cyclic time “1.CyC“
The device regulates the heating power by switching the existing heating on and off. If only 50% of the ex-
isting heating power are needed the heating is only half the time switched on. The frequency switching on
and off is adjusted by the cyclic time “1.CyC“.
Example: existing heating power 1000 W, 600 W heating power are needed
At a period time T=10s: the device switches the heating on for 6s and then off for 4s
At a period time T=200s: the device switches the heating on for 120s and then off for 80s
If the cyclic “1.CyC“ is too high the temperature of the heated object will get too high during the switch-on
period (although „1.SP“, „1.Int“, „1.dEr“ are correct) , only to cool down in the following switch-off period.
A very small “1.CyC“ value means that the relays switches a lot of times and that shortens the durability.
Therefore the cyclic time is ideally set to that value that is as high as possible, but where the effect during the
switch-on and –off periods is just not perceptible.
Tips for identification of the Cyclic time “1.CyC“:
Raise the cyclic time as long as the of the controlling deterioration is just not perceptible.
Your „1.CyC“ is 08. times the value identified by that procedure.