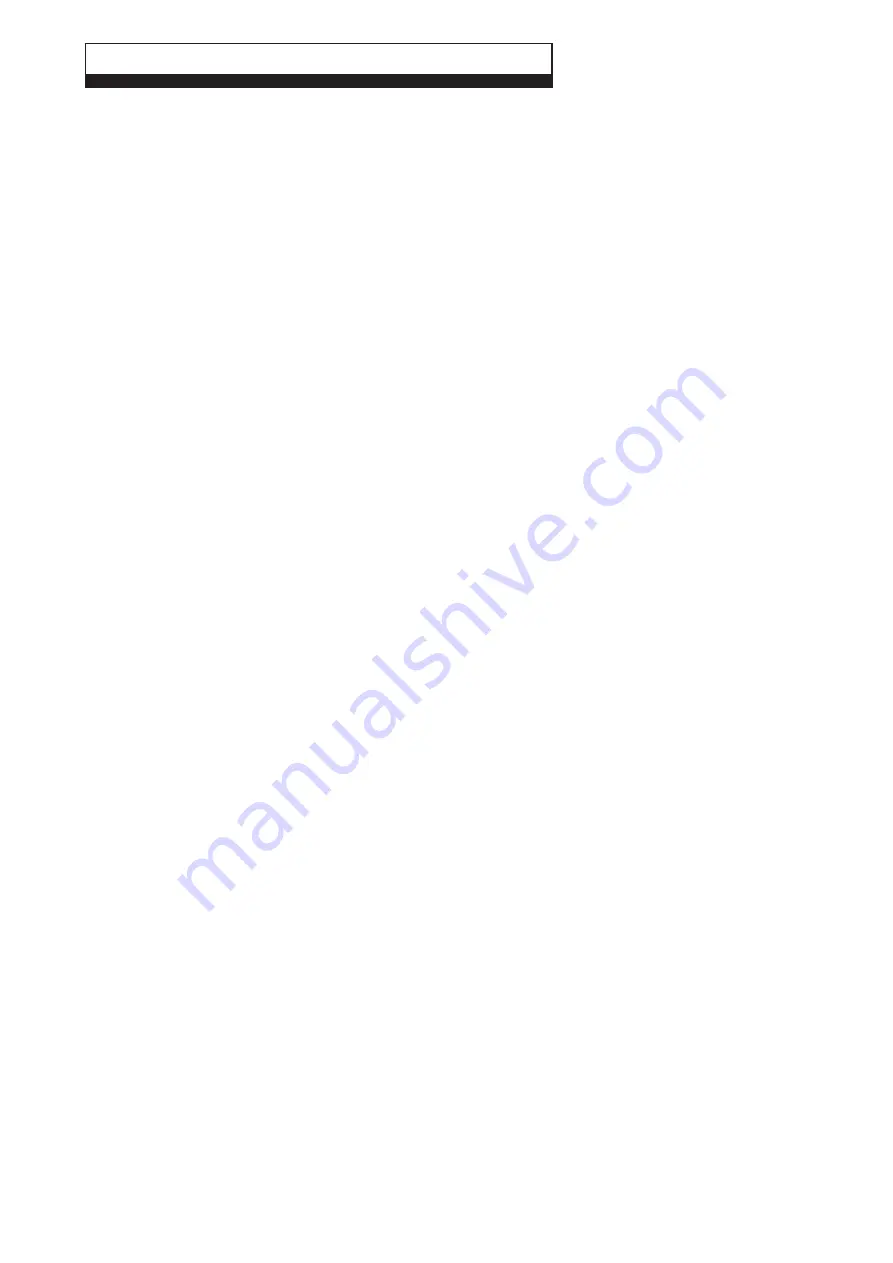
23
To ensure efficient operation of the boiler it is recommended that it is checked and serviced as necessary at regular
intervals. The frequency of servicing will depend upon the particular installation conditions and usage, but in general once
per year should be adequate.
It is the law that any service work must be carried out by a competent person, i.e. Gas Safe registered personnel.
Warning:
Before servicing the boiler, isolate the electrical supply and close the boiler gas service cock. Allow the boiler to
cool.
The data label is positioned on the inside of the right hand of the base plate.
Always test for gas tightness after servicing any gas carrying components.
Always carry out electrical system checks i.e. Earth Continuity, Resistance to Earth, Short Circuit and Polarity with a
suitable meter after servicing.
Notes: 1.
Prior to servicing, it is recommended that a flue gas analyser is used to measure the performance of the boiler
(refer to Fig. 3 or 4 for the position of the flue sampling point). If the CO/CO
2
ratio measured is greater than
0.003
or
when other checks and comments from the customer have indicated that there may be problems,
cleaning of the heat exchanger will be necessary. All Sections 6.1, 6.2, 6.3 and 6.4
must
be carried out.
Repeat the flue gas analyser test after reassembling the boiler and check that the CO/CO
2
ratio is less than
0.003.
2.
If the CO/CO
2
ratio measured is less than 0.003 and other checks and comments from the customer suggest
there are no problems then only Section 6.1 and Section 6.2 paragraphs 1, 2 and 3 need to be carried out to
allow a visual check of the components within the combustion chamber.
3.
If a flue gas analyser is not available, then all Sections 6.1, 6.2, 6.3 and 6.4
must
be carried out.
6.1
IMPORTANT NOTES PRIOR TO SERVICING
1.
Check the flue terminal outside and ensure it is not blocked.
2.
Run the boiler and check the operation of its controls.
3.
Refer to Fig. 3 or 4 for location of flue sampling point.
4.
Ensure that all system connections and fittings are sound.
5.
Refill, vent and re-pressurise the system as necessary. (Refer to Commissioning, Section 5.1).
If the system pressure exceeds 3.5 bar when operating at maximum temperature, the heating expansion vessel
should be checked and re-pressurised, if necessary.
Note:
Check the expansion vessel charge only when the system pressure is zero.
6.
Check that the condensate trap drain pipe is connected and all joints are sound.
7.
Record details of the service in the Service Record Section on page 32.
6.2
CASING REMOVAL - Fig. 23
If required, the casing can be completely removed as follows:
1.
Remove the bottom cover plate by removing its four fixing screws.
2.
Remove the two screws (item 1) securing the bottom of the casing front panel (item 5).
3.
Remove the screws (item 7) at the top of the cover (item 6).
4.
Pull the bottom of the casing front panel outwards while pushing upwards at the same time to remove it from the
boiler.
5.
Remove the two screws (item 2), each side, securing the side panels to the front support bracket.
6.
Remove the screws (item 3) at the bottom side of the boiler securing the bottom of the side panel (item 4), then push
upwards in order to remove the side panel.
Note:
If only the front panel is to be removed, remove the four screws securing the plastic top cover so that it can be lifted
slightly at the front edge. Remove the two fixing screws (item 1) (one each side at the bottom) securing the case front
panel. Pull the bottom of the panel outwards while pushing up at the same time and remove the panel
Alpha CD90S/115S - Routine Servicing
6
ROUTINE SERVICING