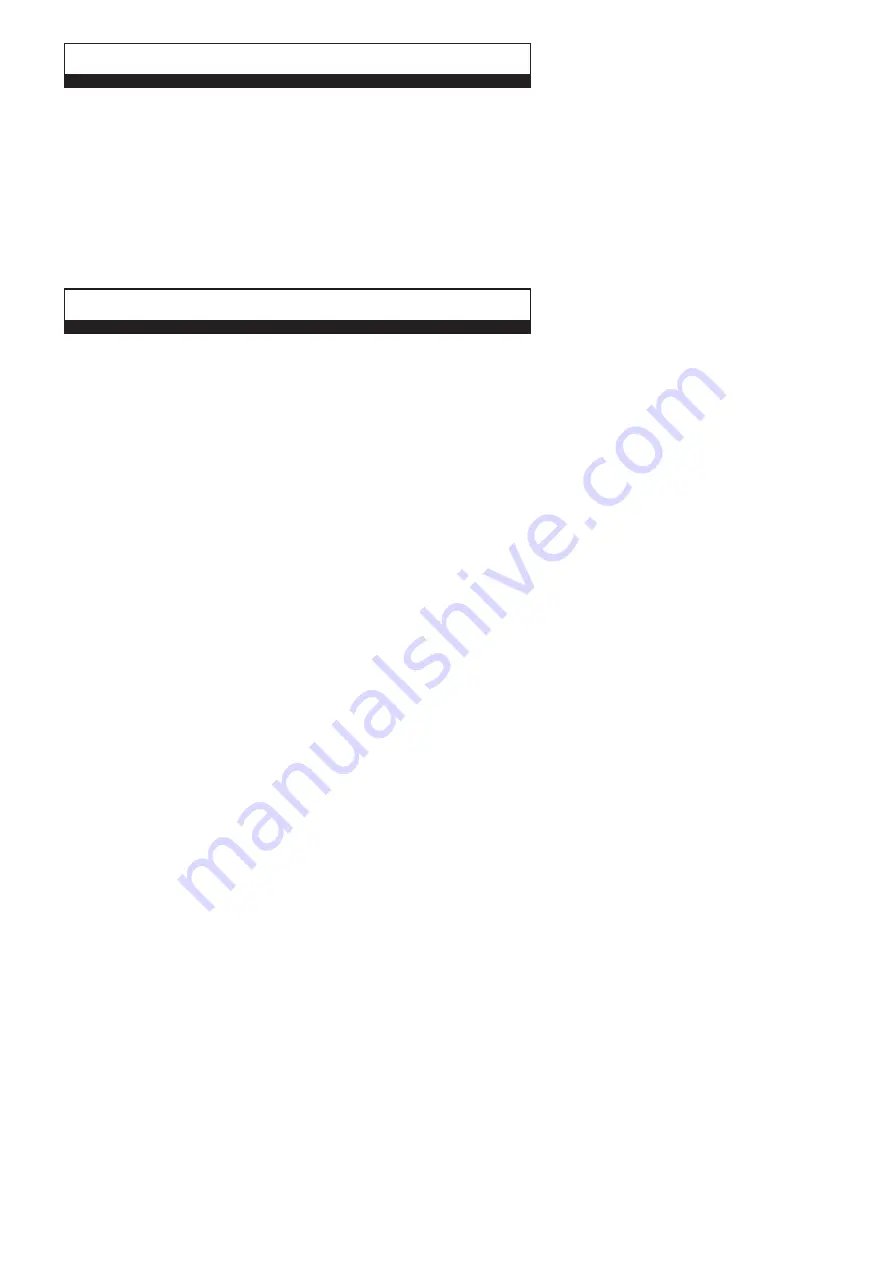
2
Alpha CD90S/115S - Contents/Introduction
CONTENTS
1
Introduction ....................................... 2
2
Technical data ................................... 3
3
General boiler information .................. 7
4
Installation ......................................... 14
5
Commissioning ................................. 18
6
Routine servicing ............................... 23
7
Wiring diagram .................................. 27
8
Fault finding ...................................... 28
9
Short parts list ................................... 30
10 Benchmark Checklist ......................... 31
11 Service record ................................... 32
The Alpha CD90S and 115S are wall mounted high efficiency condensing, fan assisted system boilers. The burner is lit
electronically and the heat output is controlled by a modulating fan and gas valve.
These are system boilers providing heating only for sealed central heating systems. However, they may be used with an
open central heating system if required - refer to Section 3.8.
The boilers are supplied with type B23 flue configuration (open chamber and forced draught) but can be changed to type C
(room sealed) by using a conversion kit.
The boilers are fitted with a pump, 4 bar pressure relief valve and pressure gauge fully assembled and tested. They are
designed for use with a fully pumped, sealed and pressurised central heating system. If used with an open system refer
to Section 3.8.
The CD90S boiler is suitable for central heating loads of between 22.5 and 90 kW (85 985 and 307 092 Btu/h).
The CD115S boiler is suitable for central heating loads of between 28.8 and 109 kw (98 269 and 371 923 Btu/h).
The boilers can be supplied for use with Natural gas or Propane Gas (LPG).
Note:
There are a number of additional controls and accessories available for use with the boilers to enable cascade and
zone installations to be used. Further information is available from Alpha Therm Ltd.
IMPORTANT
It is the law that all gas appliances are installed by a competent person, ie Gas Safe registered personnel, in accordance
with the following recommendations:-
Current Gas Safety (Installation and Use) Regulations
All current Building Regulations issued by the Department of the Environment, i.e. Approved Document L1.
Building Standards (Scotland) (Consolidation) Regulations issued by the Scottish Development Department
UK Water Regulations/Byelaws (Scotland)
Health & Safety Document No. 635 (The Electricity At Work Regulations 1989)
The installation should also be in accordance with the following British Standard Codes of Practice:-
BS 5295
Code of practice foe ventilation principles and designing for natural ventilation
BS 5854
Code of practice for flues and flue structures in buildings
BS 5978
Safety and performance of gas fired hot water boilers of rated inputs between 70 kW and 1.8 MW
BS 6644
Specification for installation of gas fired hot water boilers of rated inputs between 70 kW and 1.8 MW
BS 6700
Specification for design, installation, testing and maintenance of services supplying hot water for domestic use
within buildings and their curtilages.
BS 6981
Installation of low pressure gas pipework of up to 28 mm in domestic premises
BS 7074
Application selection and installation of expansion vessels and ancillary equipment for sealed water systems
Part 1 Code of practice for domestic heating and hot water
Part 2 Code of practice for low and medium temperature hot water system
BS 7593
Code of Practice for treatment of water in heating systems
BS 7671
Requirements for electrical installations, IEE Wiring Regulations
BS EN 12828 Design for water based heating systems
DOE
Chimney heights, Third edition of the Clean Air Act Memorandum
IGE/UP/1
Soundness testing and purging of industrial and commercial gas installations
IGE/UP/1A
Soundness testing and purging of small low pressure industrial and commercial natural gas installations
IGE/UP/4
Commissioning of gas fired plant on industrial and commercial premises
IGE/UP/10
Installation of gas appliances in industrial and commercial premises
Part 1 Flued appliances
IM/11
Flues for commercial and industrial gas fired boilers
Reference should be made to DEFRA document 'Guide to condensing boiler installation assessment procedures for dwellings'.
1
INTRODUCTION