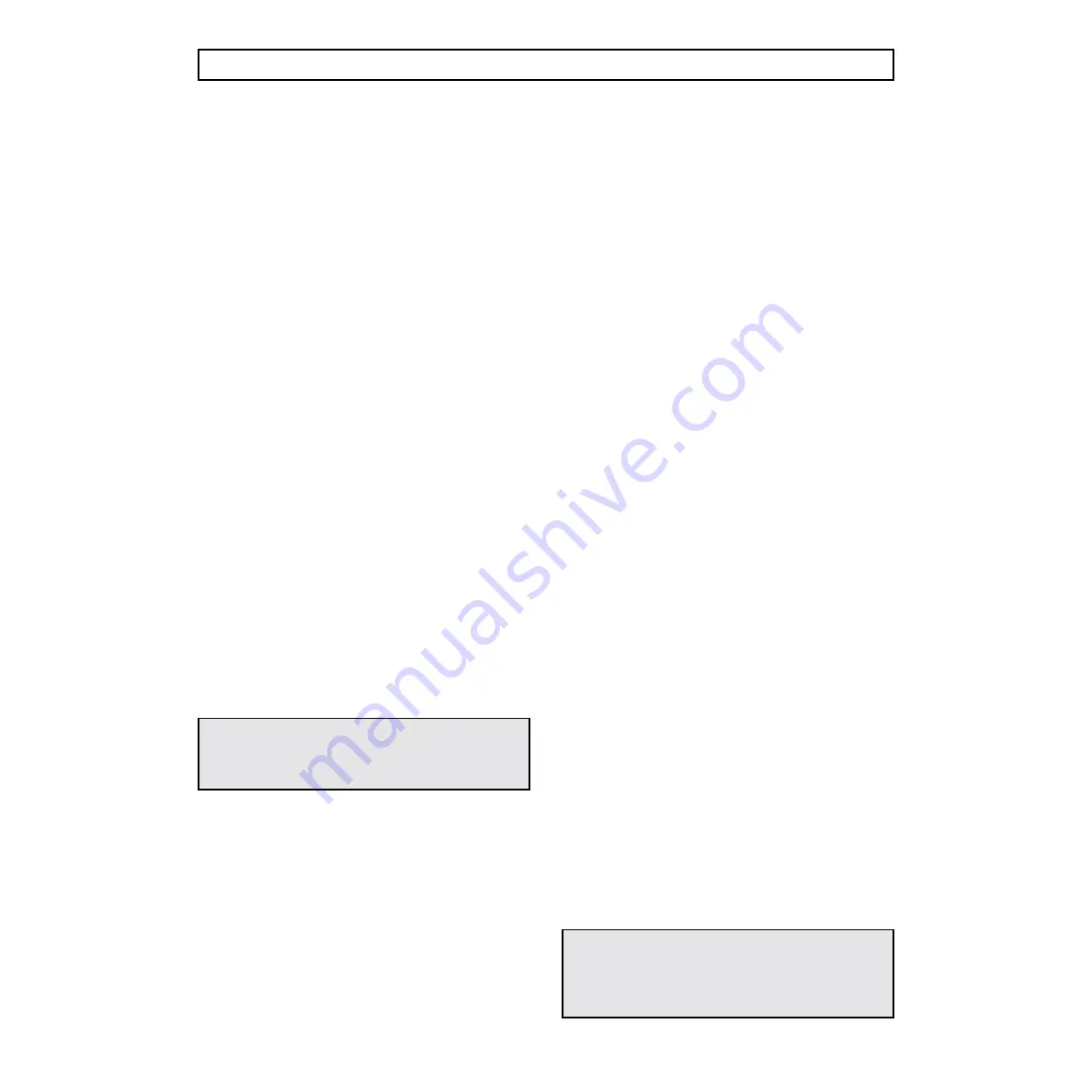
4–10
Copyright © 1996 General Motors Corp.
AT 500, 1500 SERIES AUTOMATIC TRANSMISSIONS
(2) If the bearings are particularly dirty or
filled with hardened grease, soak them in mineral spir-
its before trying to clean them.
(3) Before inspection, lubricate the bearings
with transmission fluid.
d.
Inspecting Bearings
(1) Inspect bearings for roughness of rota-
tion. Replace a bearing if its rotation is still rough after
cleaning and lubricating.
(2)
Inspect bearings for scored, pitted,
scratched, cracked, or chipped races, and for excessive
wear of rollers or balls. If one of these defects is
found, replace the bearing.
(3) Inspect bearing housing and shaft for
grooved, burred, or galled conditions that would indi-
cate that the bearing had been turning in the bore or on
the shaft. If the damage cannot be repaired with crocus
cloth, replace the defective part.
(4) When installing a bearing on a shaft, heat
the bearing to 200°F (93°C) in a hot transmission fluid
bath (approximately 30 minutes). Use the proper size
installation sleeve and a press to seat the bearing.
(5) If a bearing must be removed or installed
without a sleeve, press only on the race which is adja-
cent to the mounting surface. If a press is not avail-
able, seat the bearing with a drift and hammer, driving
against the supported race.
e.
Keeping Bearings Clean. Because the pres-
ence of dirt or grit in bearings is usually responsible
for bearing failures, it is important to keep bearings
clean during removal and installation. Observance of
the following rules will do much to ensure maximum
bearing life.
(1) Do not remove the wrapper from new
bearings until ready to install them.
(2) Do not remove the grease in which new
bearings are packed.
(3) Do not lay bearings on a dirty bench;
place them on clean, lint-free paper.
(4) If assembly is not to be completed at
once, wrap or cover the exposed bearings with clean
paper or lint-free cloth to keep out dust.
f.
Inspecting Cast Parts, Machined Surfaces
(1)
Inspect bores for wear, scratches,
grooves, and dirt. Remove scratches and burrs with
crocus cloth. Remove foreign matter. Replace parts
that have scratches or grooves that cannot be removed
with crocus cloth.
(2) Inspect all hydraulic passages for ob-
structions. If an obstruction is found, remove it with
compressed air, or by working a soft wire back and
forth through the passage and flushing it out with
cleaning solvent.
(3) Inspect mounting faces for nicks, burrs,
scratches, and foreign matter. Remove such defects
with crocus cloth or a soft stone. If scratches cannot be
removed with crocus cloth, replace the part.
(4) Inspect threaded openings for damaged
threads. Chase damaged threads with the correct size
used tap (a new tap can cut oversize). A threaded insert
may be used if the insert will not be subjected to high
hydraulic pressure. Inserts used in high pressure areas
will leak fluid.
(5) Inspect snapring grooves in transmission
housing for nicks or shavings that would prevent the
snaprings from fully seating in the grooves. Clean up
any damage with crocus cloth.
(6) Replace housings or other cast parts that
are cracked. Magnaflux and rinse planetary carriers us-
ing approximately 8000 ampere-turns (8 amperes in
1000 turn coil) to determine if fractured. Replace the
carrier if cracked.
(7) Inspect all machined surfaces for damage
that could cause fluid leakage or other malfunction of
the part. Rework or replace the defective parts.
CAUTION:
Replace any bearing that has been subjected to
metal contamination (Paragraph 3–9b).
CAUTION:
Distortions and imperfections in the hydraulic
circuit tracks will cause severe fluid leakage lead-
ing to transmission failure.