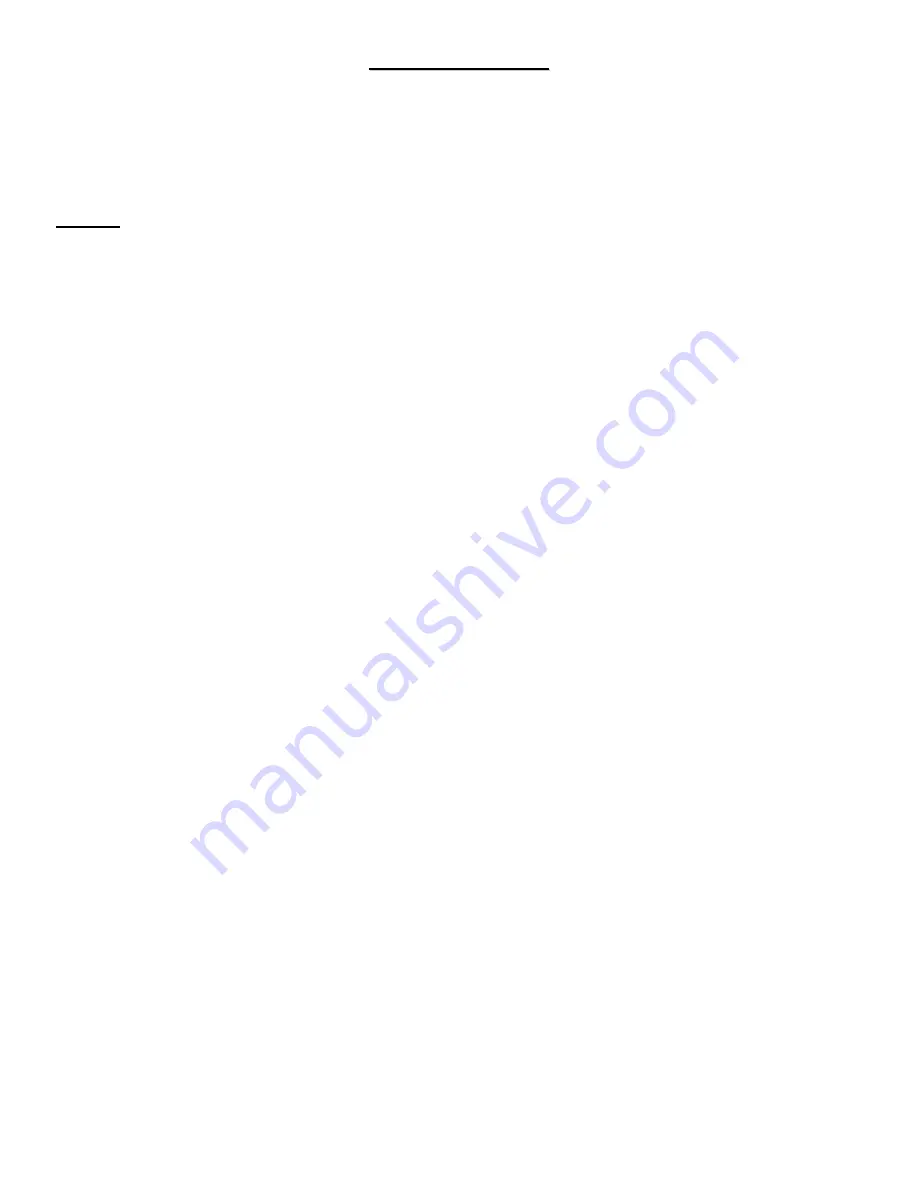
LIMITED W
LIMITED W
ARRANTY
ARRANTY
Allen Engineering Corporation warrants its products to be free of defects in material or workmanship for the fol-
lowing periods:
A. All New Machines and Part
6 Months
B. All New Gear Boxes
2 Years
C. All Factory Reconditioned Gear Boxes
1 Year
NOTICE:
The engine RPM has been set at the factory at a maximum of 3,900. Any evidence of tampering to
increase the RPM above 3,900 will immediately void the warranty with both Allen Engineering Corporation and the
engine manufacturer.
Warranty period begins on first day of use by End User. This first day of use is established by a completed warran-
ty card or a Bill of Sale to the end user. All warranty is based on the following limited warranty terms and conditions.
1.) Allen Engineering Corporation’s obligation and liability under this warranty is limited to repairing or replacing
parts if, after Allen’s inspection, it is determined to be a defect in material or workmanship. Allen Engineering
Corporation reserves the choice to repair or replace.
2.) If Allen Engineering Corporation chooses to replace the part, it will be at no cost to the customer and will be made
available to the Distributor/Dealer from whom the customer purchased the product.
3.) Replacement or repair parts, installed in the product, are warranted only for the remainder of warranty period of
the product as though they were the original parts.
4.) Allen Engineering Corporation’s warranty applies only to the products that are manufactured by Allen
Engineering and does not cover component parts such as engines and clutches. Allen Engineering Corporation
DOES NOT warranty clutches. Engine warranty claims should be made directly to an authorized factory service cen-
ter for the particular engine make.
5.) Allen Engineering Corporation’s warranty does not cover the normal maintenance of products or its components
(such as engine tune-ups and oil changes). The warranty also does not cover normal wear and tear items (such as
belts and consumables).
6.) Allen Engineering Corporation’s warranty will be void if it is determined that the defect resulted from operator
abuse, failure to perform normal maintenance on the product, modification to product, alterations or repairs made
to the product without the written approval of Allen Engineering Corporation. Allen Engineering Corporation specifi-
cally excludes from warranty any damage to any trowels resulting from an impact to the rotors. Allen Engineering
Corporation also excludes from warranty any failure of clutches on any engine driven piece of equipment.
7.) If a new gear box has a factory defect within the first year of use, Allen Engineering Corporation will either repair
the gear box or replace it with a new gear box. If a new gearbox has a factory defect in the second year of use, Allen
Engineering Corporation will either repair it or replace it with a factory reconditioned gear box. Impact damage is NOT
covered under the gear box warranty.
8.) Allen Engineering Corporation will pay shop labor repair on warranty at the Allen Engineering Shop Labor Rate in
existence on the date of the warranty claim. An Allen Engineering Labor Chart will determine the time allowed to com-
plete a repair and will govern the shop labor hours that will be allowed.
9.) Allen Engineering Corporation will pay freight on warranty replacement parts at Worldwide standard ground rates.
No warranty replacement parts will be shipped air freight at the expense of Allen Engineering Corporation. Allen
Engineering only pays outbound freight charges when sending warranty replacement parts to the customer VIA
ground service. Allen Engineering does not pay any inbound freight, however, if Allen Engineering determines this to
be warranty defect only then will Allen Engineering reimburse the customer for inbound freight at standard ground
rates.
10.) Allen Engineering Corporation’s warranty policy WILL NOT COVER the following; taxes, shop supplies, envi-
ronmental surcharges, air freight, travel time, loss of rental revenue, or any other charges whatsoever or any liabili-
ties for direct, incidental, or consequential damage or delay.
11.)
Allen Engineering Corporation makes no other warranty, expressed or implied. This limited warranty is
in lieu of the warranty of merchantability and fitness. There are no other warranties that extend beyond the
description on this document.
12.) No Allen Engineering Corporation employee or representative is authorized to change this warranty in any way
or grant any other warranty unless such change is made in writing and signed by an officer of Allen Engineering
Corporation.
Содержание HD 550
Страница 24: ...2A PARTS LEFT HAND CROSSHEAD SPIDER ASSEMBLY 2A 4...
Страница 26: ...2A 6 2A PARTS RIGHT HAND CROSSHEAD SPIDER ASSEMBLY...
Страница 28: ...2A PARTS 2A 8 PITCH AND STEERING HYDRAULIC SCHEMATIC...
Страница 29: ...2A PARTS 2A 9 HYDRAFORCE MANIFOLD HYDRAULIC SCHEMATIC...
Страница 30: ...2A PARTS 2A 10 CLOSED LOOP SYSTEM HYDRAULIC SCHEMATIC...
Страница 31: ...2A PARTS 2A 11 ELECTRICAL DIAGRAM F HD 550...