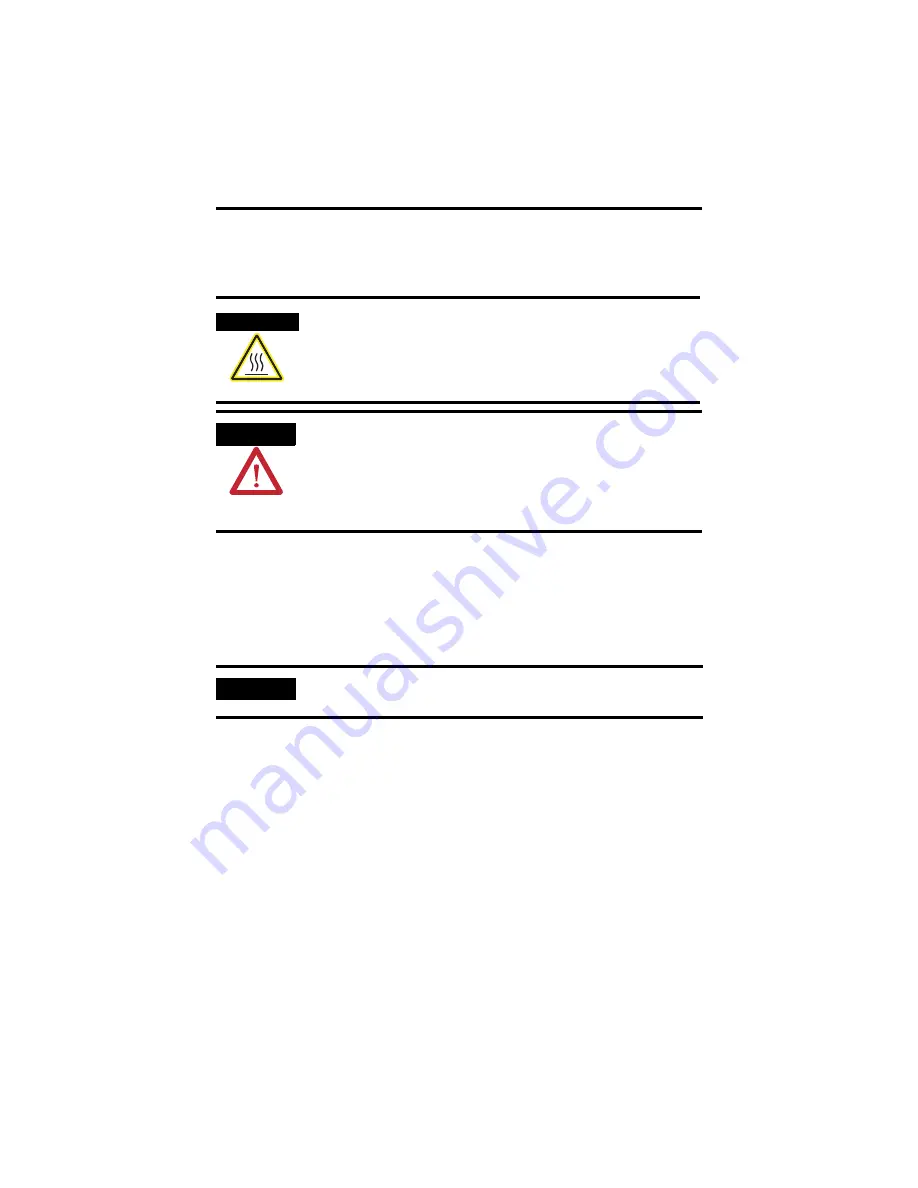
RDD-Series Rotary Direct Drive Bearingless Motor Installation Instructions
19
Publication RDB-IN002A-EN-P — October 2009
Remove the Motor
Remove the motor from a machine as outlined below.
Remove the End Cover
Loosen each pan head screw with a Phillips screwdriver.
• The RDB-
x
290
x
motor has eight (8) screws to loosen.
• The RDB-
x
410
x
motor has eleven (11) screws to loosen.
Outer surfaces of a motor can reach high temperatures, 125 °C (275 °F), during operation.
Take precautions to prevent accidental contact with hot surfaces. Consider motor surface
temperature when selecting connections and cables to install on a motor.
Failure to observe safety precautions could result in personal injury or damage to
equipment.
ATTENTION
Servo drive power must be turned off before connecting or disconnecting the cables to the
motor, and if a cable is left disconnected at the motor end.
Arcing or unexpected motion could occur if the feedback, power, or brake cables are
connected or disconnected while power is applied to the servo drive.
Failure to observe these safety procedures could result in personal injury or damage to the
motor and equipment.
IMPORTANT
Do not attempt to remove the pan head screws from the cover. The screws are affixed to
the end cover with a mechanical lock-ring.
BURN HAZARD