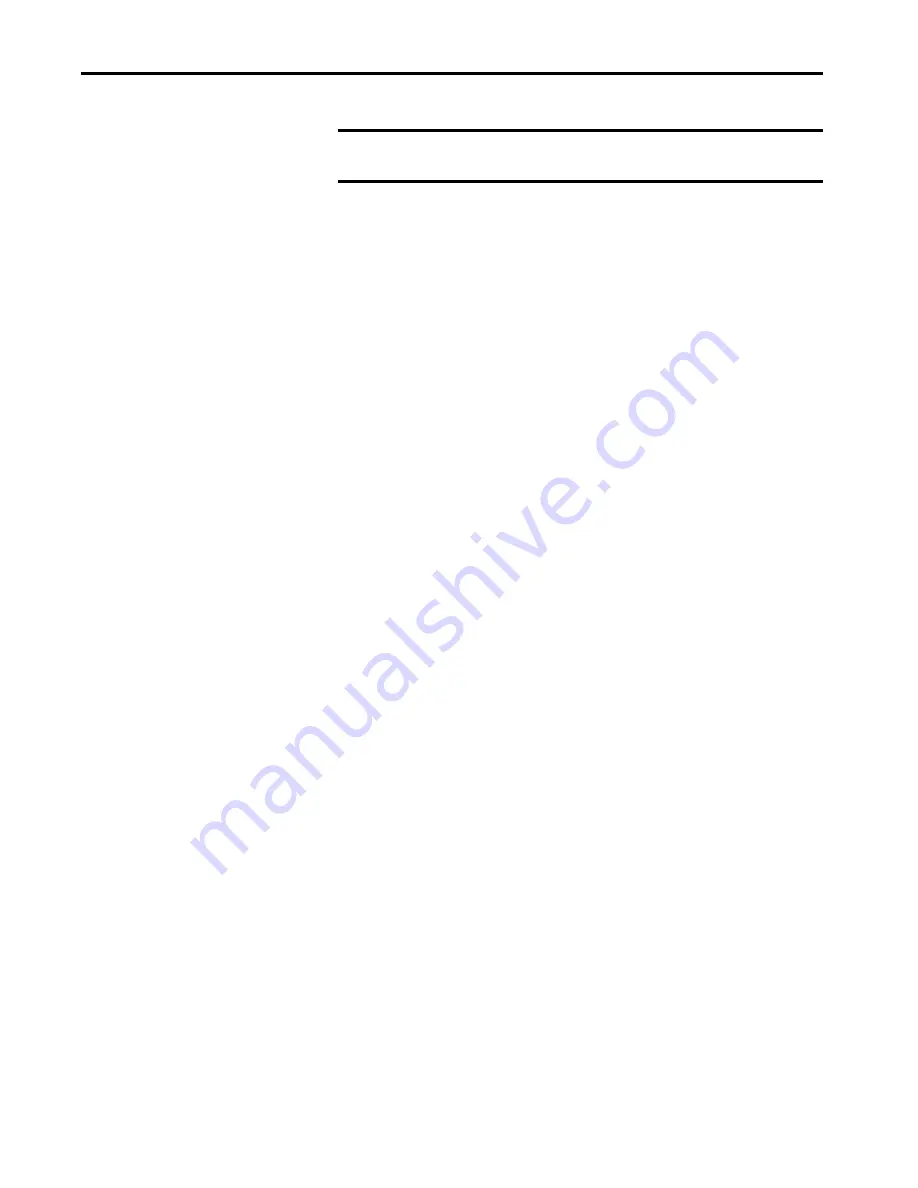
Rockwell Automation Publication 1756-UM022D-EN-P - May 2017
161
Change Controller Type
Appendix B
Change Safety Controller
Types
When you change from one safety controller type to another, the class of tags,
routines, and programs remain unaltered. Any I/O devices that are no longer
compatible with the target controller are deleted.
The representation of the safety partner is updated to appear appropriately for
the target controller:
• The safety partner is created in slot
x
(primary slot + 1) when changing
from a 1768 Compact GuardLogix to a GuardLogix 5570 controller.
• When changing to a 1768 Compact GuardLogix controller, the safety
partner is removed because it is internal to the Compact GuardLogix
controller.
Floating-point instructions, such as FAL, FLL, FSC, SIZE, CMP, SWPB, and
CPT are supported in GuardLogix 5570 controllers, but not in GuardLogix
5560 and 1768 Compact GuardLogix controllers. If your safety program
contains these instructions, verification errors can occur when changing
from a GuardLogix 5570 controller to a GuardLogix 5560 or
1768 Compact GuardLogix controller.
IMPORTANT
1768 Compact GuardLogix controllers and GuardLogix 5560 controllers are
not supported in the Logix Designer application, version 21.
TIP
A GuardLogix 5570 controller supports 100 safety programs in the safety
task while a 1768 Compact GuardLogix controller supports 32.
Содержание GuardLogix 5570
Страница 8: ...8 Rockwell Automation Publication 1756 UM022D EN P May 2017 Table of Contents...
Страница 20: ...20 Rockwell Automation Publication 1756 UM022D EN P May 2017 Chapter 1 System Overview Notes...
Страница 46: ...46 Rockwell Automation Publication 1756 UM022D EN P May 2017 Chapter 2 Install the Controller Notes...
Страница 56: ...56 Rockwell Automation Publication 1756 UM022D EN P May 2017 Chapter 3 Configure the Controller Notes...
Страница 124: ...124 Rockwell Automation Publication 1756 UM022D EN P May 2017 Chapter 6 Develop Safety Applications Notes...
Страница 134: ...134 Rockwell Automation Publication 1756 UM022D EN P May 2017 Chapter 7 Go Online with the Controller Notes...
Страница 162: ...162 Rockwell Automation Publication 1756 UM022D EN P May 2017 Appendix B Change ControllerType Notes...
Страница 169: ...Rockwell Automation Publication 1756 UM022D EN P May 2017 169 Index Notes...
Страница 170: ...170 Rockwell Automation Publication 1756 UM022D EN P May 2017 Index Notes...
Страница 171: ......