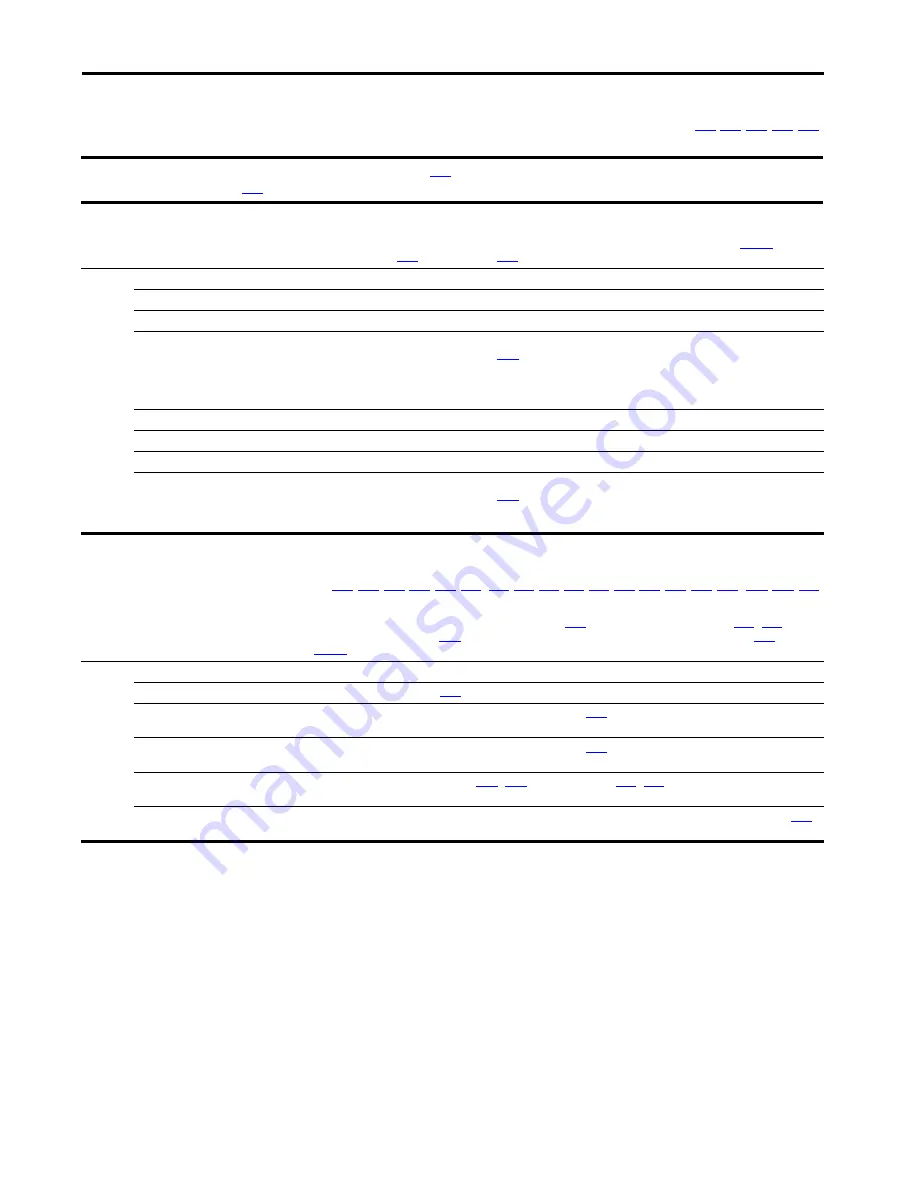
Rockwell Automation Publication 22C-UM001J-EN-E - January 2017
63
Programming and Parameters
Chapter 3
P037 [Stop Mode]
Related Parameter(s):
,
Active stop mode for all stop sources [e.g. keypad, run forward (I/O Terminal 02), run reverse (I/O Terminal 03), RS485 port] except as noted below.
Hardware Enable Circuitry
By default, I/O Terminal 01 is a coast to stop input. The status of the input is interpreted by drive software. If the application requires the drive to be disabled without software
interpretation, a “dedicated” hardware enable configuration can be utilized. This is accomplished by removing the ENBL enable jumper on the control board. See
for details.
In this case, the drive will always coast to a stop regardless of the settings of
[Start Source] and
[Stop Mode].
Options
0 “Ramp, CF”
(1)
Ramp to Stop. “Stop” command clears active fault.
1 “Coast, CF”
(1)
(Default)
Coast to Stop. “Stop” command clears active fault.
2 “DC Brake, CF”
(1)
DC Injection Braking Stop. “Stop” command clears active fault.
3 “DCBrkAuto,CF”
(1)
DC Injection Braking Stop with Auto Shutoff.
• Standard DC Injection Braking for value set in
[DC Brake Time].
OR
• Drive shuts off if the drive detects that the motor is stopped.
“Stop” command clears active fault.
4 “Ramp”
Ramp to stop.
5 “Coast”
Coast to stop.
6 “DC Brake”
DC Injection Braking Stop.
7 “DC BrakeAuto”
DC Injection Braking Stop with Auto Shutoff.
• Standard DC Injection Braking for value set in
[DC Brake Time]
OR
• Drive shuts off if the drive detects that the motor is stopped.
(1) Stop input also clears active fault.
IMPORTANT
I/O Terminal 01 is always a coast to stop input except when
[Start Source] is set for “3-Wire” control. When in three wire control, I/O Terminal 01 is
controlled by
[Stop Mode].
P038 [Speed Reference]
,
,
,
,
,
,
,
Sets the source of the speed reference to the drive.
The drive speed command can be obtained from a number of different sources. The source is normally determined by
[Speed Reference]. However, when
[Digital
Inx Sel] is set to option 1, 2, 3, 4, 5, 8, 14, 15, 16, 17 and the digital input is active, or if
[PID Ref Sel] is not set to option 0, the speed reference commanded by
[Speed
Reference] will be overridden. Refer to the flowchart on
for more information on speed reference control priority.
Options
0 “Drive Keypad”
Internal frequency command from the digital speed keys on the integral keypad.
1 “InternalFreq”
Internal frequency command from
[Internal Freq]. Must be set when using MOP function.
2 “Analog In 1” (Default)
External frequency command from an analog source as determined by
[Analog In 1 Sel] and DIP Switch AI1 on the control
board. Default Dip Switch setting is 10V.
3 “Analog In 2”
External frequency command from an analog source as determined by
[Analog In 2 Sel] and DIP Switch AI2 on the control
board. Default Dip Switch setting is 10V.
4 “Preset Freq”
External frequency command as defined by
...
[Digital Inx Sel] are programmed as
“Preset Frequencies” and the digital inputs are active.
5 “Comm Port”
External frequency command from the communications port. Refer to Appendix E and Appendix G for details. Parameter
[Comm Format] is used to select a communications protocol.
Содержание 22C-B012N103
Страница 8: ...6 Rockwell Automation Publication 22C UM001J EN E January 2017 Summary of Changes Notes...
Страница 46: ...44 Rockwell Automation Publication 22C UM001J EN E January 2017 Chapter 1 Installation Wiring Notes...
Страница 56: ...54 Rockwell Automation Publication 22C UM001J EN E January 2017 Chapter 2 Start Up Notes...
Страница 154: ...152 Rockwell Automation Publication 22C UM001J EN E January 2017 Appendix B Accessories and Dimensions Notes...
Страница 176: ...174 Rockwell Automation Publication 22C UM001J EN E January 2017 Appendix E Modbus RTU Protocol Notes...
Страница 192: ...190 Rockwell Automation Publication 22C UM001J EN E January 2017 Appendix G P1 FloorLevel Network FLN Notes...
Страница 195: ......