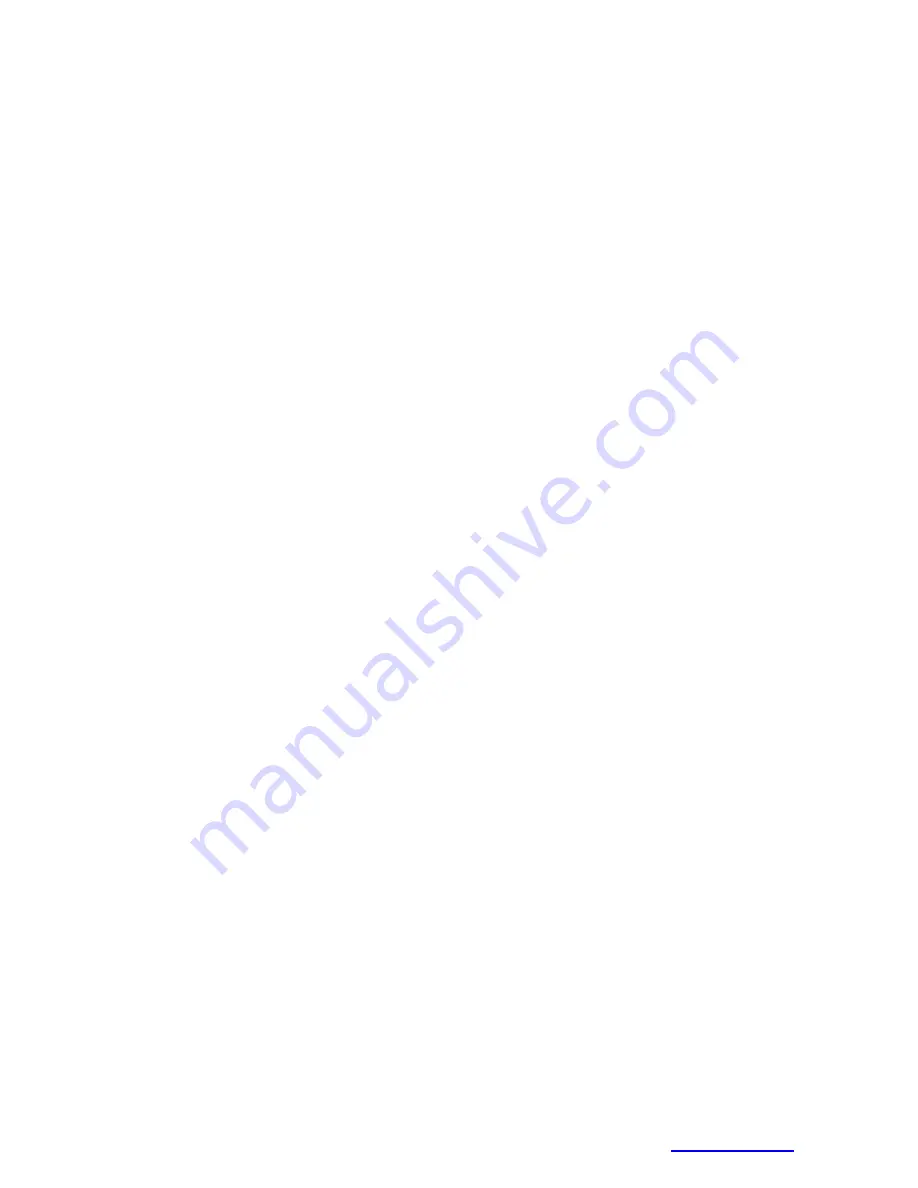
-4-
ALFA
IN
a.s.
©
www.alfain.eu
2
SAFETY INSTRUCTIONS AND WARNINGS
Once the packing has been opened, make sure that the machine is not
damaged. If in any doubt, call the service centre.
This equipment must only be used by qualified personnel.
During installation, any electric work must only be carried out by trained
personnel.
The machine must be used in a dry place with good ventilation.
Make sure that no metal dust can be drawn in by the fan inside the machine,
as this could cause damage to the electronic circuits.
It is prohibited to connect more than one INVERTER generator in series or in
parallel.
When installing the machine, follow the local regulations on safety.
The position of the machine must allow easy access by the operator to the
controls and connectors.
When the welding machine is operating, all its covers and doors must be
closed and well fixed.
Do not expose the welding machine to direct sunlight or to heavy rain. This
equipment conforms to protection rating IP23S.
During welding, the welding cables must be located near or at ground level.
They should be as short as possible.
The operator must wear gloves, clothes, shoes, and a helmet or a welder’s
helmet, which protect and are fire-resistant in order to protect him against
electric shock, flashes and sparks from welding.
The operator must protect his eyes with safety visor or mask designed for
welding, fitted with standard safety filters. He should also be aware that during
electrical welding ULTRAVIOLET RADIATION is emitted. Therefore it is vital
that his face is also protected from radiation. Ultraviolet rays produce the same
harmful effect as sun burning on unprotected skin.
The operator is obliged to warn anyone near the welding area of the risks that
welding involves and to arrange to provide adequate protection equipment.
It is very important to arrange for sufficient ventilation, especially when welding
in enclosed spaces. We suggest using suitable fume extractors to prevent the
risk of intoxication by fumes or gas generated by the welding process.
The operator must ensure all flammable materials are removed from the work
area to avoid any risk of fire.
The operator must NEVER weld containers that have previously contained
petrol, lubricants, gas or similar flammable materials, even if the container has
been empty for a considerable time. THERE IS A VERY HIGH RISK OF
EXPLOSION.
The operator must be aware of all the special regulations which he needs to
conform to when welding in enclosed spaces with a high risk of explosion.
To prevent electric shock, we strongly suggest the following rules:
Do not work in a damp or humid environment.
Do not use the welding machine if its cables are damaged in any way.