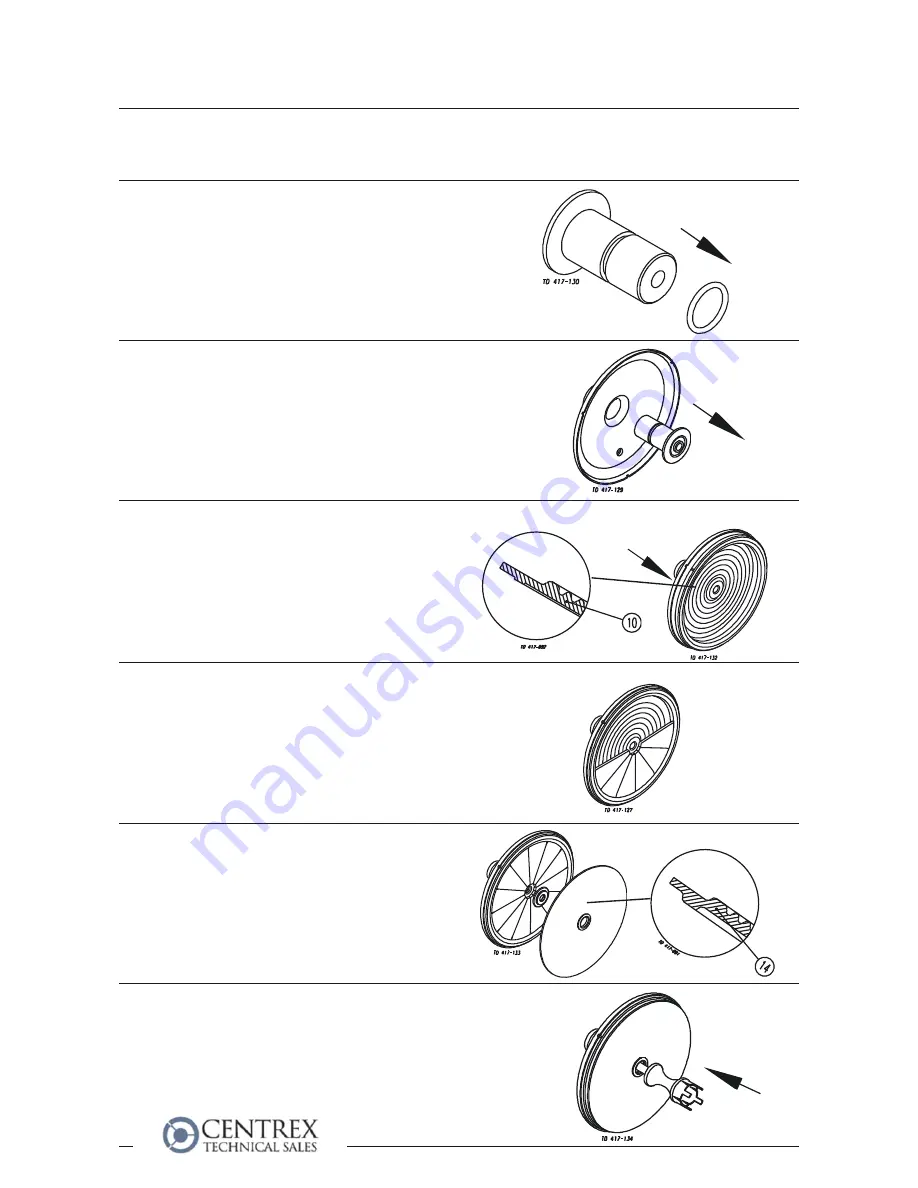
18
Study the instructions carefully.
The items refer to the parts list and service kits section.
Lubricate the guide, the sectors and the threads before assembly.
CPMI-2: Constant-Pressure Modulating Inlet. CPMO-2: Constant-Pressure Modulating Outlet.
Step 1
Fit O-ring (8)
Step 2
Lubricate guide (9) and fit it into cover (7).
NOTE!
Turn cover (7) downwards before continuing.
Step 3
Fit upper diaphragm (10), upper inner ring (11) and outer ring
(13) on guide (9) and cover (7).
NOTE!
The upper diaphragm has a small recess.The outer ring must
be fitted with the recess turned uppermost so that the
indication hole is fixed opposite the indication hole in the cover.
Step 4
Fit sectors (12) between upper inner ring (11) and outer ring
(13).
Step 5
Fit lower inner ring (11) and lower diaphragm (14).
Concentric grooves should point towards the steel segments.
Step 6
CPMI-2:
Fit plug (15a) in the diaphragm unit and guide (9) until the flange
of the plug contacts lower diaphragm (14).
Fit the correct diaphragm!
(Air side)
Fit the correct diaphragm!
4.3 Assembly
4. Maintenance