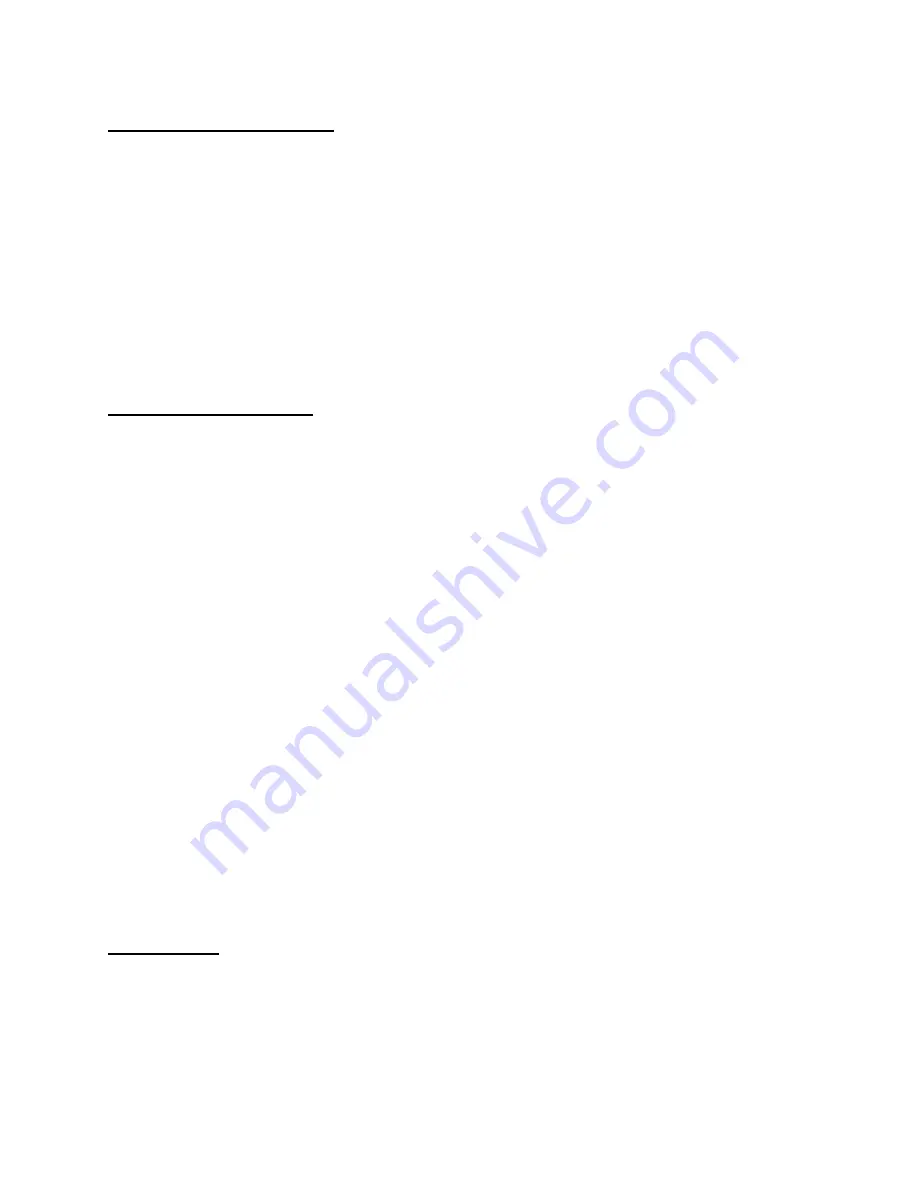
3
Lubrication and Filters
a)
Use only Airworks certified and approved fluids and filters
b)
Compressor may be under pressure; ensure pressure is released and unit is switched off
and unloaded before servicing, remove fill cap slowly
– stop if pressure is present until
compressor unloads.
c)
Oil filters are spin-on type
d)
Air filters are paper element replaceable
e)
Spin on coalescing separator element
Operating Principals
The system uses a flooded lobe, rotary screw compressor. The oil filled compressor contains
two synchronous rotors turning at a variable speed.
When air at atmospheric pressure is introduced into the housing, by the inlet control valve it is
trapped between the rotors allowing for compression.
A lubricated pitch line provides sealing. As the lobes on the rotors mesh, they reduce the
volume of air, compressing it to the desired pressure.
Oil separation occurs in two stages.
1. Mechanical; where the air/oil is first separated through a series of baffles
2. The coalescing filter.
A liquid to liquid cooling system is used to maintain compressor oil temperature. This system
uses the cooling system of the prime mover to act as a heat sink for heat transfer and may also
use an air to oil cooler.
Rotary screw compressors are machined to close tolerances and ingestion of foreign objects into
the system will rapidly damage or shorten the life expectancy of the unit.
Direct coupled engine and compressor drive improves efficiency and reduces moving parts.
Important
Driving on rough terrain while your unit is running may cause damage to be incurred. Shut your unit off
prior to moving your vehicle to prevent this.