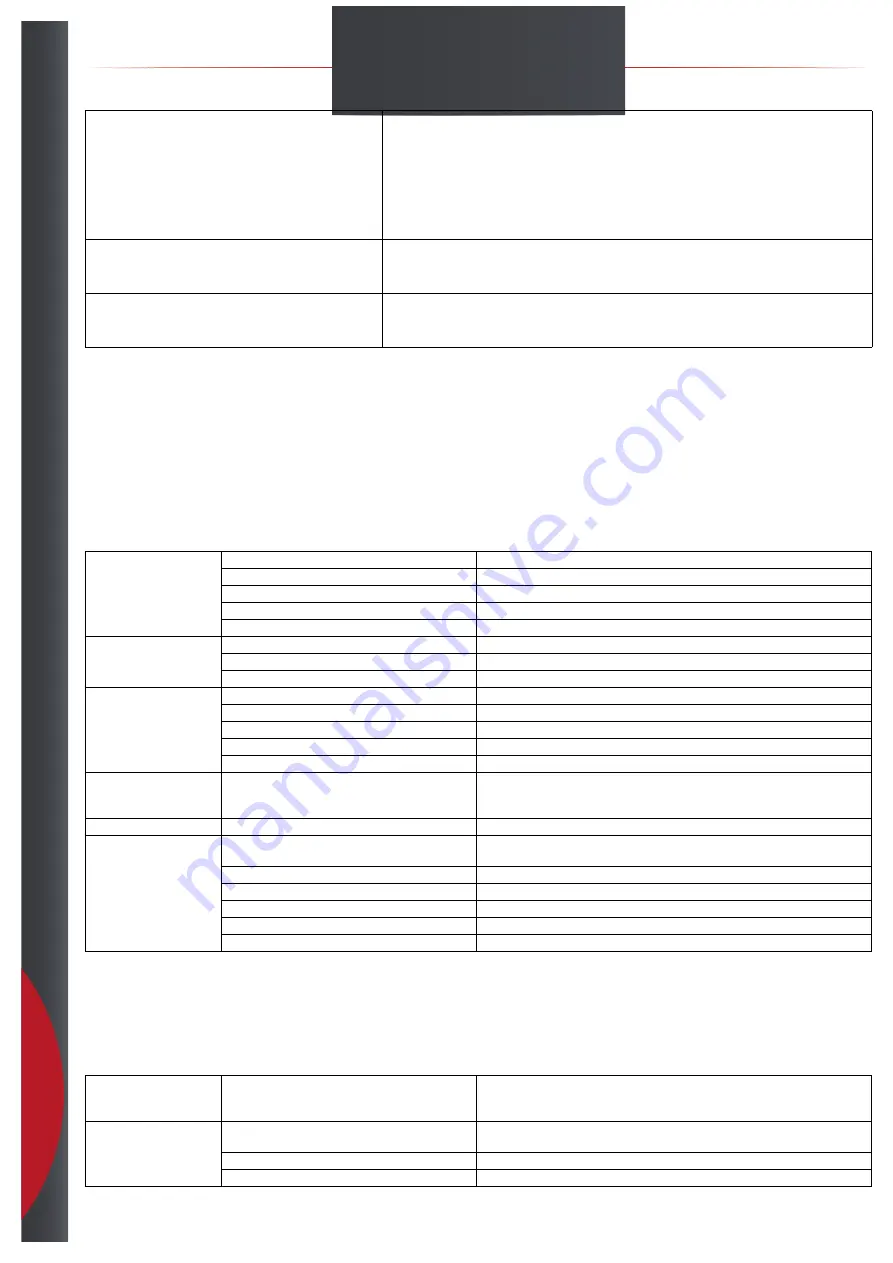
84
Solving the problem
Having run through the above 10 steps, you are now ready to solve whatever problems have been uncovered. The next section tells specifically how to resolve common complaints and problems with water
treatment systems.
Softening - hard water
Problem
Cause
Solution
1. Water meter disc is not
turning.
Non-conforming meter drive pawl.
Replace meter drive pawl.
Meter drive spring installed wrong.
Reinstall meter drive spring.
”No back pawl” isn’t installed.
Install ”no back pawl”.
Damaged tooth on the meter disc.
Replace meter disc.
Damaged gear in the gearing stack.
Regear Level 1 Assembly and check allowable flow rates.
2. The unit will not go into
automatic regeneration.
Water meter disc is not turning.
See number 1 above.
Control disc will not automatically advance out of service position Replace regeneration start pawl.
Damaged teeth on control disc.
Replace control disc.
3. No vacuum in brine position.
Check stems or balls is missing or not working correctly.
Replace or add check stems.
Clogged venturi.
Clean out Level 3 venturi throat and molded venturi nozzle (do not use a paper clip!).
Clogged backwash flow control.
Clean out backwash flow control.
Clogged brine elbow screen.
Clean out brine elbow screen.
Dammaged outlet main valve seat seal.
Replace main valve seat seal.
4. Short saltning.
The brine level is not level. The grid system allows a water level
no more than 1” above the grid. If the brine drum isn’t level, it
may excess this.
Level the brine drum.
5. Bridget salt in the brine drum. Salt has solidified in the drum.
Carefully move the salt around to break the mass of solidified salt.
6. Brine drum dosn’t refill or
overfills.
The brine valve is set incorrectly.
Set the brine valve according to instructions on the brine valve installation sheet in the owner’s pack or
tech manual.
The brine valve is non-conforming.
Replace the brine valve.
The brine drum is dirty.
Clean out the brine drum.
The venturi nozzle is clogged.
Clean out Level 3 venturi throat and molded venturi nozzle (do not use a paper clip!)
The brine elbow screen is clogged..
Remove and clean brine elbow screen.
The brine flow control is clogged.
Clean or replace the brine flow control.
Softening - frequent regeneration / backwash
Problem
Cause
Solution
1. The customer does not
understand Kinetico units.
If customers previously owned an electric unit with timer based
regeneration, they may not realize that Kinetico units can
regenerate at any time of the day or night.
Explain to the customer how the Kinetico softener works.
Emphasize that regeneration is controlled by the measurement of water use rather than on an
arbitrary timed basis.
2. The unit does regenerate too
frequently.
Incorrectly labeled meter disc. Verify that the number of slots on
the disc match the number molded on the disc.
Install the correct meter disc.
Meter disc not moving and start pawl in gap.
Refer to ”Softening - hard water” section, step 1.
Incorrect Meter Nozzle.
Vertify meter nozzle and replace if necessary.
8. Measure water pressure
Low water pressure can cause hard water and/or salty water.
Measure the water pressure:
1. Adapt a pressure gauge to the brine fitting port on level 3.
2. Turn on one cold water faucet wide open.
3. Place either tank in the backwash portion of cycle.
Did the pressure drop below 1 bar / 15 psi at the brine fitting?
The Kinetico valve requires a minimum of 1 bar / 15 psi to function properly.
9. Measure backwash flow rate
Too little backwash flow can cause salty water.
Measure the amount of water coming out of the drain line during the backwash portion of cycle.
•
Is it less than the backwash rate on the specification sheet?
10. Check unit shut-off
The drain should be dry at the service positions (12 o’clock and 6 o’clock).
An occasional drip may occur. Measure the drip rate. There should be less than 5 ml of water collected in 22 seconds.
•
Is the drain running or dripping excessively in the service positions?
201218