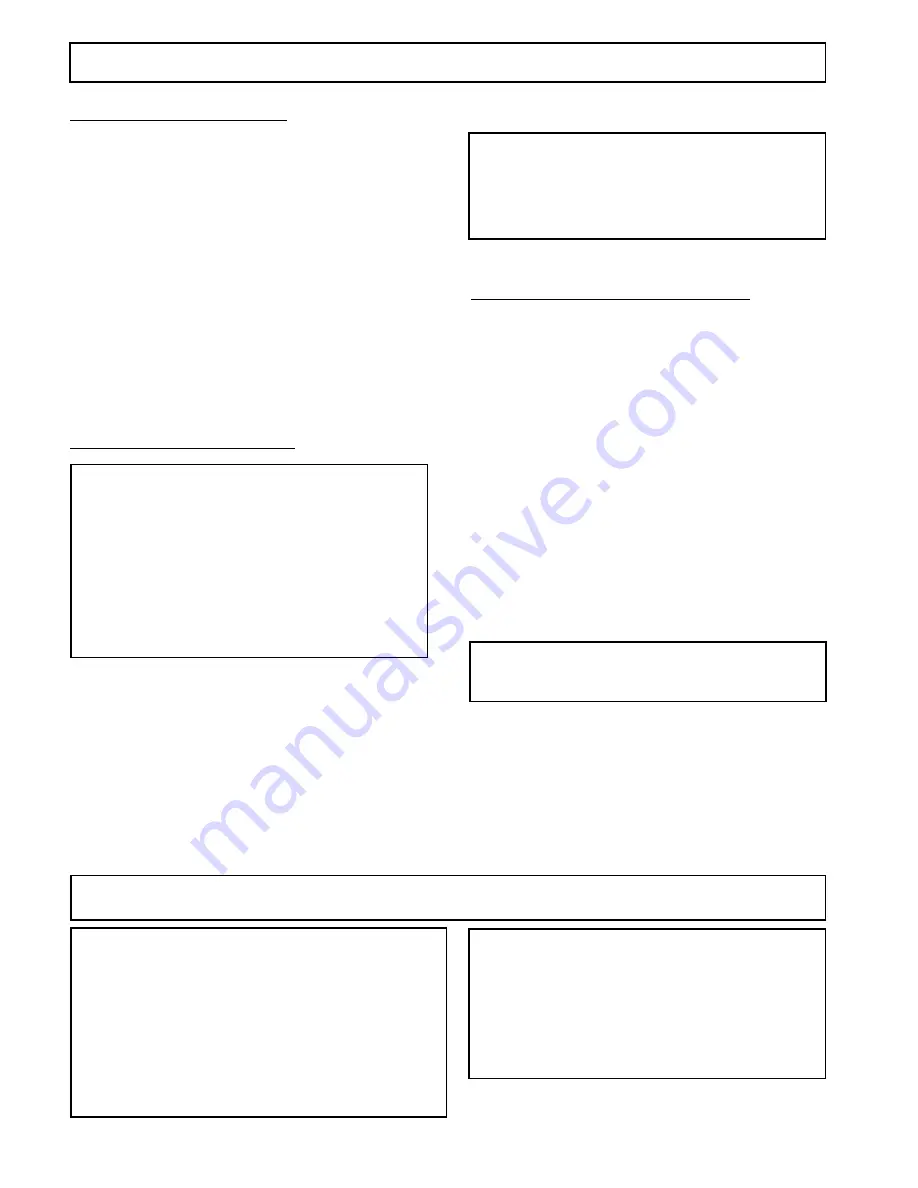
4
STARTING UP continued
WARNINGS
Note: United States Government safety stan-
dards have been adopted under the Occupational
Safety & Health Act. These standards, particularly
the General Standards, Part 1910 & Construction
Standards, Part 1926 should be consulted.
WARNINGS CONTINUED ON NEXT PAGE.......
DO NOT USE halogenated solvents in this sytem. The
prime valve and most airless guns have aluminum
parts and may explode. Cleaning agents, coatings,
paints or adhesives may contain halogenated
hydrocarbon solvents. DON'T TAKE CHANCES!
Consult your material suppliers to be sure. Some of the
most common of these solvents are:
Carbontetrachloride, Chlorobenzene, Dichloroethane,
Dichloroethyl Ether, Ethylbromide, Ethylchloride,
Tethrachloethane. Alternate valves and guns are
available if you need to use these solvents.
Every time you stop spraying, for even a minute,
lock the gun and submerge it into a small bucket
of thinner suitable for the material sprayed.
Thinner will dissolve the buildup of paint on the
outside of tip, tip guard and gun much more
effectively if the paint doesn't have time to dry
out completely.
There is an easy way to keep the outside of the tip
clean from material build up:
WARNING
- Follow the "Pressure Relief
Procedure" on page 6 .
To reduce the risk of injection, never hold your
hand, body, fingers or hand in a rag in front of
the spray tip when cleaning or checking for a
cleared tip. Always point the gun toward the
ground or into a waste container when checking
to see if the tip is cleared or when using a self-
cleaning tip.
4. Adjusting the Pressure
a. Turn the Pressure Control Knob CW to increase
pressure and CCW to decrease pressure.
b. Always use the lowest pressure necessary to
completely atomize the material being sprayed.
CAUTION - Operating the sprayer at higher pres-
sure than needed, wastes material, causes early
tip wear and shortens sprayer life.
c. If more coverage is needed use a larger tip rather
than increasing the pressure.
d. Check the spray pattern. The tip size and angle
determines the pattern width and flow rate.
5. Cleaning a Clogged Tip.
WARNING
- Clogged standard (flat) tip - clean
only after the tip is removed from the gun and
pressure has been relieved.
FOLLOW THE PRESSURE RELIEF
PROCEDURE WARNING ON PAGE 6.
6. When Shutting off the Sprayer
a. Whenever you stop spraying, even for a short
break, follow the "Pressure Relief Procedure Warning"
on page 6.
b. Clean the tip & gun as recommended on page 13.
c. Flush the sprayer at the end of each work day, if
the material you are spraying is water-based, or if it
could harden in the sprayer overnight. See "Flushing"
pages 1 and 2. Use a compatible solvent to flush,
then fill the pump and hoses with an oil based solvent
such as mineral spirits.
d. For long term shutdown or storage, refer to page 1.
WARNING
- Be sure to relieve pressure in
the pump after filling with mineral spirits.