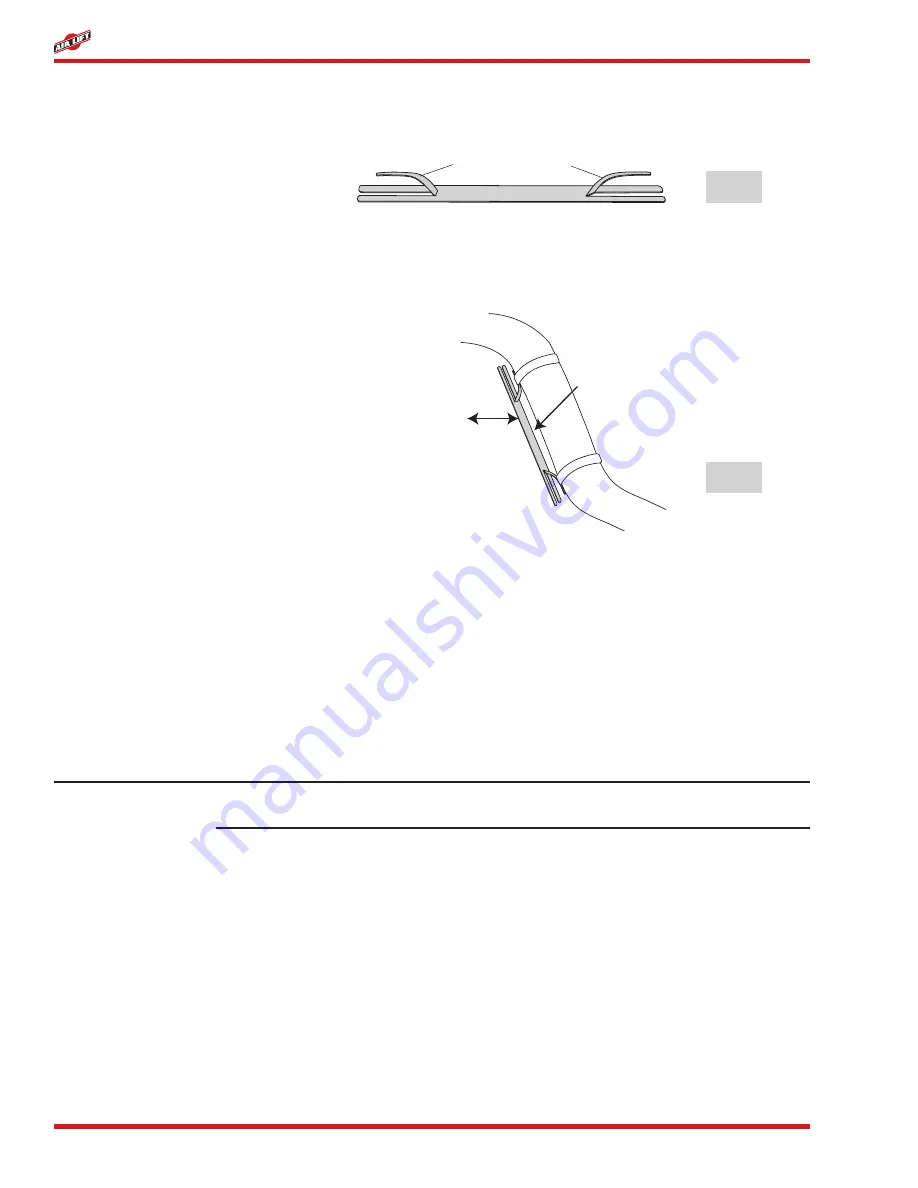
12
MN-831
LoadLifter 5000 Ultimate
INSTALLING THE HEAT SHIELD
1. Bend tabs to provide a 1/2” dead air space between exhaust pipe and heat shield (Figure
13).
NOTE
Bend Tabs Up
fig. 13
fig. 14
2. Attach the heat shield (Q) to the exhaust pipe using the clamps (R) (Figure 14). Bend
the heat shield for maximum clearance to the air spring.
Distance from Heat
Shield to Bellows
must be at least ½"
At least ½"
of dead air
space
3. On the driver side, it will be necessary to secure the emergency brake cable away from
the air spring to prevent it from rubbing. Use the provided tie straps (BB).
CHECKING FOR LEAKS
1. Inflate the air spring to 60 p.s.i.
2. Spray all connections and the inflation valves with a solution of 1/5 liquid dish soap
and 4/5 water to check for leaks. You should be able to spot leaks easily by looking for
bubbles in the soapy water.
3. After the test, deflate the springs to the minimum pressure required to restore the Normal
Ride Height, but not less than 5 p.s.i.
Check the air pressure again after 24 hours. A 2 to 4 p.s.i. loss after initial installation is
normal. Retest for leaks if the loss is more than 5 lbs.
FIXING LEAKS
1. If there is a problem with the swivel fitting, then:
a. Check the air line connection by deflating the spring and removing the line by pulling the
collar against the fitting and pulling firmly on the air line. Trim 1” off the end of the air
line. Be sure the cut is clean and square. Reinsert the air line into the push-to-connect
fitting.
b. Check the threaded connection by tightening the swivel fitting another 1/2 turn. If it
still leaks, deflate the air spring, remove the fitting, and re-coat the threads with thread
sealant. Reinstall by hand tightening as much as possible, then use a wrench for an
additional two turns.
2. If there is a problem with the inflation valve, then:
a. Check the valve core by tightening it with a valve core tool.