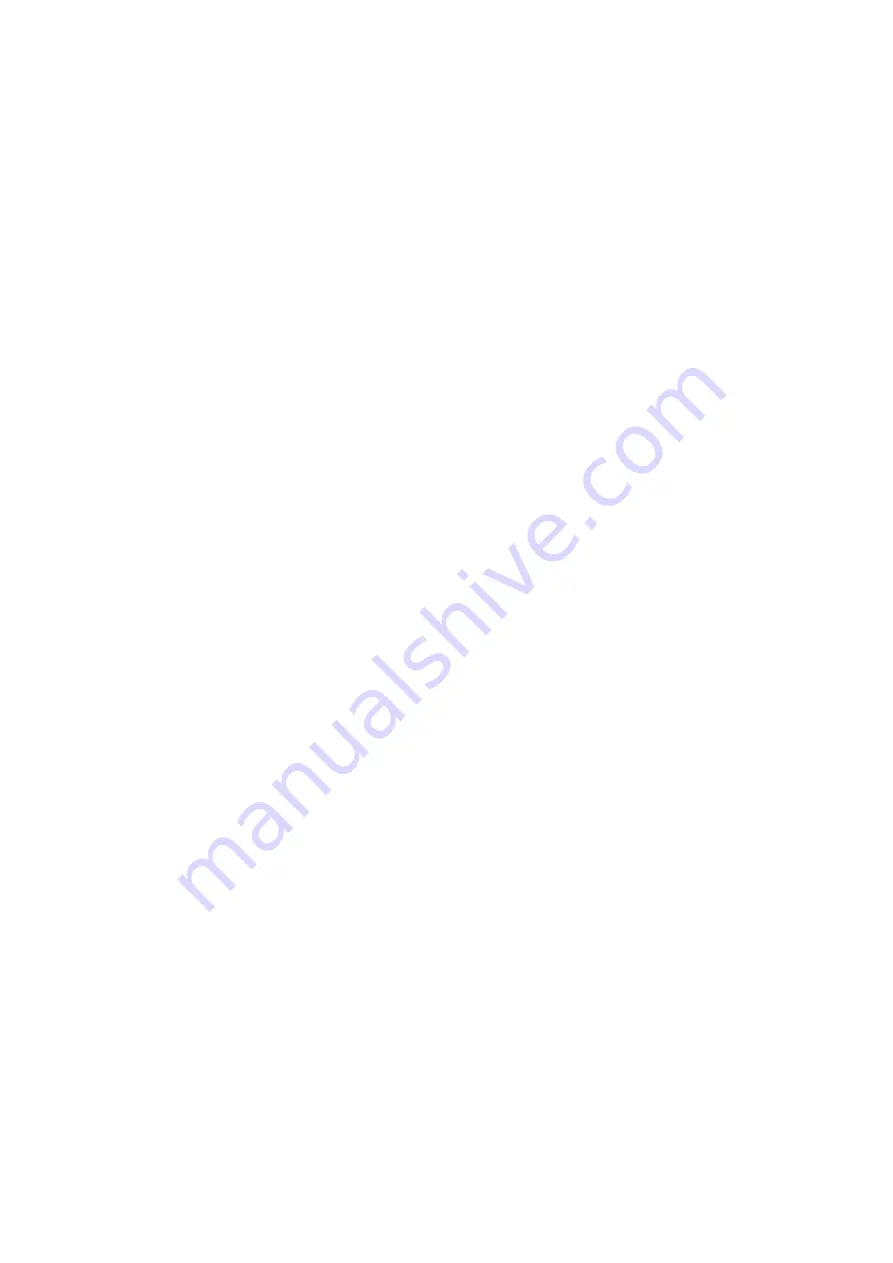
1100 Series Nano Pump Service Manual
29
Troubleshooting and Test Functions
2
Remote Time-out
A not-ready condition is still present on the remote input.
When an analysis is started, the system expects all not-ready conditions (e.g. a
not-ready condition during detector balance) to switch to run conditions
within one minute of starting the analysis. If a not-ready condition is still
present on the remote line after one minute the error message is generated.
Probable Causes
•
Not-ready condition in one of the instruments connected to the remote line.
•
Defective remote cable.
•
Defective components in the instrument showing the not-ready condition.
Suggested Actions
✔
Ensure the instrument showing the not-ready condition is installed
correctly, and is set up correctly for analysis.
✔
Exchange the remote cable.
✔
Check the instrument for defects (refer to the instrument’s reference
documentation).
Содержание 1100 Series
Страница 1: ...s1 Agilent 1100 Series Nano Pump Service Manual ...
Страница 4: ...iv 1100 Series Nano Pump Service Manual ...
Страница 12: ...xii 1100 Series Nano Pump Service Manual Agilent Technologies on Internet 269 Index 271 ...
Страница 32: ...20 1100 Series Nano Pump Service Manual 1 Installing the Pump ...
Страница 114: ...102 1100 Series Nano Pump Service Manual 2 Troubleshooting and Test Functions ...
Страница 174: ...162 1100 Series Nano Pump Service Manual 4 Parts and Materials Figure 27 Nano pump hydraulic path 1 9 3 6 5 8 7 10 4 2 ...
Страница 176: ...164 1100 Series Nano Pump Service Manual 4 Parts and Materials Figure 28 Pump Head Assembly 1 2 3 5 6 7 11 9 4 8 10 ...
Страница 204: ...192 1100 Series Nano Pump Service Manual 4 Parts and Materials ...
Страница 242: ...230 1100 Series Nano Pump Service Manual 5 Introduction to the Nano Pump ...
Страница 265: ...1100 Series Nano Pump Service Manual 253 Control Module Screens for the Nano Pump 6 ...
Страница 272: ...260 1100 Series Nano Pump Service Manual 7 Specifications ...
Страница 282: ...270 1100 Series Nano Pump Service Manual A Safety Information ...
Страница 287: ......