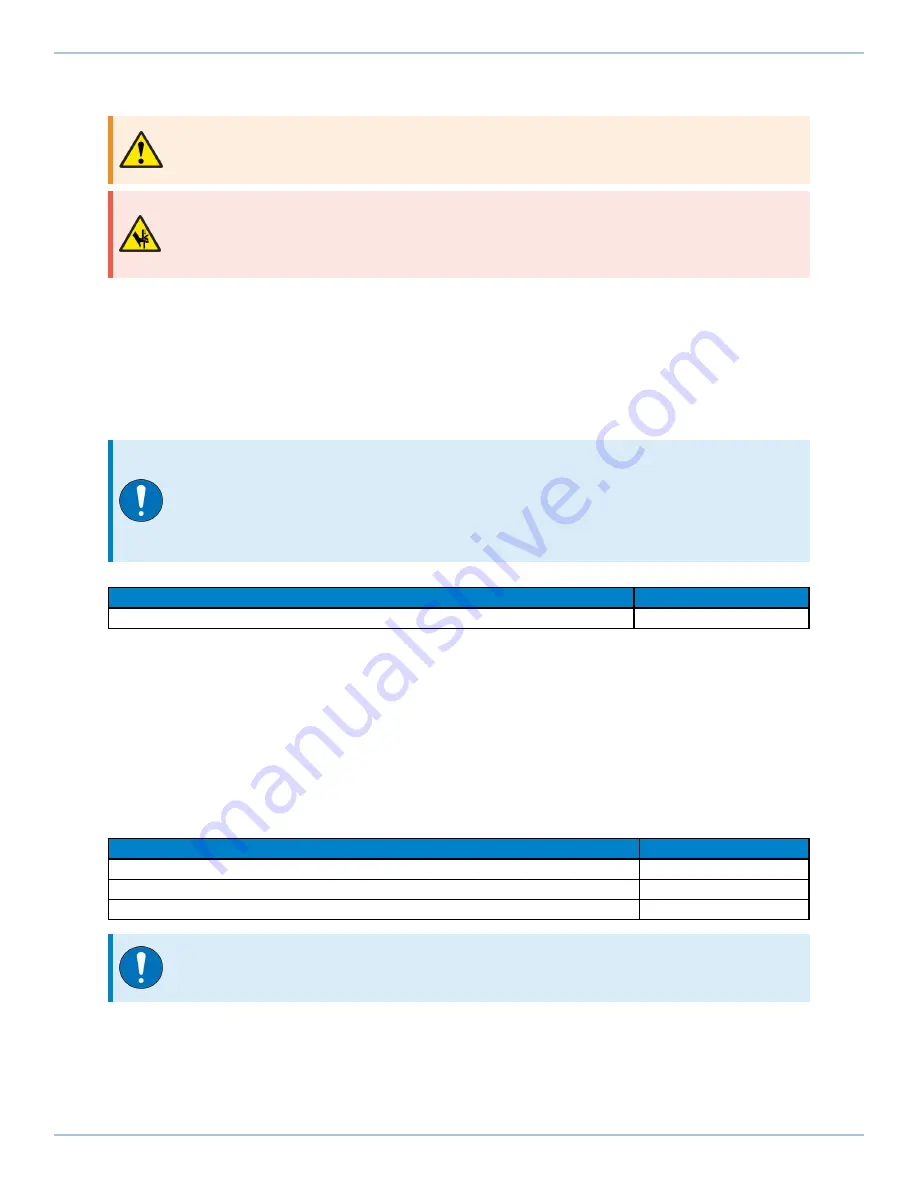
2.3. Securing the Stage to the Mounting Surface
WARNING
: The stage must be mounted securely. Improper mounting can result in
injury and damage to the equipment.
DANGER
:
PINCH POINT!
Keep Hands Clear while the stage is in motion. Make sure that
all moving parts are secure before you move the stage. Unsecured moving parts could
shift and cause injury or damage to the equipment.
The mounting surface must be flat and have adequate stiffness to achieve the maximum
performance from the stage. When it is mounted to a non-flat surface, the stage can be distorted
while the mounting screws are tightened. This distortion will decrease overall accuracy. Adjustments
to the mounting surface must be done before the stage is secured.
Inspect the mounting surface for dirt or unwanted residue and clean if necessary. Use precision
flatstones on the mounting surface to remove any burrs or high spots. Clean the mounting surface
with a lint-free cloth and acetone or isopropyl alcohol and allow the cleaning solvent to completely
dry. Gently place the stage on the mounting surface.
IMPORTANT
: The stage is precision machined and verified for flatness prior to product
assembly at the factory. If machining is required to achieve the desired flatness, it
should be performed on the mounting surface rather than the stage. Shimming should
be avoided if possible. If shimming is required, it should be minimized to retain
maximum rigidity of the system.
Table 2-1:
Stage Mounting Surface Flatness Requirement
Stage Travel
Flatness Requirement
All Travels
1 µm per 50 mm
Access the mounting holes in the base of the stage by sliding the carriage all the way to either end of
travel (shown in
).
Four additional mounting holes in the base of the stage are also available for customer use (refer to
for locations and
for mounting hardware information). For X-Y configurations,
mount the upper axis to the tabletop of the lower stage. A mounting plate is required if the upper
axis is an ANT95L-050.
Tightening torque values for the mounting hardware are dependent on the properties of the surface
to which the stage is being mounted. Values provided in
are typical values and may not be
accurate for your mounting surface. Refer to
for mounting locations and dimensions.
Table 2-2:
Stage to Mounting Surface Hardware
Mounting Hardware
Typical Screw Torque
M4 SHCS (stage mounting)
2.0 N·m [18 lb·in]
M5X0.8 (alternate mounting)
4.1 N·m [36 lb·in]
M6 or (1/4") SHCS ([-MP] option)
7.0 N·m [61 lb·in]
IMPORTANT
: 75 mm and 100 mm travel stages are only available for lower axis (X-axis)
configurations.
2.3. Securing the Stage to the Mounting Surface
ANT95L Hardware Manual
20
www.aerotech.com
Содержание ANT95L Series
Страница 1: ...Revision 2 00 ANT95L Series Single Axis Linear Direct Drive Nanopositioning Stage HARDWARE MANUAL...
Страница 6: ...This page intentionally left blank List of Tables ANT95L Hardware Manual 6 www aerotech com...
Страница 10: ...This page intentionally left blank EU Declaration of Incorporation ANT95L Hardware Manual 10 www aerotech com...
Страница 34: ...This page intentionally left blank 3 5 Motor and Feedback Phasing ANT95L Hardware Manual 34 www aerotech com...
Страница 42: ...This page intentionally left blank Appendix B Revision History ANT95L Hardware Manual 42 www aerotech com...