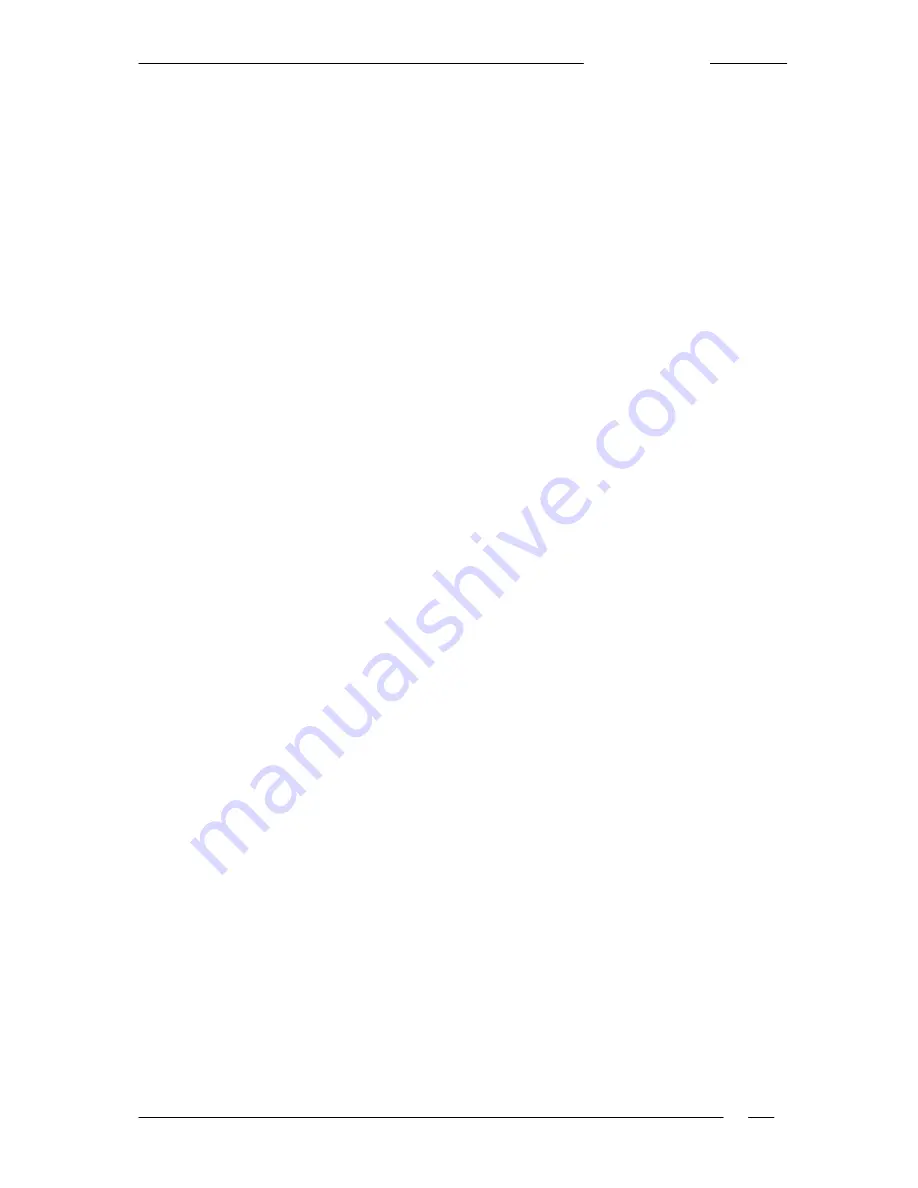
Xenon
Xenon building instructions
4
The next step is to install the screw guide support block and the actual screw guide (plastic tube),
to allow the tailplane to be screwed in place. Glue the tube to the balsa block using 5-minute
epoxy.
Glue this assembly in the fuselage, exactly vertical and exactly below the hole in the tailplane
saddle (fuselage). Now drill a hole in the bottom of the fuselage so that the retaining screw can be
passed through the guide.
The tailplane can now be screwed to the fuselage.
At this point attach the wing to the fuselage, and sight along the fuselage from the nose to check
whether the tailplane is exactly parallel to the wing. If not, carefully file away material from the
tailplane saddle to correct. Take great care here: the model’s flying characteristics depend to a
large extent on correct alignment of the flying surfaces.
The elevator servo should be glued to the servo well cover using 5-minute epoxy: roughen the
GRP surface thoroughly before applying glue, as the production process tends to leave traces of
mould release agent which could cause the glued joint to fail.
Extend the elevator servo lead with twisted cable so that it reaches the area under the wing,
where the receiver will be installed.
Assemble the elevator linkage as described for the ailerons and flaps; the system consists of a
horn, pre-formed wire pushrod, clevis and threaded coupler. Here again it is important that the
linkage hole in the horn is located exactly over the hinge pivot axis.
Finally fix the servo well cover to the fuselage using four self-tapping screws.
Rudder
The rudder is attached to the fin by means of two hinges; the hinge slots are already prepared.
Glue the hinges in place using 5-minute epoxy after applying a tiny drop of oil to the pivot pins to
prevent them becoming jammed.
The rudder servo is glued to the servo well cover using 5-minute epoxy, as described previously
for the elevator; roughen the GRP surface thoroughly before applying glue, as the production
process tends to leave traces of mould release agent which could cause the glued joint to fail.
Extend the rudder servo lead with twisted cable so that it reaches the area under the wing, where
the receiver will be installed.
Assemble the rudder linkage as described for the ailerons and flaps; the system consists of a
horn, pre-formed wire pushrod, clevis and threaded coupler. Once again it is important that the
linkage hole in the horn is located exactly over the hinge pivot axis.
Finally fix the servo well cover to the fuselage using four self-tapping screws.
Fuselage
The canopy is detachable, to ensure that the battery can be swapped easily during a flying ses-
sion.
Glue the GRP tongue to the inside of the canopy in such a way that it engages under the fuse-
lage flange. At the front end it is located by a steel pin glued into the canopy.
Alternatively you may prefer to attach the canopy using adhesive tape or two small self-tapping
screws.
Installing the electric motor
The first step is to glue the GRP motor bulkhead in the fuselage: press it firmly into position, tack it
in place with thin cyano, and then apply a fillet of 5-minute epoxy to secure it. The front face of the
fuselage defines the correct thrustline of the motor: the motor shaft should be inclined down by
about 2°, with a very little sidethrust (approx. 1° to the right, as seen from the tail).
Allow the glue to set hard, then slide the propeller / spinner onto the motor shaft. You may need to
sand back the front face of the fuselage until it matches the diameter of the spinner accurately,
and lines up correctly. Please work slowly and only remove material in small increments - your
reward will be a perfect result.
The motor can now be screwed to the bulkhead, and connected to the speed controller. Check the
motor’s direction of rotation at this point; in fact, it is best to check this before installing the motor.
A small block of wood with a central hole can be pushed onto the shaft to help you see its