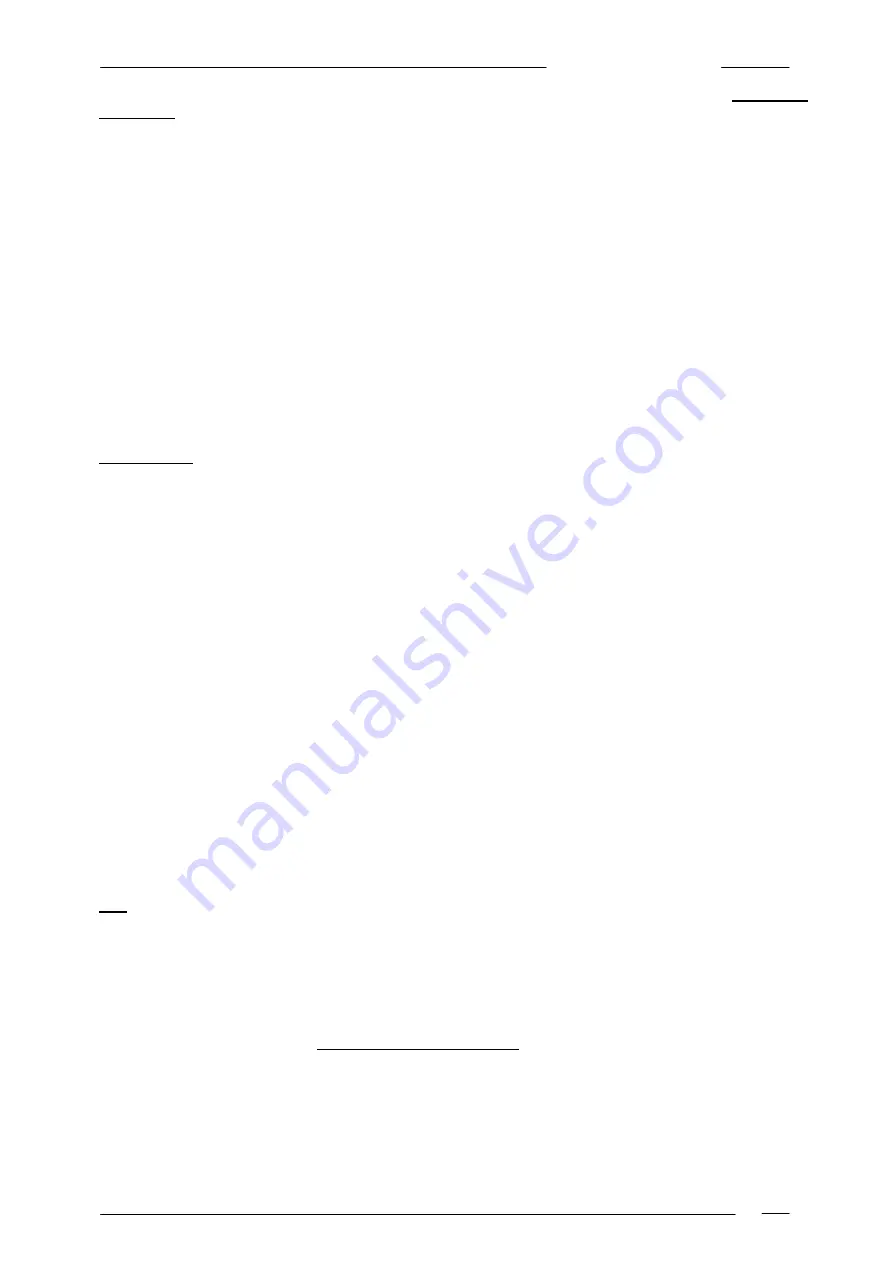
Canadair CL-415
6
and slip the snakes into place. Fit the steel pushrods (26) from the rear, and fit them in the appropriate
sleeve (25). Now slide the support plate (95) and snakes slowly into the fuselage, allowing the wires to
guide the snakes to and through the appropriate exit slots. Part (95) must be positioned carefully in the
fuselage to guarantee a smooth run of the sleeves (25). When you are sure this is the case, glue part (95)
in place with cyano, then reinforce the joints with epoxy.
Parts (25) should only be glued to part (95) (using thin cyano) once the snake inners (steel wire) have
been connected to the servos: see Figs. 14, 15. Install the receiver aerial sleeve as shown on the plan.
Cut out the battery supports (16) accurately and drill a series of 2 mm Ø holes in the side flanges as shown
in Fig. 16. Glue the reinforcements (18) to the inside of the rear support (16) using thin cyano. Bend the
retainer bars from aluminium strip and drill the 2 mm Ø holes as shown in Fig. 16. A single metal strap
should also be adequate if you prefer. The battery supports are not installed in the fuselage until a later
stage.
Carefully cut out the hatch cover (28) and trim it to fit. Caution: the front and rear faces are not the same!
Drill two 3 mm Ø holes in the support (31), stiffen the material with thin cyano and glue it to the fuselage
together with the hatch support (30). Insert the dowels, fill the space between the dowels and the hatch
cover (28) with a strip of scrap wood, and glue the parts together. Mark the position of the hatch latch (29),
cut the slot for the latch lever in the hatch cover, and tack part (29) in place with thin cyano.
Reinforce the joints with Stabilit-Express. Glue the second hatch support (30) in place and add 5 x 5 mm
balsa strips to stiffen the sides of the hatch cover - Fig. 17.
The tailplane
is assembled directly over the plan (building board). Pin down the trailing edge sheeting
(44), and fit all the ribs on the spars (40) and (41). Position the framework as accurately as you can on part
(44), then tack the spar (41) to the trailing edge sheet using thin cyano. Align the ribs carefully and glue
them to part (44) using thin cyano. Remove the structure from the building board. Now pin down the
leading edge sheeting (46) on the building board. Place the framework on the sheet panel, aligning the
main spar accurately, and tack it to part (46) using thin cyano. Now glue the ribs to the leading edge sheet
(46) one by one, again using thin cyano. Sand the underside of the false leading edge (45) to the angle
shown and glue it in place. Cut the centre section sheeting from part (51) and glue it to the framework.
The plan also shows the “scale” version of the tailplane. If you wish to build this, the half-ribs (43) must
also be installed; see section F-F.
The top trailing edge sheet (44) is applied using thickened resin in exactly the same manner as for the
wing, working directly over the building board. The torsion box must be exactly straight, as this guarantees
the symmetry of the tailplane when the top leading edge sheet panel (46) is attached. Fit the centre section
sheeting (51) and the capstrips (50), glue the leading edge (47) in place, and sand everything smooth
overall. Check that the tailplane is perfectly square when viewed from above.
At this stage the channel at the elevator separation line has to be marked out as accurately as possible;
take care not to cut into the spar (41): see sections G-G and H-H. Remove the sheeting over the hinge line
channel.
Glue the balsa tip blocks (48) to the tailplane and sand them to shape (Figs. 18 to 20). Mark the elevator
separation line accurately and separate the elevator panel from the tailplane. Sand back the excess rib
material neatly. The elevator panel can now be divided into two as shown. Glue the elevator lining strips
(49) in place, fit the root end-pieces (36) to complete and stiffen the elevators, then sand everything
smooth.
Mark the position of the horns on the elevators - note that the 3 mm Ø holes must be at an angle as shown
in section H-H. This is done by packing up the elevators on the drilling table, so that the angle of the horn
is the same on both sides. Strengthen the holes with thin cyano, then run the drill through the holes again.
Fin:
you have already trial-fitted this on the stub fin. Check the fit once more, and ensure that it stands
truly vertical (relative to the wing). Relieve the trailing edge as shown on the plan to simulate the scale trim
tab. As mentioned at the start of the building instructions, sand away as much of the gel-coat as possible
to save weight at the tail end. Cut the “snake” exit slots by drilling 2.2 mm Ø holes at an angle, and file
them out at the correct angle.
Drill a series of 2 mm Ø holes all round the inside of the marked tailplane opening on both sides of the fin,
taking great care to follow the marked airfoil as accurately as you can. The tailplane must be an easy
sliding fit in the slots. With the tailplane installed, place the fin on the fuselage and tape the parts together.
Fit the wing on the fuselage and check the longitudinal dihedral! Correct any deviation by sanding back the
trailing edge of the fin root.
The marked lines on the moulding show where the rudder has to be separated - including the hinge line
gap. This is best done using a small electric drill (e.g. Proxxon) and a thin disc cutter, although a stiff, fine-
tooth sawblade could also be used. The fin / rudder construction is drawn full-size on the plan.
Start by sanding back the edges of the glass moulding to a neat finish, and reinforce the joint between the
factory-fitted spar and the fin if required. Make an in-fill piece from part (36) for the horn and epoxy it in the
rudder as shown. Seal the open faces of the fin and rudder using scrap 2 mm balsa sheet.