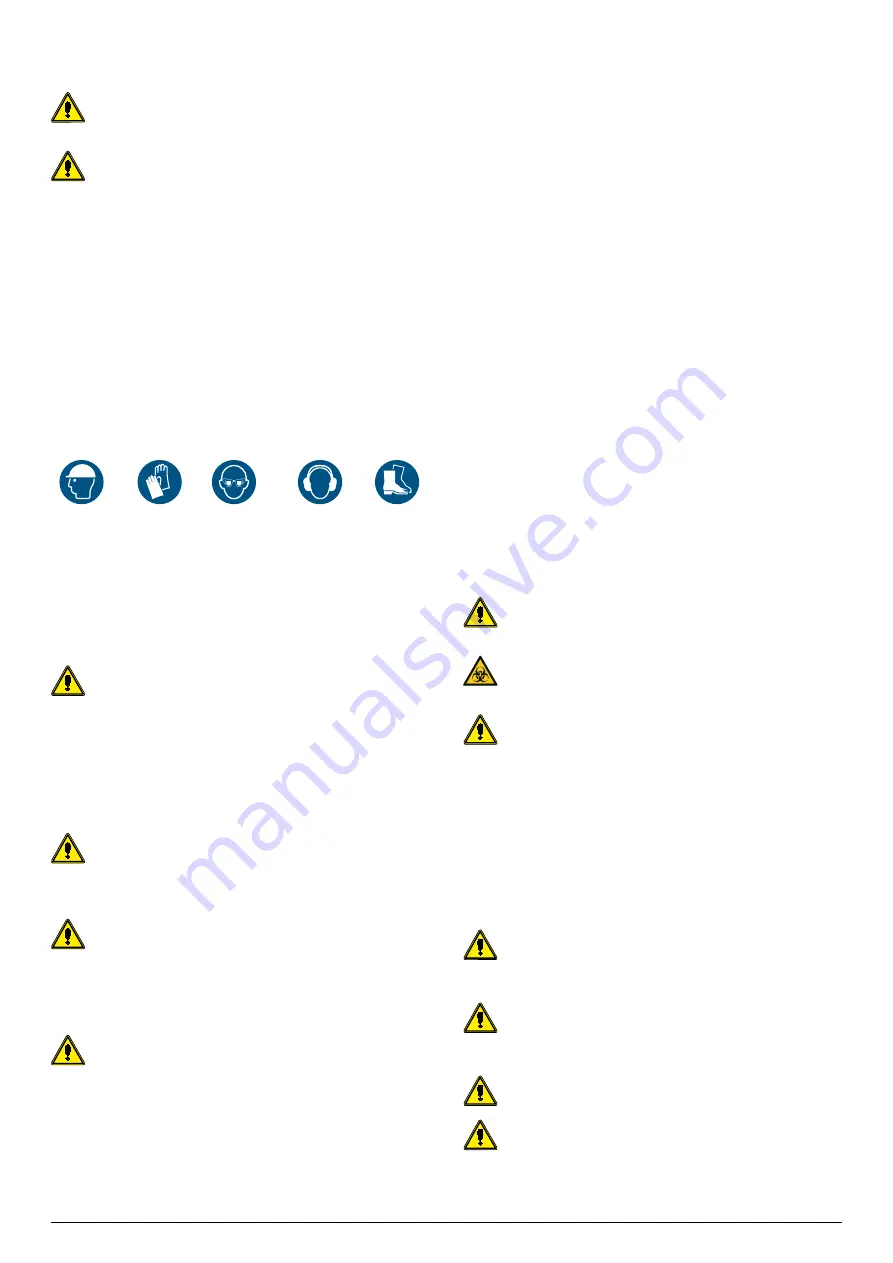
22.11 – 5806712_07
41
15 MAINTENANCE
NOTICE:
Aermec cannot be held responsible for any malfunction of the
units which are due to improper or missing maintenance.
Any cleaning, inspection, control or routine or extraordinary main-
tenance intervention:
must be carried out by expert technical personnel
who are authorised and qualified to perform the activities indicated above.
These activities must be carried out with the machine turned off and not
powered, and in a workmanlike manner according to what is required by
the national laws in force. When carrying out these activities, the machine
has the following risks:
— Risks of electric discharges;
— Risk of injuries due to the presence of rotating parts;
— Risk of injuries due to the presence of sharp edges and heavy weights;
— Risks of injuries due to the presence of components containing high pressure
gas;
— Risks of injuries due to high or low temperature components.
— Noise-related risks of the machine functioning (refer to what is declared in the
user manual);
— Risks related to the presence of harmful substances in hydronic circuits.
These activities must be carried out using personal protective equip-
ment suitable for the activities to carry out.
Maintenance operations are essential to maintain the refrigerant unit efficient, from
a purely functional point of view and with regard to energy and safety.
In the absence of specific regulations regarding HFC refrigerants, the manufacturer
prescribes the application of and compliance with that indicated in the:
1.
Regulation (EC) No.842/2006- art.3 concerning the "leakage containment";
2.
Regulation (EC) No.1516/2007 concerning the “standard leakage checking
requirements” and related national laws implementing the above European
regulations.
WARNING For the unit, the user must provide a system booklet which
he must ensure, or its designee authorised to service the machine,
will contain all required records in order to have a historical doc-
umentation of the unit functioning. The absence of records in the
booklet may count as evidence of lack of maintenance.
PRECAUTIONS AND PREVENTIVE MEASURES TO OBSERVE
DURING MAINTENANCE
WARNING Maintenance operations can only be performed by author-
ised technicians.
precautions against residual risks mechanical risks
WARNING The cooling circuit contains pressurised refrigerant gas:
— all operations must be performed by skilled personnel who have the legally re-
quired authorisations or qualifications.
— The cooling circuit contains under pressure refrigerant gas: any operation must
be performed by competent personnel in possession of the authorisations and
qualifications required by current laws
IT IS FORBIDDEN TO LOAD:
the cooling circuit with a refrigerant other
than the one indicated. Using a different refrigerant gas could seriously
damage the unit.
— Before opening a machine panel, ascertain whether it is or not firmly connected
to it by hinges;
— In case a piece is disassembled, make sure it is correctly reassembled before
restarting the unit;
— Louvers of the heat exchangers, edges of the components and panels, screws
can generate cuts;
— Do not remove the protections from mobile elements while the unit is running
— Make sure that the protections of mobile elements are correctly in place before
restarting the unit;
— It is not permitted to walk on the machine or to place other items on it;
— Fans, motors and belt drives may be in motion, always wait for them to stop and
take appropriate precautions to prevent their activation before accessing them;
— If the unit has components such as integrated inverters, disconnect the power
supply and wait at least 15 minutes before accessing it for maintenance opera-
tions: the internal components remain energised for this period, generating the
risk of electrocution;
— Isolate the unit from the mains by means of the external isolator provided for
the insertion of padlocks (up to 3) for blocking in "open" position;
— Place a sign reading "Do not turn on - maintenance in progress" on the open
isolator;
— Equip yourself with the appropriate personal protective equipment (helmet,
insulated gloves, protective goggles, accident-prevention shoes, etc.);
— Equip yourself with tools in good condition and make sure to have fully under-
stood the instructions before using them;
— For outdoor units, do not perform interventions in dangerous weather condi-
tions such as rain, snow, fog, etc.
— Never keep the cooling circuit open, because the oil absorbs humidity and de-
grades;
— Always use appropriate equipment (extractor, antistatic bracelet, etc.) when
replacing electronic boards;
— If replacing a motor, compressor, evaporator, condensing coils or any oth-
er heavy element, make sure that the lifting devices are compatible with the
weight to be handled;
— In air units with independent compressor compartment, do not access the fan
compartment without having first disconnected the machine through the iso-
lator on the board and having placed a sign reading "Do not turn on - mainte-
nance in progress";
— Contact the company if changes must be made to the refrigerant, hydraulic or
electric diagram of the unit, as well as its control logic.
Prevention of chemical / fire / environmental risks
WARNING Any intervention on the machine must be performed with
"NO SMOKING";
WARNING Never disperse the fluid contained in the cooling circuit in
the environment;
WARNING The water circuit may contain harmful substances. Prevent
the contents coming into contact with skin, eyes and clothing. Use
the prescribed personal protective equipment;
If there is a need to perform a braze-welding, so with the use of special torch with
naked flame, the same flame must only be activated if in the absence of freon gas in
the environment and on the cooling circuit pipes. Inside piping must be "washed"
and contain nitrogen type inert gas. The presence of flame and freon gas decom-
poses the same, forming lethal and carcinogenic compounds.
Hot works require the availability of a Carbon Dioxide (CO
2
) fire extinguisher. DO
NOT USE WATER, leachates could be hazardous for the discharges; if using water,
provide a containment tank.
Prevention against residual risks due to pressure or high/low temperature
WARNING The unit contains under pressure gas:
no operation must be
performed on under pressure equipment except during maintenance that
must be carried out by competent and authorised personnel.
WARNING Perform brazing or welding only on empty pipes and clear
of any lubricating oil residues; do not near flames or other heat sourc-
es to the pipes containing under pressure fluids;
WARNING Do not work with naked flames near the unit;
WARNING Do not bend or hit pipes containing under pressure fluids;