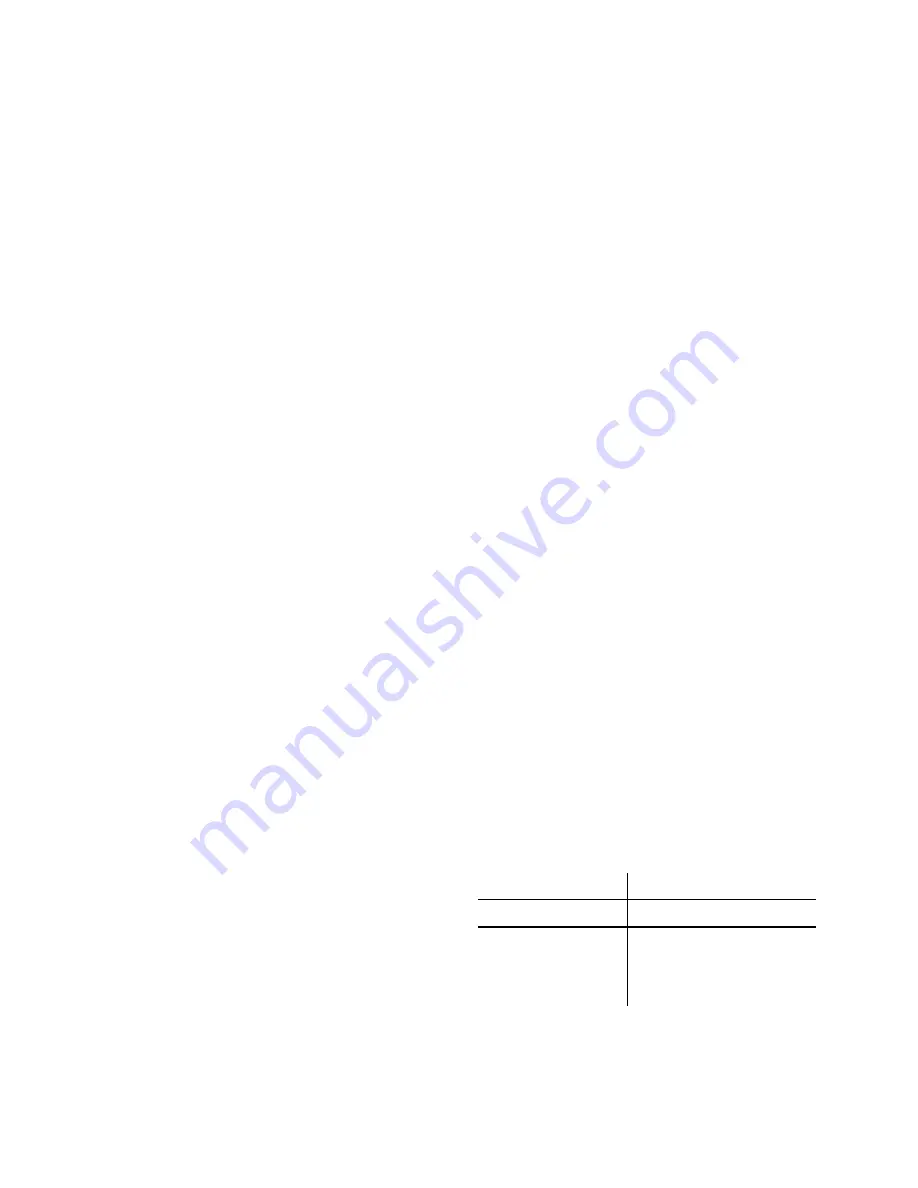
MODE OF OPERATION
If the Network setting is selected for RS485
Modbus operation, a valid Comm Address must
be entered in the Setup Menu. Refer to Modbus
Communication Manual GF-114 for additional
information.
While it is possible to change the settings of
temperature related functions, the unit is factory
preset with settings that work well in most
applications. It is suggested that an AERCO
representative be contacted, prior to changing
any temperature related function settings. For
descriptions of temperature-related functions
and their factory defaults, refer to Appendices A
and E.
5.4.1 Remote Setpoint Field Wiring
The only wiring connections necessary for the
Remote Setpoint mode are connection of the
remote signal leads from the source to the unit’s
I/O Box. The I/O Box is located on the front
panel of the boiler. For either a 4-20mA/0-5V or
a 0-20mA/0-5V setting, the connections are
made at the ANALOG IN terminals in the I/O
Box. For a Network setting, the connections are
made at the RS-485 COMM terminals in the I/O
Box. The signal must be floating, (ungrounded)
at the I/O Box and the wire used must be a two
wire shielded pair from 18 to 22 AWG. Polarity
must be observed. The source end of the shield
must be connected at the source. When driving
multiple units, each unit’s wiring must conform to
the above.
5.4.2 Remote Setpoint Startup
Since this mode of operation is factory preset
and the setpoint is being externally controlled,
no startup instructions are necessary
.
In this
mode, the
REMOTE
LED will light when the
external signal is present.
To operate the unit in the Manual mode, press
the
AUTO/MAN
switch. The
REMOTE
LED will
go off and the
MANUAL
LED will light.
To change back to the Remote Setpoint mode,
simply press the
AUTO/MAN
switch. The
REMOTE
LED will again light and the
MANUAL
LED will go off.
5.5 DIRECT DRIVE MODES
The unit’s air/fuel valve position (% open) can be
changed by a remote signal which is typically
sent from an Energy Management System
(EMS) or from a Building Automation System
(BAS). The Direct Drive mode can be driven by
a current or voltage signal within the following
ranges:
4-20 mA/1-5 Vdc
0-20 mA/0-5 Vdc
The factory default setting for the Direct Drive
mode is 4-20 mA/1-5 Vdc. With this setting, a 4
to 20 mA signal, sent by an EMS or BAS is used
to change the unit’s valve position from 0% to
100%. A 4 mA/1V signal is equal to a 0% valve
position, while a 20 mA /5V signal is equal to a
100% valve position. When a 0-20 mA/0-5 Vdc
signal is used, zero is equal to a 0% valve
position.
In addition to the current and voltage signals
described above, the Direct Drive mode can also
driven by a RS485 Modbus Network signal from
an EMS or BAS.
When in a Direct Drive mode, the unit is a slave
to the EMS or BAS and does not have a role in
temperature control. Direct Drive can be used to
drive single, or multiple units.
NOTE
If a voltage, rather than current signal is
used to control the remote setpoint, a DIP
switch adjustment must be made on the
CPU Board located in the Control Box
Assembly. Contact your local AERCO
representative for details.
To enable the Direct Drive Mode, the following
menu setting must be made in the Configuration
Menu:
MENU OPTION
SETTING
Boiler Mode
Direct Drive
Remote Signal
4-20mA/1-5V,
0-20mA/0-5V, or
Network
Refer to paragraph 3.3 for instructions on
changing menu options.
5-3
Содержание Benchmark 2.0
Страница 4: ......
Страница 8: ......
Страница 12: ......
Страница 24: ......
Страница 44: ......
Страница 50: ......
Страница 78: ......
Страница 84: ......
Страница 88: ......
Страница 90: ......
Страница 101: ...APPENDIX F F 5 ...
Страница 102: ...APPENDIX F F 6 ...
Страница 104: ...APPENDIX F F 8 ...
Страница 105: ...APPENDIX F F 9 ...
Страница 106: ...APPENDIX F F 10 ...
Страница 107: ...APPENDIX F F 11 ...
Страница 108: ...APPENDIX F F 12 ...
Страница 112: ...APPENDIX G G 4 ...
Страница 113: ...APPENDIX H H 1 ...
Страница 114: ...APPENDIX H H 2 ...
Страница 115: ...APPENDIX H H 3 ...
Страница 118: ......
Страница 119: ...APPENDIX J BENCHMARK CONTROL PANEL EXPLODED VIEW J 1 ...
Страница 120: ...APPENDIX J J 2 P1 P2 P3 P4 P5 P6 BENCHMARK CONTROL PANEL REAR VIEW ...
Страница 122: ......