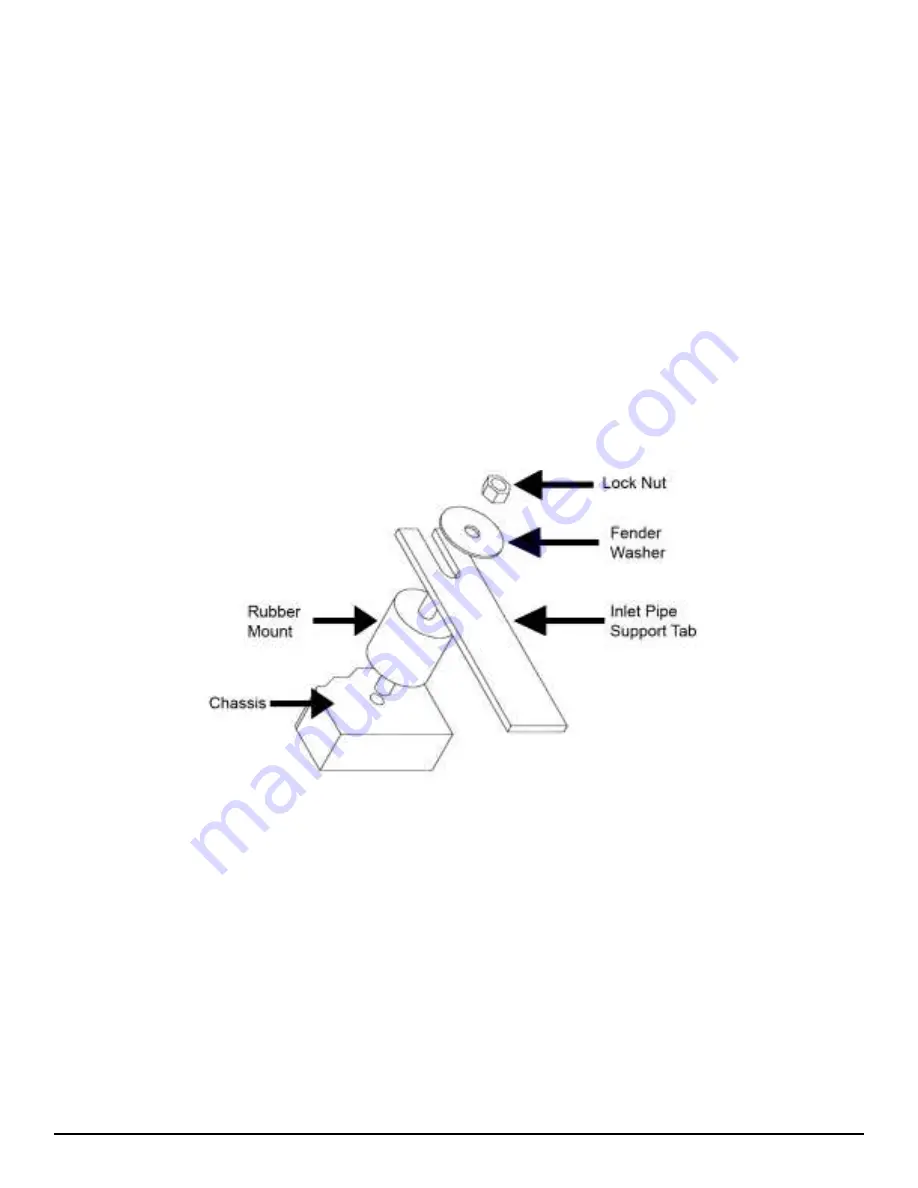
4
• To contstuct a working prototype of the intake system, it is best to cut the tubing to
an approximate size leaving a little extra at the ends of the bends. Use the couplers
to connect the pipes. For the blade style MAF sensor, use double sided foam tape to
attach the MAF pad to the pipe so that it can be easily relocated if the fuel trims are
unacceptable. Once the configuration of the system is complete, and the fuel trims
are acceptable, the mounting bracket can be mounted, and if applicable the MAF pad
can be welded to the inlet tube.
• With the AEM universal intake we provide two couplers AEM-5-438 for installation
using a tubular MAF sensor. We also Provide a weld on aluminum MAF pad for the
blade style MAF sensor.
• The routing of the inlet system must be clear of any moving engine component.
Additionally, before making the inlet tract permanent, Perform an “engine rock “ test
to ensure there is no contact with the body or chassis when the engine torques over
when under load. This check is done by starting the engine and putting it in gear
WITH THE PARKING BRAKE ON AND THE BRAKES APPLIED. Raise the engine speed in
forward and then reverse gear to 2000 RPM and having someone observe there is no
contact with any part of the vehicle including hoses or wiring of any kind.
• The location of the mounting bracket used to stabilize the inlet duct should be placed
as close to the filter end of the intake tube as possible to minimize the moment load
at the weld attachment point on the duct.
• There is a rubber soft mount included with the kit to isolate the movement of the
intake tube from the body of the vehicle. This mount MUST be used to ensure the
mount bracket does not crack.