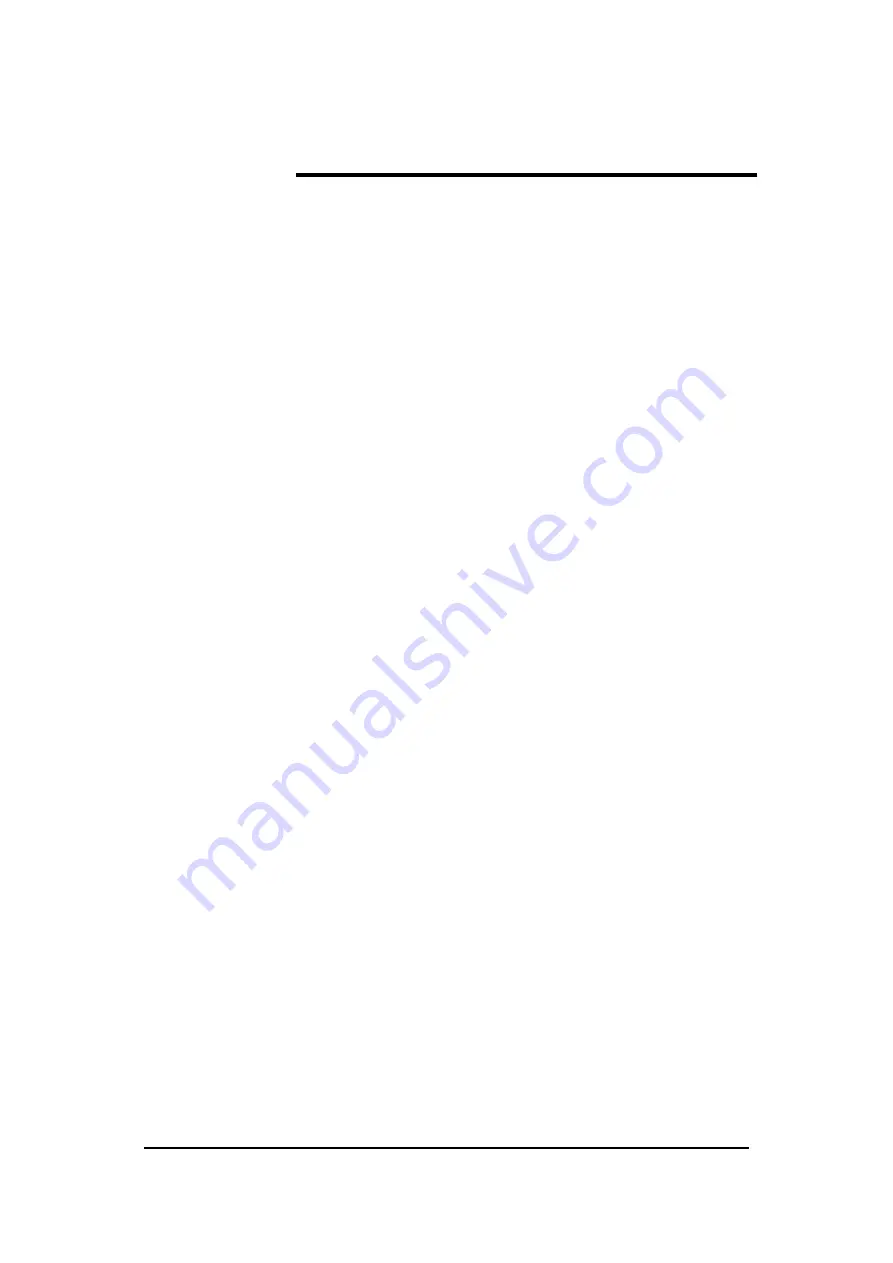
Preface
Dear User
Welcome to the growing group
of Beta Major Users. The product you
have purchased has been carefully designed and manufactured to ensure
that you, the user, will gain the maximum benefit.
All Adkins products
are specifically designed to ensure ease of use
with particular attention to safety requirements.
Should you discover any fault
or damage upon receipt of this product,
you should immediately contact your supplier.