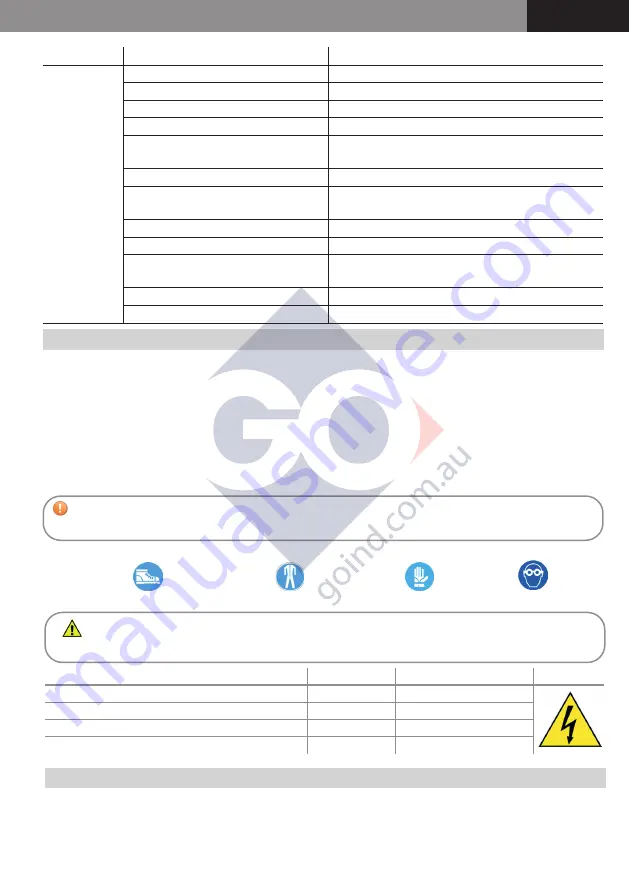
EN
8 - MAINTENANCE
Maintenance includes inspections, checks and interventions which, to prevent interruptions and breakdowns,
systematically keep the machine lubrication status and the parts subject to wear under control. These operations,
although simple, must be carried out by Qualified Personnel.
The machine is designed to minimise routine
maintenance. It is the operator’s responsibility to assess the status and its suitability for use. We recommend
stopping the operations and performing maintenance every time operation is not perfect. This will always allow
maximum efficiency.
PROBLEM POSSIBLE CAUSE
CORRECTIVE ACTION
LOW OR NO
FLOW RATE
Low level of liquid in the tank
Fill the tank
Filter dirty or clogged
Clean or replace the filter
Foot valve dirty or clogged
Clean or replace the foot valve
Pipe or dispensing nozzle damaged
Replace the damaged components
Excessive negative pressure to the
suction line
Make sure there are no leaks or restrictions on the
suction part (recommended pipes chap. 5.2)
High pressure drops in the circuit
Change the hydraulic discharge configuration
Bypass valve open or blocked
Check the condition of the valve and clean or replace it
if necessary
Vanes blocked
Check and clean the vanes and their housings
Excessive wear of the vanes or impeller Replace the worn components
Leaks from the gaskets
Make sure the gaskets are properly tightened and not
worn
Incorrect power supply voltage
Power the pump as specified on the rating plate
Defective motor
Contact the dealer (fault code M2)
9 - DEMOLITION AND DISPOSAL
If the electric pump is to be scrapped, its parts are to be given to companies specialised in disposing of and recycling industrial
waste, as shown on the table below:
CAUTION! Make sure the pump is disconnected from the power supply and is not in ope-
ration before carrying out any maintenance.
Safety footwear
Protective clothing
Protective gloves
Safety goggles
Always use the appropriate PPE (Personal Protective Equipment):
WARNING! Failure to comply with these requirements will release the manufacturer from any liabi
-
lity resulting from the effects of the Warranty.
MAINTENANCE
FREQUENCY MACHINE STATUS
SYMBOL
Make sure the pipes and couplings are properly connected Every month
Isolation for Maintenance purposes
Check/clean pipes and fittings
Every 12 months
Isolation for Maintenance purposes
Check/clean filter and fittings
Every month
Isolation for Maintenance purposes
Check/clean pump body
Every month
Isolation for Maintenance purposes