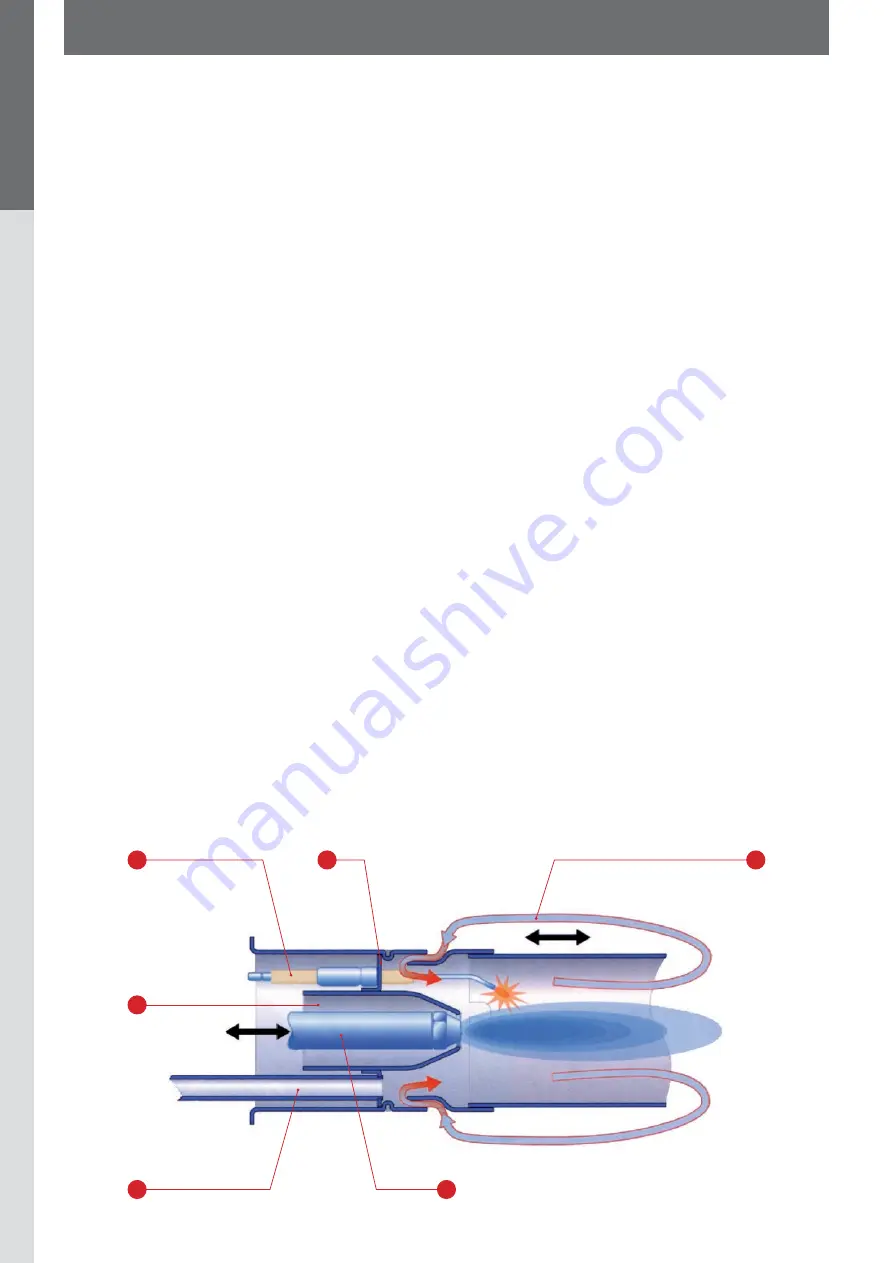
EN • 4
ENGLISH
FRANCAIS
NEDERLANDS
ES
p
A
ño
L
IT
ALIAN
o
DE
u
TSCH
662Y0500 • B
geneRal
energy SaVing
By purchasing this burner, you will be able to make significant
savings in terms of costs, oil and above all, energy!
we recommend that the heating system is regularly inspected
and serviced by a qualified heating engineer in accordance with
DIN 4755.
An indication of the combustion quality and oil consumption can be
obtained by checking the exhaust gas temperature and the burner
running times.
the mixing unit and recirculation
principle
A. Air
B. Ignition electrode
C. Gasket
D. Recirculation
E. Oil
F. Inspection glass for flame detector
the flame makeS the difference
Thanks to many years’ experience of developing blue burners,
we have been able to develop a product that not only meets, but
far exceeds the sophisticated requirements of modern heating
technology. In the design and development phase we took an
innovative route; by combining a new housing with a high-powered
fan which creates a pressure of 9 - 16 mbar behind the nozzle,
we have managed to develop a highly efficient oil gasification
system. This system provides a totally blue flame and an optimum
soot-free burn, whilst running extremely quietly and is a further
step towards green technology.
• Exhaust gas temperature
The exhaust gas temperature is measured using a thermometer
which can be purchased from a specialist shop. The chimney
sweep’s inspection hole is the ideal measuring point. If the exhaust
gas temperature appears to increase by more than 30°C, it
must be assumed that a coating has formed in the combustion
chamber, which will cause the heating system to run inefficiently.
If this occurs, clean the boiler and check the burner immediately.
when comparing with reference measurements, make sure that
the burner running times are the same.
• Operating hours meter
An operating hours meter which records the opening time
of the solenoid valve can be used to monitor oil consumption.
The system is connected to the electrical supply via the B4
terminal of the connection plug.
when comparing with reference measurements, allow for the
respective outside temperature of the year in question.
• Flue gas shut-off valve
Flue gas shut-off valves are occasionally used to prevent excess
cooling during shut-down. when the system is fully shut down,
condensation can form in the boiler and the chimney due to
the interrupted air flow. In addition, hot boiler components may
reflect back onto the nozzle (carbonization). However, the use
of a draught limiter or secondary air device can prevent the
satisfactory ventilation of the chimney and excessive cooling of
the boiler.
F
D
B
C
A
E