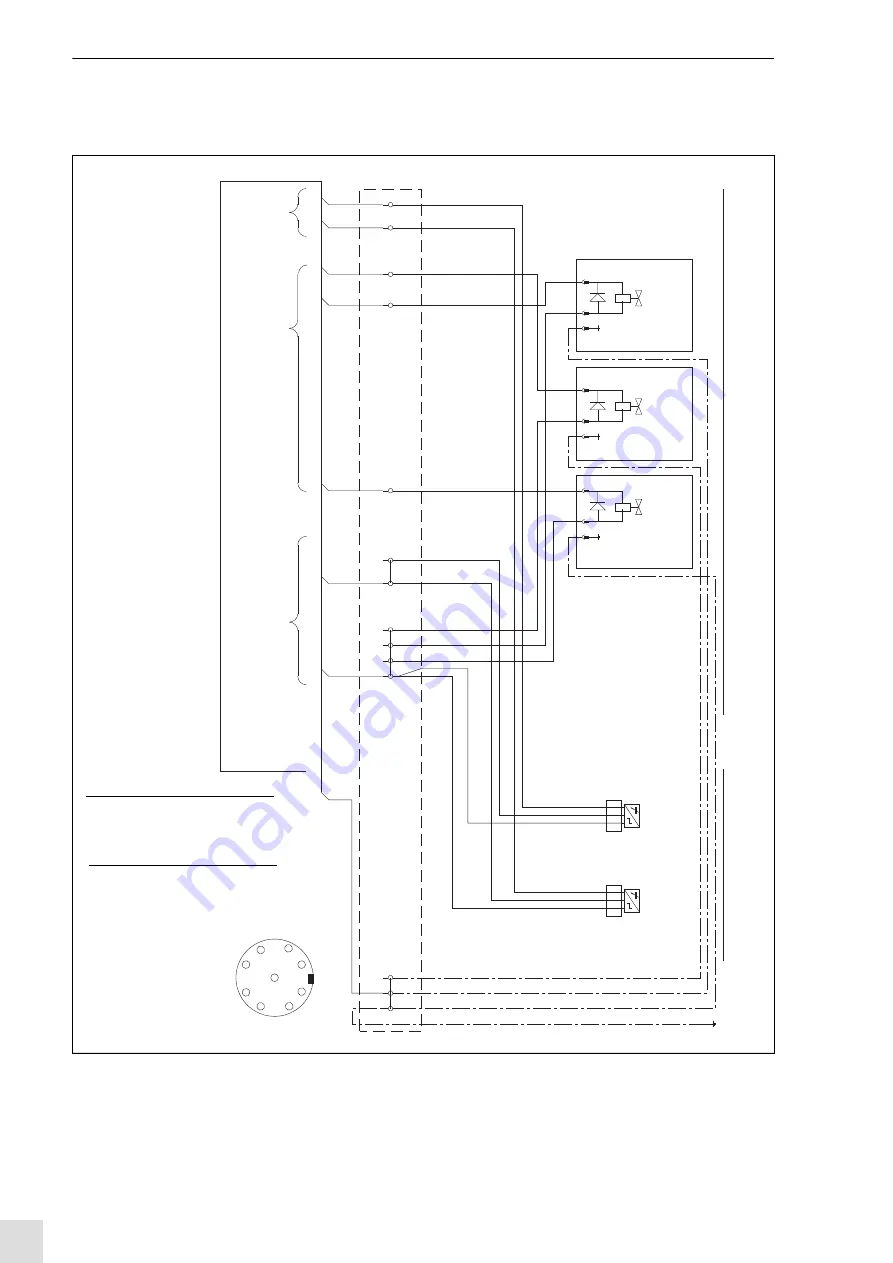
DE - 24
6 Inbetriebnahme
TCS-Compact
6.4 Elektroanschluss herstellen
Abb. 20
Schaltplan
Spannungsv
er
sor
gung
GND
2
4VDC
Ventilspulen
Näher
ungsschalter
Schalter
ausgänge
-X1.13
-X1.14
-X1.12
-X1.11
-X1.10
BK
BK
BN
BN
BN
Spannzylinder offen (S2)
Hub ist unten (S1)
Motor Rotation
Hub oben (Y1)
Spannen/Schere
-X1.9
-X1.8
BN
BN
-X1.7
-X1.6
-X1.5
-X1.4
BU
BU
BU
GND
Klemmleis
te X1
-X1.3 PE
-X1.2 PE
-X1.1 PE
-S2
Spannzylinder
of
fen
Hubzylinder
unten
-S1
PE1
Sensor
en
Aktor
en
Spannen/
Dr
ahtscher
e
Hub oben
Motor R
o
tation
PE
BU
BN
-D
A2
-Y
3
A1
-Y
2
-Y
1
-D
A1
A2
BN
BU
PE
BN
BU
-D
PE
A2
A1
Gerätestecker
8 Spannzylinder
7 Hub unten 24VDC/max.100mA
6 Motor-Rotation (Y2) 24VDC/2,8W
5 Hub hoch (Y1) 24VDC/2,8W
4 Spannen /
3 24 VDC/200 mA
2 GND
1 PE
1
2
3
4
5
6
7
8
9 n.c.
1
2
3
4
5
6
7
8
9
(Y2)
(Y3)
Schere ein (Y3) 24VDC/2,8W
offen 24VDC/max.100mA
Ausgang
Eingang
Betriebs-
spannung
Achtung 2 V
er
sionen sind möglic
h:
1) PNP-
Ausgang: Sour
ce-V
a
riante
2) NPN-
Ausgang: Sink
-V
ar
iante
Sensor
en
ve
rsion: siehe T
ypensc
hild
Polar
ität der F
reilaufdioden im
Magnetv
entils
tec
ker beac
hten,
ggf. änder
n
Содержание TCS-Compact
Страница 62: ...EN 32 13 Notizen Notes TCS Compact 13 Notizen Notes ...
Страница 63: ...TCS Compact 13 Notizen Notes EN 33 ...