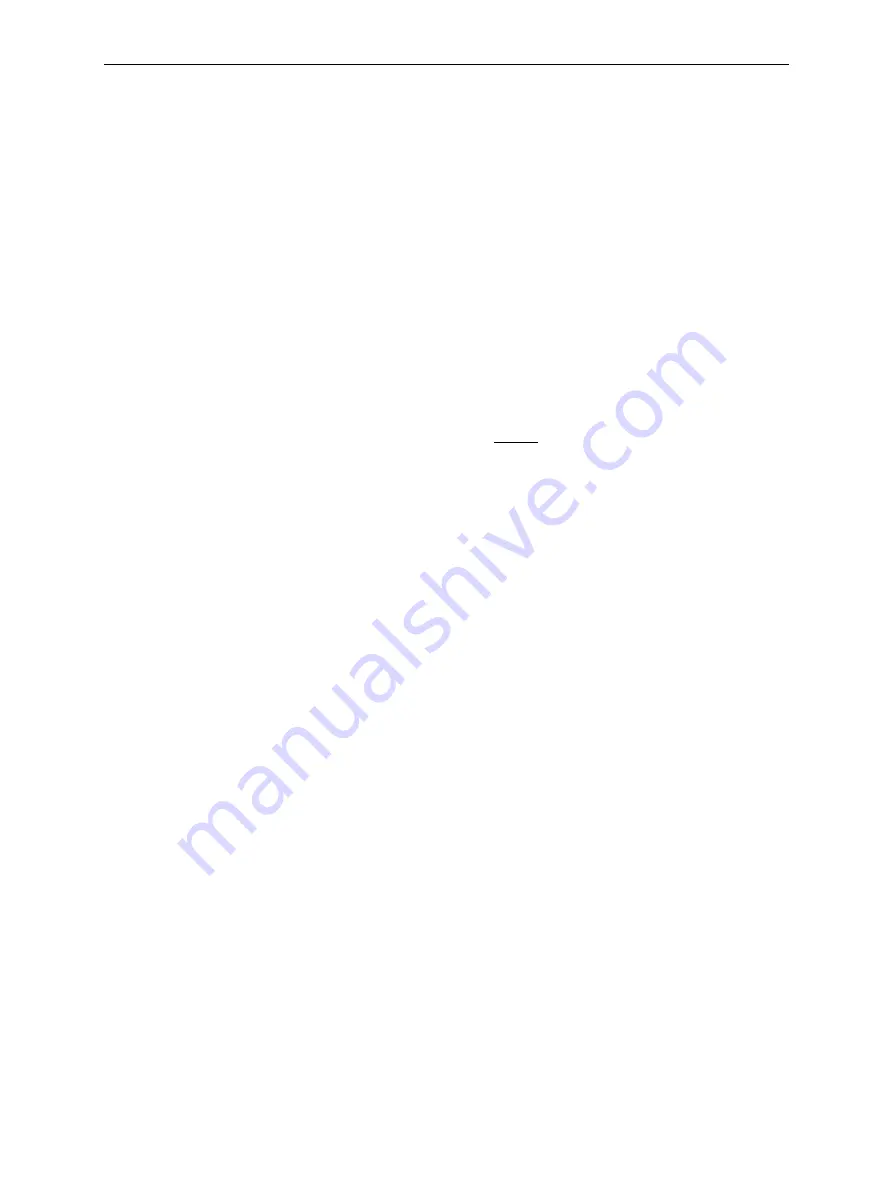
23
Replace Pressure Rollers and Springs
Shut down the sample gas feed unit:
1
Stop the sample gas supply and shut off the sample gas feed unit power
supply.
Remove the hose:
2
Disconnect the external hoses from the hose connections.
3
Using the handles, press the moving belt
1
together and turn the S-clip
2
as
far as its limit stop. Remove the moving belt with hose from the pump head.
Dismantle the pump head:
4
Unscrew the two screws
3
that secure the pump head.
5
Pull the pump head
4
off the roller mounting axle, and remove the roller
mounting
5
from the pump head.
Replace pressure rollers and springs:
6
Press the pressure springs
6
slightly together and pull them out of the hole in
the roller mounting
5
and out of the retaining slot in the roller axle
7
.
Remove the roller axle from the roller mounting, and pull the pressure roller
8
off the roller axle.
7
Before reassembling the hose pump, check all the parts for dirt and, if
necessary, clean them with a dry cloth or oil-free compressed air. Do not use
solvents for cleaning as they can attack the plastic parts.
8
Push the new pressure roller
8
onto the roller axle
7
and secure with new
pressure springs
6
in the roller mounting
5
.
Fit the pump head:
9
Insert the roller mounting
5
in the pump head
4
, and push both components
together onto the roller mounting axle.
During this process, check to ensure that the roller mounting axle and roller
mounting fit together properly and that the flange on the rotating axis points
towards the pump head front.
10
Secure the pump head
4
with the two screws
3
.
Refit the hose:
11
Insert moving belt
1
with the hose in the dovetail guides in the pump head.
Using the handles, press the moving belt together while at the same time
turning the S-clip
2
until it engages.
12
Connect the external hoses to the hose connections.
Restart the sample gas feed unit:
13
Switch on power supply to the sample gas feed unit.
14
The sample gas flow should only be restarted after the lead time period.
Содержание SCC-S
Страница 1: ...SCC S Sample gas feed unit Operator s Manual 42 23 59 EN Rev 1 ...
Страница 35: ...35 Circuit Diagrams SCC S Sample Gas Feed Unit without Peltier Cooler ...
Страница 36: ...36 SCC S Sample Gas Feed Unit with Peltier Cooler ...
Страница 37: ...37 SCC S Sample Gas Feed Unit 24 VDC Power Supply and Solenoid Valves ...
Страница 39: ......