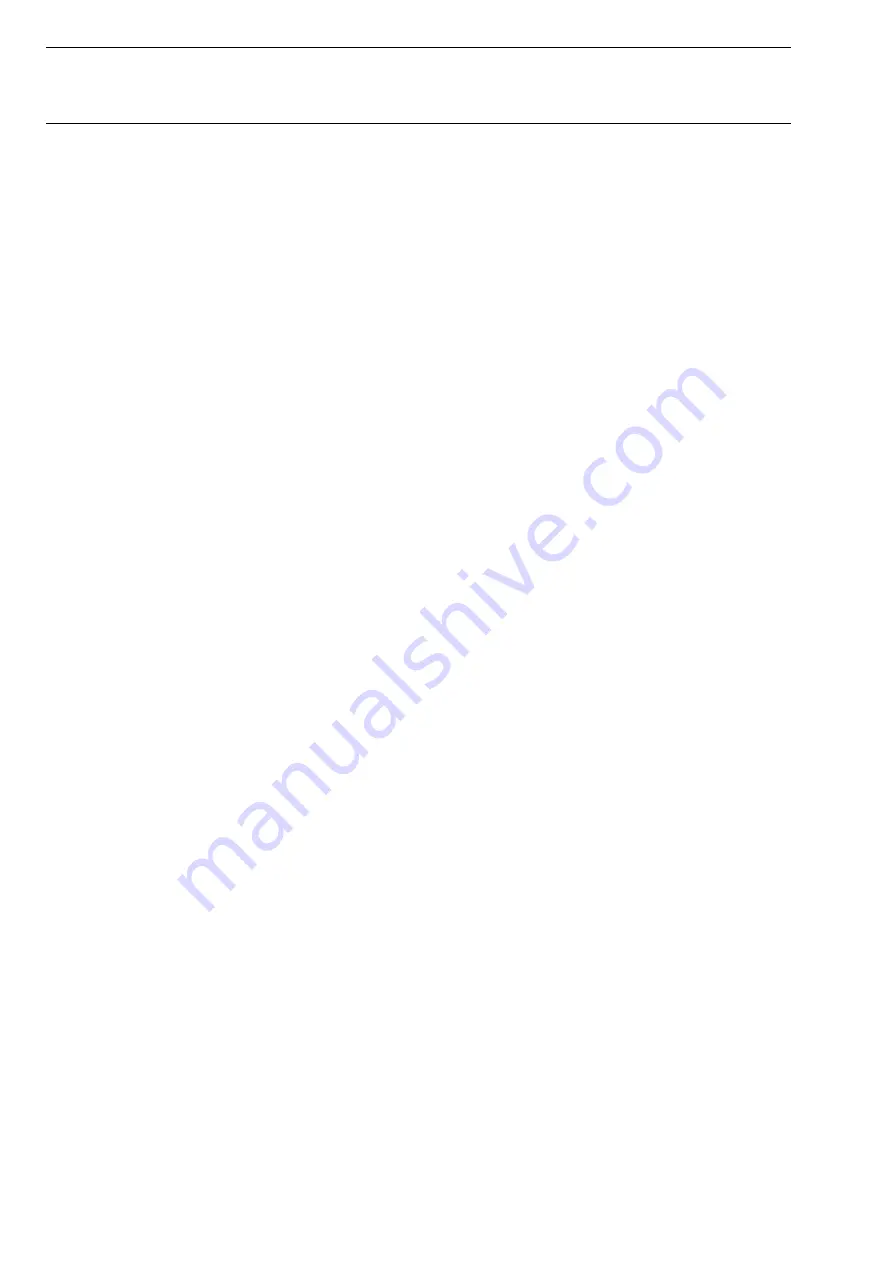
1MRK 502 001-UEN
Page 8
RARIC
Shaft current protection
Remove the protection from the transport case and make a visual inspec-
tion for transport damages. Check that all screws are firmly tightened and
all relay elements are securely fastened.
Check on the rating plate of the relay units that the delivered relay has cor-
rect data as regards auxiliary voltage, frequency etc. Check against the list
of apparatus that all units are included.
If the relay is to be stored before installation this must be done in a dry and
dust-free place, preferably in the original transport case.
The RARIC protection can be placed in a 19" equipment frame for mount-
ing in a 19" rack in a cubicle. The relay can also be placed in a relay case
type RHGX.
On delivery, all internal connections in the protection are ready made.
External connections (dotted lines on the circuit diagrams) are made with
leads with 20 A COMBIFLEX sockets to the RTXP 18 test switch and
with 10 A sockets to the relay terminal bases.
The ILDD shaft current transformer should be mounted around the shaft at
a place where any possible current through the bearing is flowing in the
shaft. This means that it should be mounted at the rotor side of any bearing
or slip-ring. To avoid disturbances the transformer shall be mounted on the
turbine side of the machine which is free from field bars and at maximum
distance from the end of the stator winding. See Fig. 12 and Fig. 13 for
recommended mounting.
Screened cable, with twisted pairs and with the screen grounded only at
the relay side is recommended for the connections between the protection
and the shaft current transformer.
An inner diameter of the transformer 20 - 50 mm larger than the shaft
diameter is suitably selected. Large diameter of the transformer has a neg-
ative influence on the sensitivity of the protection and it also increases the
risk of stray fluxes entering the CT core.
The width of the transformer in axial direction is 38 mm for inner diame-
ters up to 2 000 mm and 42 mm for inner diameters above 2 000 mm.
An axial distance of at least 250 mm is required for assembling the trans-
former sections on the shaft.
Mounting details are not included in the delivery, since they must be
designed to suit the specific machine. Examples on mounting supports,
which can be used in most cases, are showned in Fig. 14.
4 RECEIVING, STORAGE AND INSTALLATION
4.1 Receiving
4.2 Storage
4.3 Installation