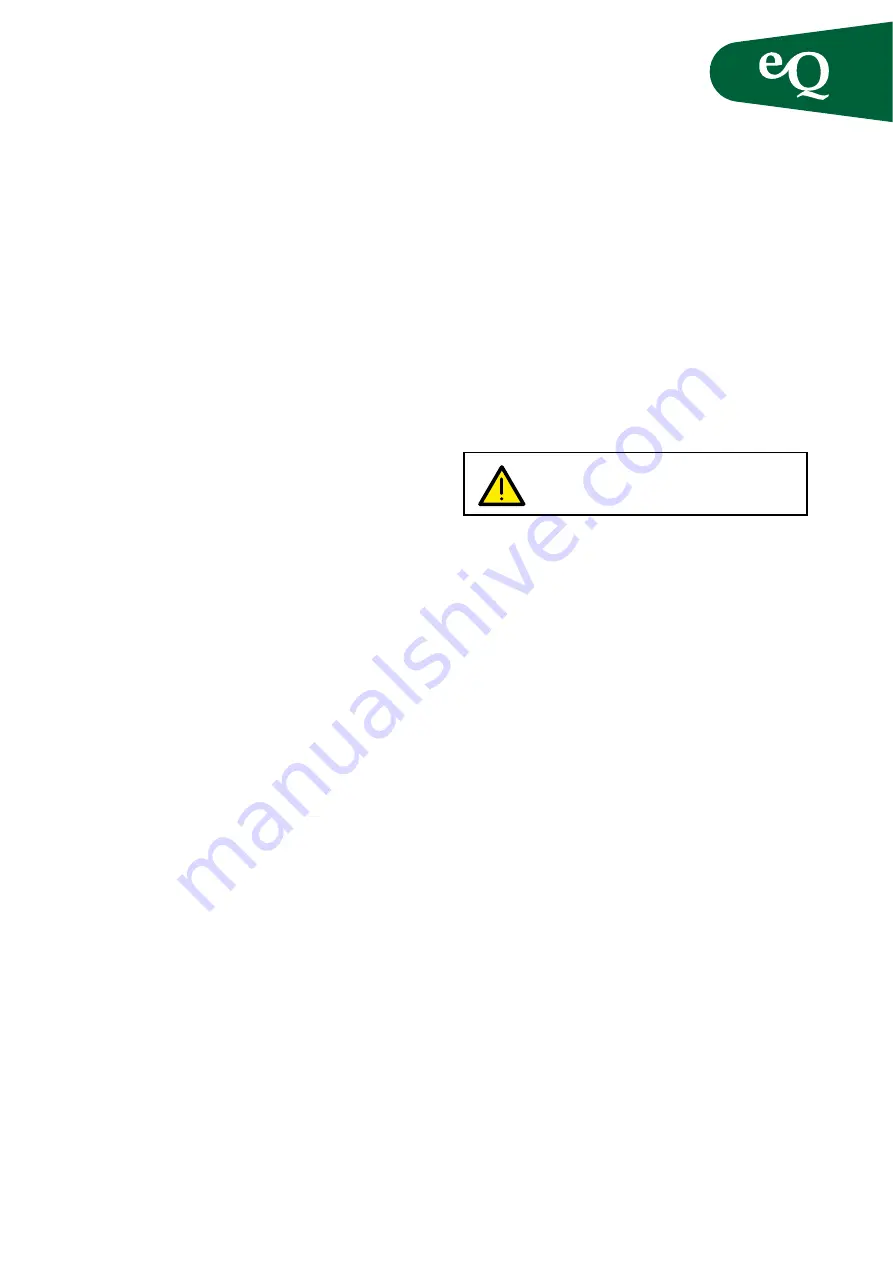
Fläkt Woods
8265 GB 2011.10
4
Specifications are subject to alteration without notice
Installation and maintenance instruction
Fläkt Woods three phase asyncronous motor
Manufacturer: ABB
Fitting coupling halves and pulleys
Coupling halves and pulleys must be fitted using suitable
equipment and tools that do not damage the bearings.
Never fit a coupling half or pulley by hammering into
place or remove it using a lever pressed against the body
of the machine.
Mounting accuracy of coupling half :
check that the clearance b is less than 0,05 mm and that the
difference a1 to a2 is also less than 0,05 mm. See figure 3.
Balancing
The rotor of the machine is dynamically balanced.
As standard, balancing has been carried out using
half
key,
and the shaft is marked
with a RED tape,
with the
text “Balanced with half key”.
To avoid vibration the coupling-half or pulley must be
balanced with half key after the keyway has been
machined.
In the event of balancing with full key the shaft is
marked
with a YELLOW tape,
with the text “Balanced
with full key”.
To avoid vibration the coupling-half or pulley must be
balanced without a key after the keyway has been
machined.
In case balancing
without key,
the shaft is marked
with
a BLUE tape,
with the text “Balanced without key”.
Maintenance and lubrication
General inspection
- Inspect the machine at regular intervals.
- Keep the machine clean and ensure free ventilation
airflow.
- Check the condition of shaft seals (eg V-ring) and
replace if necessary.
- Check the condition of connections and mounting and
assembly bolts.
- Check the bearing condition by listening for unusual
noise, vibration measurement, bearing temperature,
inspection of spent grease or SPM bearing monitoring.
* When changes of condition occur, dismantle the machine,
check the parts and replace if necessary.
Lubrication
Machines with permanently greased bearings
Machines up to frame size 180 are normally fitted with
permanently greased bearings of either Z or 2Z types.
Bearing types are specified in the respective product cata-
logues and on the rating plate of each motor from size 112
and larger.
WARNING!
Beware of all rotating parts!
As a quide, adequate lubrication can be achieved for the
following duration, according to L1 at ambient tempera-
ture of 25 ° C.
32 000 - 45 000 duty hours for 4 pole machines.1)
16 000 - 26 000 duty hours for 2 and 2/4 pole
machines.
1)
The shorter times apply to larger frame sizes.
1)
Depending on application and load conditions, see
applicable product catalogue.
Hours of operation for vertical motors are half of the
above values.
Machines with relubrication system
Relubrication procedure:
- Remove grease outlet plug if fitted.
- Press fresh grease into the bearing until all old grease
has been forced out
- Let the motor run 1-2 hours to ensure that all excess
grease is forced out of the bearing. Close the grease
outlet plug if fitted.
Regrease motors while running. If this is not possible,
lubrication can be carried out while the machine is at a
standstill. In this case, use only half the quantity of grease,
then run the motor for a few minutes at full speed. When
the motor has stopped, the remaining quantity of grease
can be forced in until the old grease has been replaced.
After 1-2 running hours close the grease outlet plug (if
fitted).
The grease outlet plug must be removed permanently
with automatic lubrication.
If the machine is fitted with a lubrication information
plate, follow the values given, otherwise use the values
in table, page 5.
ABB Motors policy is to have reliability as a vital issue in
bearing lubrication intervals. That is why we follow the
L1-principle (meaning that 99 % of the motors are sure
to make the interval time). According to L1 policy the
lubrication intervals are as follows: