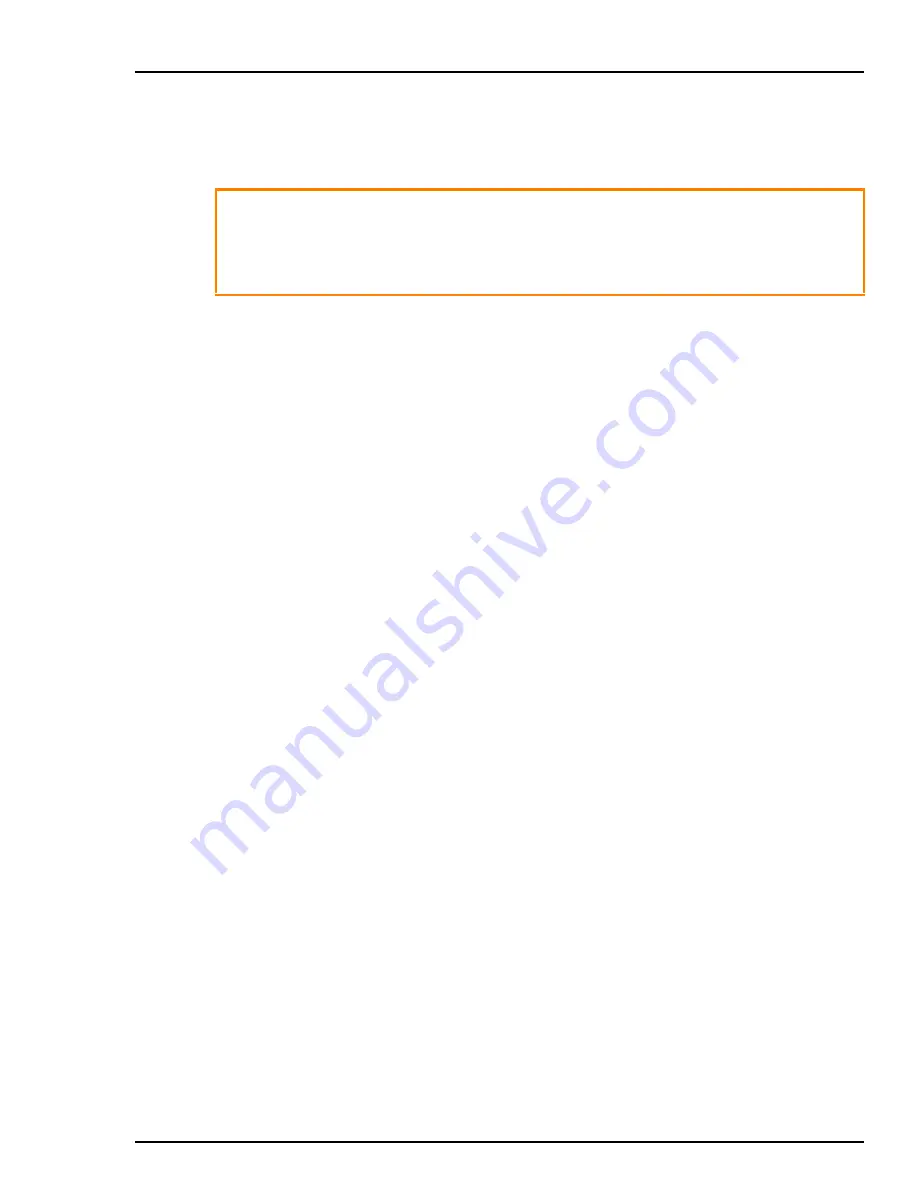
POSITION TRANSMITTERS
CALIBRATION
A
-
7
3. Insert ohmmeter leads into test jacks TP1 and TP2. If the resis-
tance value is between 940 and 1060 ohms, remove the ohmmeter
leads and proceed to Step 4. Otherwise continue with Step 3.
a. Remove the cam, by removing the screw, flag, nut, and
washer (Fig.
b. Loosen the set screw on the hub of the small gear using a
-inch Allen wrench (Fig.
c. Use a screwdriver to adjust the shaft on the potentiometer
until the ohmmeter reads 1000,
±
10 ohms. While adjusting the
resistance, hold the gears and cam shaft stationary so rotation
does not occur. Only the potentiometer shaft should move while
adjusting the resistance.
NOTE:
If the mesh between the large and small gears is not tight,
adjust the position of the potentiometer mounting bracket (Fig.
so that backlash is eliminated.
d. Tighten the set screw on the small gear hub.
e. Remove the ohmmeter from TB1-1 and TB1-2. Install the
cam, screw, flag, nut, and washer (Fig.
).
4. Place the CAL/OPER jumpers into the operate (OPER) position
(Fig.
). If a direct-acting cam is being used, place the FOR/REV
jumpers in the FOR position. For a reverse action cam, place these
jumpers in the REV position (Fig.
).
5. Move the actuator to the 0% position. Insert ammeter leads into
TP2(+) and TP1(-). If the position of the cam limits access to TP1,
connect the (-) lead of the meter to TB1-2 on the terminal block.
6. Adjust the ZERO potentiometer to 4.00 mA. See Figure
the location of the zero potentiometer.
7. Move the actuator to the 100% position. Adjust the SPAN potenti-
ometer to 20.00 mA. See Figure
potentiometer.
8. Repeat Steps 6 and 7 until the indicated current readings are
obtained.
WARNING
The pneumatic supply pressure must be turned off before
removing the positioning cam. The final control element will go
to one end of the stroke and can cause a process upset. Some
process upsets may cause damage to equipment and endan-
ger personnel.
1 16
⁄