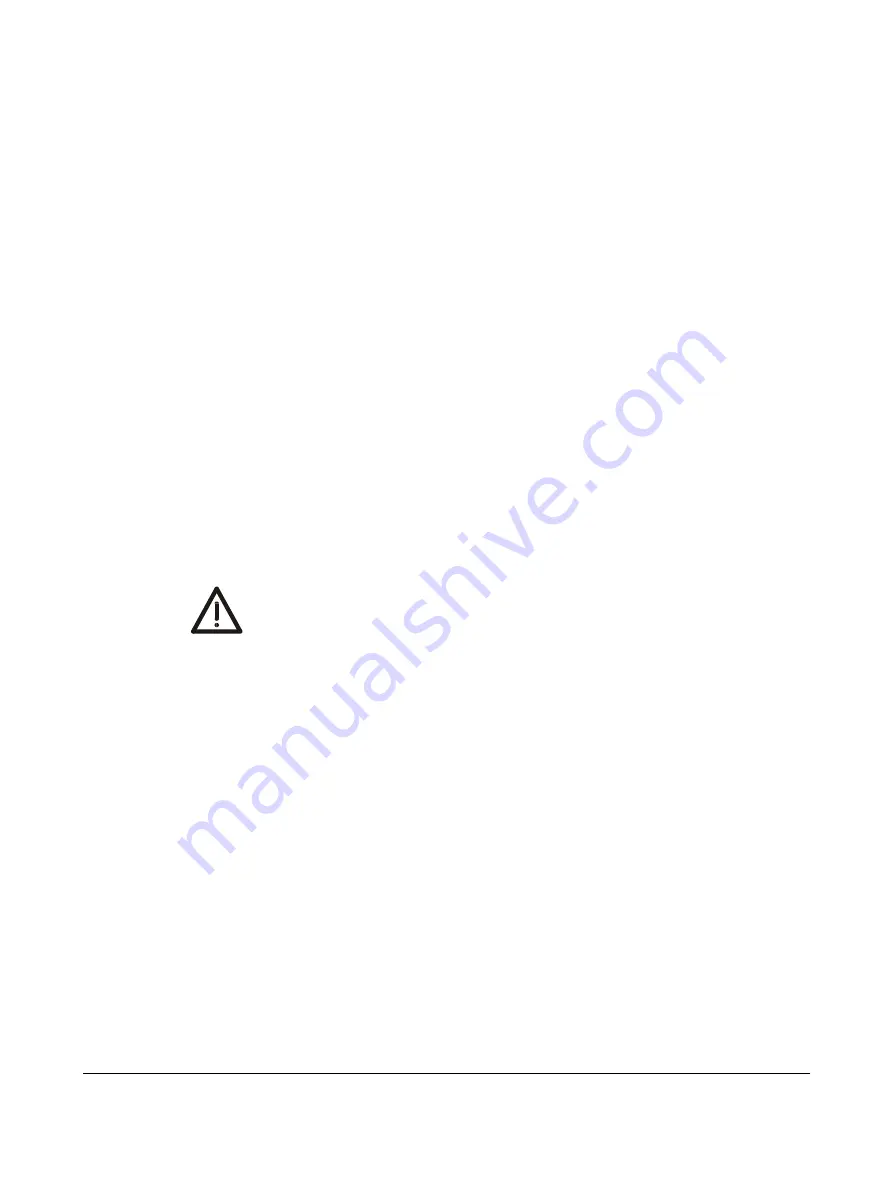
CI/ACX-EN Rev. D
ACX Analyzer System Commissioning Instruction
19
Back-Purging Unit: Installation Site and Air Supply Requirements
Design of the
Back-Purging Unit
The back-purging unit consists of a protective cabinet with shut-off valve, 6 bar
pressure reduction valve, solenoid valves for back-purging, pressure regulator and 5 l
compressed air receiver for effective pressure pulses also with lower airflow rate.
Distance to
Sampling Probe
The distance between the back-purging unit and the sampling probe must not exceed
5 m (length of the steel-braided compressed-air hoses = 6 m).
Protection from
Adverse Conditions
Protect the back-purging unit against
•
Water spray
•
Contact with chemicals
•
Strong sunlight and heat radiation
•
Strong air currents
•
Heavy dust load
•
Corrosive atmospheres
•
Vibration
Pressurized air supply
requirements
•
dry (dew point < 3 °C), oil- and dust-free
•
max. 6 bar for back-purging
•
approx. 4 bar as control air (needed for 2-stage back-purging with Type PFE2 filter
unit and AO2000-Fidas24 VOC analyzer)
•
Required air capacity approx. 100 m3/h
•
Instrument air following ISO 8573-1 Class 2 (particle size max. 1 µm, particle density
max. 1 mg/m3, oil content max. 0.1 mg/m3, pressure dew point max. –20 °C)
CAUTION!
If the compressed air is not dry and clean, this will result in damage to the sample
conditioning components (valves, filters, sample gas cooler, sample gas feed unit) as
well as to the gas analyzer.