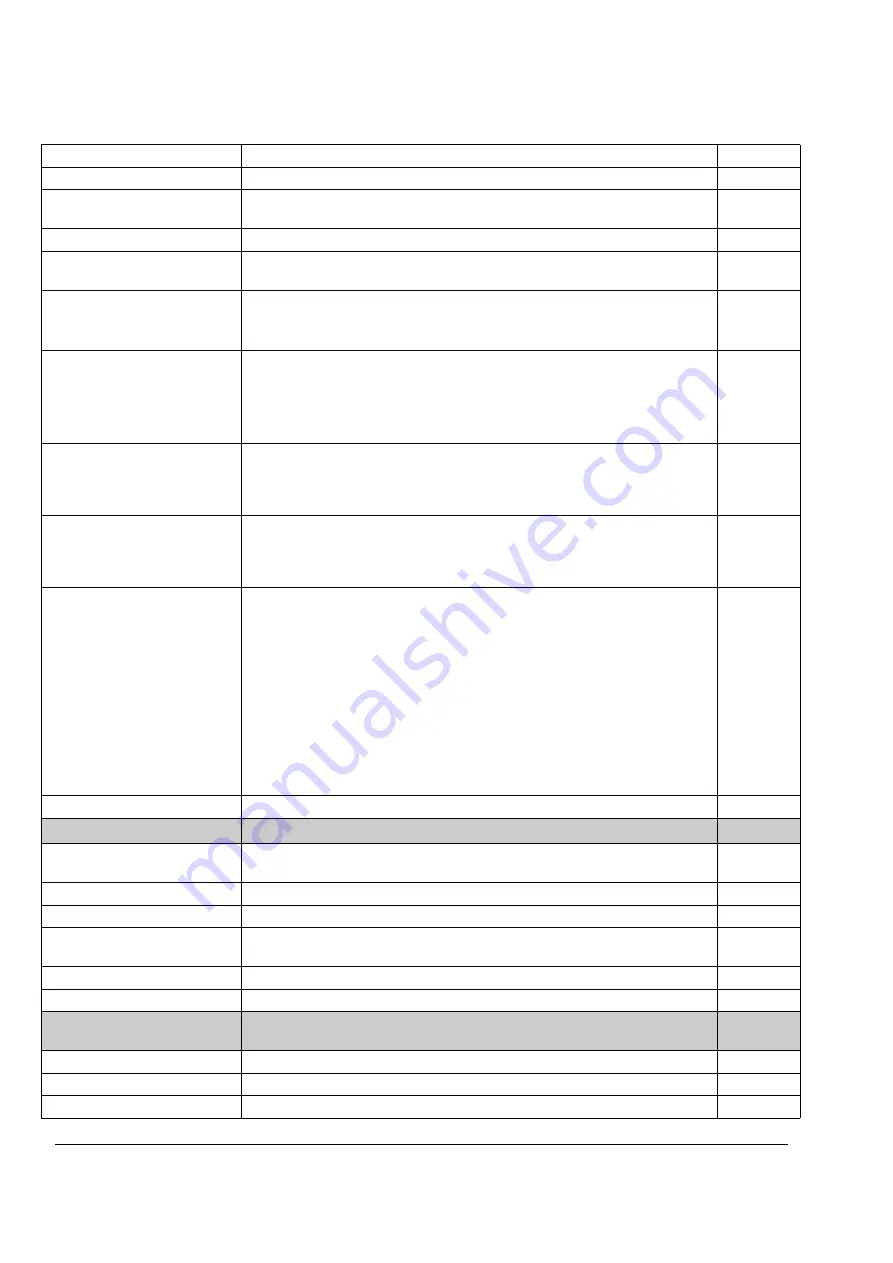
Actual signals and parameters
210
0 ... 100.0 rpm
Setting range in rpm
0 … 1000
78.09
SYNC ERR LIM
Defines the Synchro error limit which will be used if configured as Follower
drive for the SYNC FAULT fault generation. See Par.
0 ... 100.0 mm
Setting range in mm
0 … 1000
78.10
HOME POSITION
Defines the initial position value when a homing acknowledgment is done
using Par.
selection. The actual position is initialized to this value.
-1000000.0 ...
1000000.0 mm
Setting range in mm
Note:
When using the Fieldbus communication to write to this parameter the
value would be limited to -32768 … 32767
-1000000
… 1000000
78.12
SYNC CORR MODE
Defines the synchronisation correction mode to be used on the activation
Synchro command through the signal defined in Par.
Note
: The Synchro command should be reactivated using the signal defined in
Par.
SYNC SEL, after the synchronisation mode is changed from
OFFSET to DIRECT or from DIRECT to OFFSET.
OFFSET
The synchronisation correction is offset correction. In this mode, the difference
between the Master position and the Follower position at the time of Synchro
command activation is taken as an offset and is not considered as position
error.
0
DIRECT
The synchronisation correction is direct correction. In this mode, the difference
between the Master position and the Follower position at the time of Synchro
command activation is taken as position error. No permanent offset is
calculated in this mode.
1
78.13
POS HYSTERISIS
Defines the position hysteresis for stopping sequence in synchronisation
mode. This parameter is applicable only for Follower drives in synchronisation
mode. The drive is stopped only when the absolute Synchro position error Par.
SYNC POS ERROR is in this range. When the brake control is active the
drive issues a brake Closing command while in stopping sequence, only when
the Master drive brake has closed and the absolute Synchro position error
SYNC POS ERROR is within this hysteresis value. When brake control
is not active and the drive is a Follower, the drive stops only when the Master
drive stops and then the Synchro position error Par.
is within this hysteresis value.
Note:
When brake control is active the brake closing speed
ABS BRAKE
CLS SPD is not considered in this mode.
1.0 ... 50.0 mm
Setting range in mm
10 … 500
79 SERVICE COUNTER
Settings for Service Counter.
79.01
BRAKE CTR RESET
Reset selection of brake open counts. Used to reset the brake open count
value. Reset clears the value of signal
NO
No reset
0
RESET
Resets the counter. Automatically reverts back to 0.
1
79.02
RESET OPT TIME
Crane operation time reset selection. Used to reset the crane operation timer
value. Reset clears the value of signal
NO
No reset
0
RESET
Reset value. Automatically reverts back to 0.
1
83 ADAPT PROG CTRL
Control of the Adaptive Program execution. For more information, see the
Adaptive Program Application Guide
[3AFE64527274 (English)].
83.01
ADAPT PROG CMD
Selects the operation mode for the Adaptive Program.
STOP
Stop. The program cannot be edited.
1
RUN
Run. The program cannot be edited.
2
Index
Name/Selection
Description
FbEq
Содержание ACS 800 Series
Страница 1: ...ACS800 Firmware Manual Crane Control Program N697 ...
Страница 4: ......
Страница 26: ...Start up and control through the I O interface 26 ...
Страница 36: ...Quick start up guide 36 ...
Страница 52: ...Control panel 52 ...
Страница 105: ...Program features 105 Figure Control diagram for Shaft synchronisation executed in 20 ms ...
Страница 126: ...Program features 126 The figures below show speed limits according to different load conditions ...
Страница 128: ...Program features 128 ...
Страница 150: ...Application macros control location EXT1 EXT2 150 ...
Страница 228: ...Actual signals and parameters 228 ...
Страница 299: ...Adaptive Programming examples for crane control 299 ...
Страница 305: ...Adaptive Programming examples for crane control 305 ...
Страница 312: ...Adaptive Programming examples for crane control 312 The following figures show the previous example enlarged ...
Страница 314: ...Adaptive Programming examples for crane control 314 The following figures show the previous example enlarged ...
Страница 318: ...Analogue Extension Module 318 ...
Страница 332: ...Additional data actual signals and parameters 332 ...
Страница 333: ...DriveWindow 333 DriveWindow DriveWindow connected to the ACS800 RMIO RDCO board and channel CH3 ...
Страница 334: ...DriveWindow 334 ...
Страница 335: ...Control block diagrams 335 Control block diagrams ...
Страница 336: ...Control block diagrams 336 ...
Страница 337: ...Control block diagrams 337 ...
Страница 338: ...Control block diagrams 338 ...
Страница 340: ...www abb com drives www abb com drivespartners Contact us 3AFE68775230 Rev E EN 2012 09 25 ...