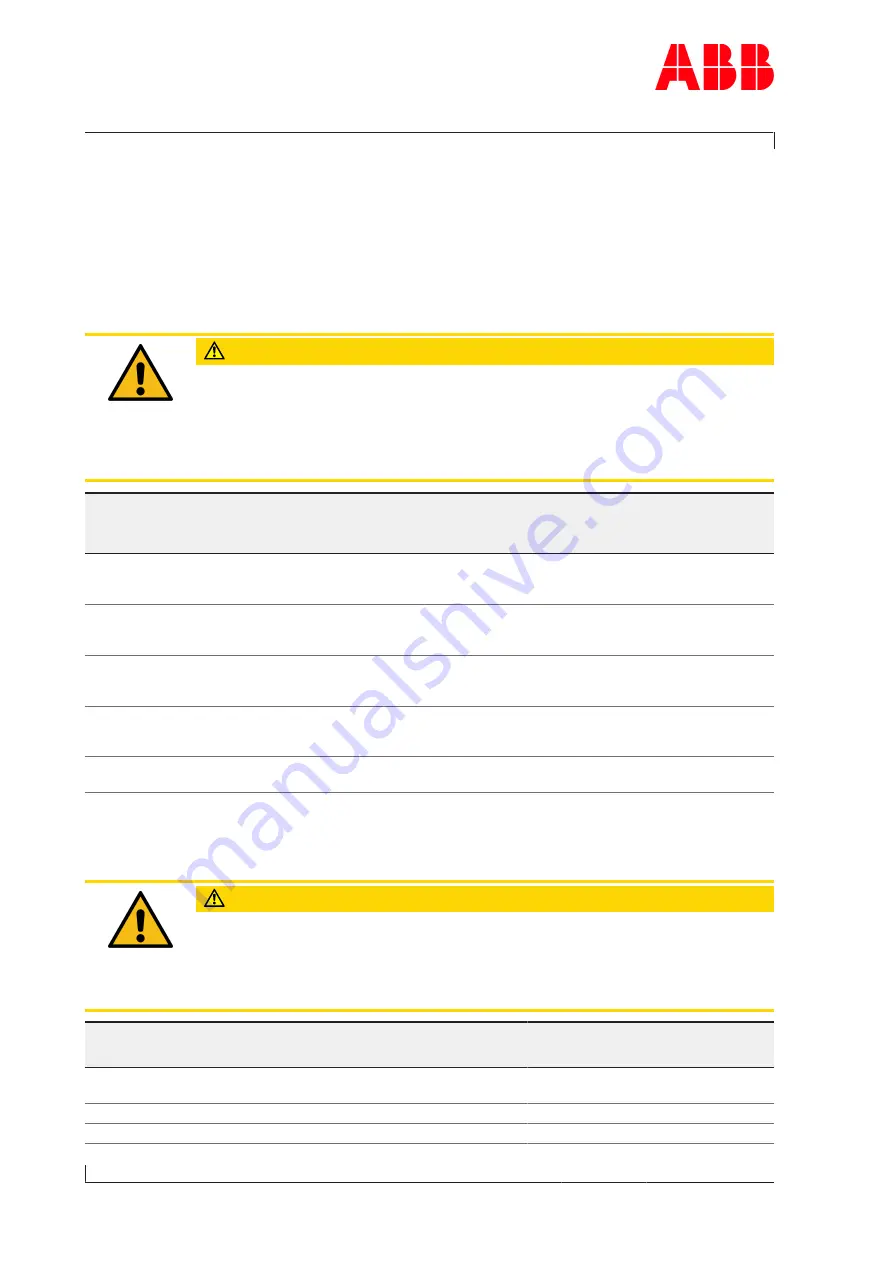
Operation Manual / 4 Product description / A100-L
4 Monitoring during operation / 4.1 Oil pressure, oil temperature
© Copyright 2020 ABB. All rights reserved.
HZTL4034_EN
Rev.P
January 2020
4
Monitoring during operation
4.1
Oil pressure, oil temperature
Lubricating oil pressure before turbocharger
CAUTION
Assuring lubricating oil pressure
Serious damage to the engine or property can result from a missing or insuf-
ficient lubricating oil supply.
u
The lubricating oil pressure must be monitored during operation and the
necessary pressure assured at the oil inlet.
Status for operation
Oil pressure before tur-
bocharger
[bar]
Admissible for normal operation,
with an oil temperature range at the inlet of 30 … 65 °C
with an oil temperature range at the inlet of 65 … 80 °C
0.8 … 2.5
1.0 … 2.0
Admissible during engine warm-up,
with an oil temperature range at the inlet of 30 … 65 °C
with an oil temperature range at the inlet of 65 … 80 °C
0.8 … 4.0
1.0 … 4.0
Temporarily admissible ( < 1 h )
→
alarm
with an oil temperature range at the inlet of 30 … 65 °C
with an oil temperature range at the inlet of 65 … 85 °C
0.6 … 0.8
0.8 … 1.0
Not admissible
→
emergency stop
with an oil temperature range at the inlet of 30 … 65 °C
with an oil temperature range at the inlet of 65 … 85 °C
< 0.6
< 0.8
Admissible, during pre-lubrication and post-lubrication (engine
stopped)
0.2 … 0.6
Table 6: Lubricating oil pressure, oil inlet
Lubricating oil temperature at the inlet
CAUTION
Machine damage
If the oil temperature at the oil inlet exceeds the admissible range, this may
lead to engine damage.
u
Observe oil temperature at the oil inlet according to the following table.
Status for operation
Oil temperature at the inlet
T
oil,inlet
[°C]
Admissible
(see Table 6: Lubricating oil pressure, oil inlet
30 … 80
Temporarily admissible (< 1 h)
→
alarm
> 80
Not admissible
→
stop engine
> 85
Page
16
/
112